- AS
1. AS prestasie
AS is 'n propileen-stireen kopolimeer, ook genoem SAN, met 'n digtheid van ongeveer 1.07g/cm3. Dit is nie geneig tot interne stres krake nie. Dit het hoër deursigtigheid, hoër versagtingstemperatuur en impaksterkte as PS, en swakker vermoeiingsweerstand.
2. Toepassing van AS
Bakkies, koppies, eetgerei, yskaskompartemente, knoppe, beligtingsbykomstighede, ornamente, instrumentspieëls, verpakkingsbokse, skryfbehoeftes, gasaanstekers, tandeborselhandvatsels, ens.
3. AS verwerkingstoestande
Die verwerkingstemperatuur van AS is oor die algemeen 210 ~ 250 ℃. Hierdie materiaal absorbeer maklik vog en moet vir meer as een uur gedroog word voor verwerking. Die vloeibaarheid daarvan is effens erger as PS, so die inspuitdruk is ook effens hoër, en die vormtemperatuur word beheer op 45 ~ 75 ℃ is beter.
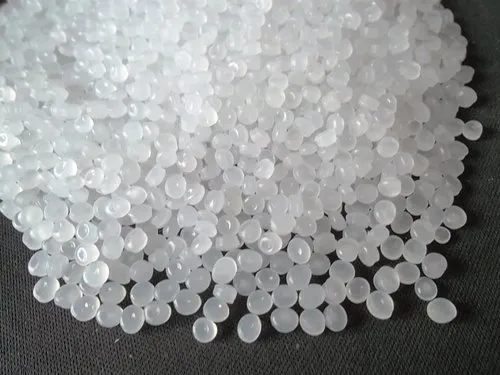
- ABS
1. ABS prestasie
ABS is akrilonitril-butadieen-styreen terpolimeer. Dit is 'n amorfe polimeer met 'n digtheid van ongeveer 1,05 g/cm3. Dit het 'n hoë meganiese sterkte en goeie omvattende eienskappe van "vertikaal, taai en staal". ABS is 'n algemeen gebruikte ingenieursplastiek met verskeie variëteite en wye gebruike. Dit word ook "algemene ingenieursplastiek" genoem (MBS word deursigtige ABS genoem). Dit is maklik om te vorm en te verwerk, het swak chemiese weerstand, en die produkte is maklik om te elektroplateer.
2. Toepassing van ABS
Pompwaaiers, laers, handvatsels, pype, elektriese toestelomhulsels, elektroniese produkonderdele, speelgoed, horlosiekaste, instrumentkaste, watertenkomhulsels, koelstoor en yskasbinneomhulsels.
3. ABS proses eienskappe
(1) ABS het hoë higroskopisiteit en swak temperatuurweerstand. Dit moet volledig gedroog en voorverhit word voor giet en verwerking om die voginhoud onder 0,03% te beheer.
(2) Die smeltviskositeit van ABS-hars is minder sensitief vir temperatuur (anders as ander amorfe harse). Alhoewel die inspuittemperatuur van ABS effens hoër is as dié van PS, het dit nie 'n losser temperatuurstygbereik soos PS nie, en blinde verhitting kan nie gebruik word nie. Om sy viskositeit te verminder, kan jy die skroefspoed verhoog of die inspuitdruk/spoed verhoog om sy vloeibaarheid te verbeter. Die algemene verwerkingstemperatuur is 190 ~ 235 ℃.
(3) Die smeltviskositeit van ABS is medium, hoër as dié van PS, HIPS en AS, en die vloeibaarheid daarvan is swakker, dus word hoër inspuitdruk vereis.
(4) ABS het 'n goeie effek met medium tot medium inspuitspoed (tensy komplekse vorms en dun dele hoër inspuitspoed vereis), is die mondstuk van die produk geneig tot lugmerke.
(5) ABS-vormtemperatuur is relatief hoog, en sy vormtemperatuur word gewoonlik tussen 45 en 80 °C aangepas. Wanneer groter produkte vervaardig word, is die temperatuur van die vaste vorm (voorvorm) oor die algemeen ongeveer 5°C hoër as dié van die beweegbare vorm (agterste vorm).
(6) ABS moet nie te lank in die hoë-temperatuur vat bly nie (moet minder as 30 minute wees), anders sal dit maklik ontbind en geel word.
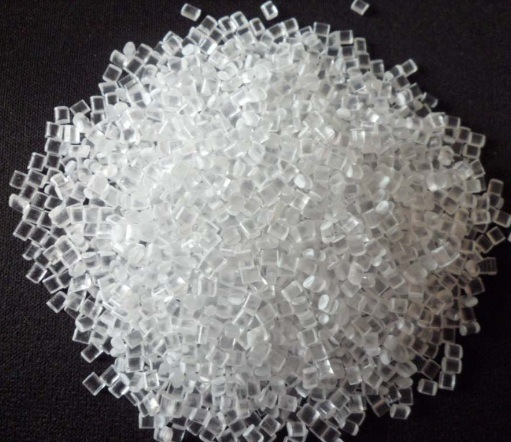
- PMMA
1. Prestasie van PMMA
PMMA is 'n amorfe polimeer, algemeen bekend as plexiglas (sub-akriel), met 'n digtheid van ongeveer 1.18g/cm3. Dit het uitstekende deursigtigheid en 'n ligoordrag van 92%. Dit is 'n goeie optiese materiaal; dit het goeie hitteweerstand (hitteweerstand). Die vervormingstemperatuur is 98°C). Die produk het medium meganiese sterkte en lae oppervlak hardheid. Dit word maklik deur harde voorwerpe gekrap en laat spore. In vergelyking met PS is dit nie maklik om bros te wees nie.
2. Toepassing van PMMA
Instrumentlense, optiese produkte, elektriese toestelle, mediese toerusting, deursigtige modelle, versierings, sonlense, kunsgebitte, advertensieborde, horlosiepanele, motor se agterligte, voorruite, ens.
3. Proseskenmerke van PMMA
Die verwerkingsvereistes van PMMA is streng. Dit is baie sensitief vir vog en temperatuur. Dit moet volledig gedroog word voor verwerking. Die smeltviskositeit is relatief hoog, dus moet dit by 'n hoër temperatuur (219 ~ 240 ℃) en druk gevorm word. Die vorm temperatuur is tussen 65 ~ 80 ℃ is beter. Die termiese stabiliteit van PMMA is nie baie goed nie. Dit sal afgebreek word deur hoë temperatuur of om te lank by 'n hoër temperatuur te bly. Die skroefspoed moet nie te hoog wees nie (ongeveer 60rpm), aangesien dit maklik in dikker PMMA-onderdele voorkom. Die "leegte"-verskynsel vereis groot hekke en "hoë materiaaltemperatuur, hoë vormtemperatuur, stadige spoed" inspuittoestande om te verwerk.
4. Wat is akriel (PMMA)?
Akriel (PMMA) is 'n deursigtige, harde plastiek wat dikwels in die plek van glas gebruik word in produkte soos breekvaste vensters, verligte tekens, dakvensters en vliegtuigafdakke. PMMA behoort aan die belangrike familie van akrielharse. Die chemiese naam van akriel is polimetielmetakrilaat (PMMA), wat 'n sintetiese hars is wat uit metielmetakrilaat gepolimeer is.
Polimetielmetakrilaat (PMMA) staan ook bekend as akriel, akrielglas, en is onder andere beskikbaar onder handelsname en handelsmerke soos Crylux, Plexiglas, Acrylite, Perclax, Astariglas, Lucite en Perspex. Polimetielmetakrilaat (PMMA) word dikwels in plaatvorm gebruik as 'n liggewig of breekvaste alternatief vir glas. PMMA word ook gebruik as 'n giethars, ink en deklaag. PMMA is deel van die ingenieursplastiekmateriaalgroep.
5. Hoe word akriel gemaak?
Polimetielmetakrilaat word deur polimerisasie gemaak aangesien dit een van die sintetiese polimere is. Eerstens word metielmetakrilaat in die vorm geplaas en 'n katalisator word bygevoeg om die proses te bespoedig. As gevolg van hierdie polimerisasieproses kan PMMA in verskillende vorms gevorm word soos velle, harse, blokke en krale. Akrielgom kan ook help om die PMMA-stukke sag te maak en aanmekaar te sweis.
PMMA is maklik om op verskillende maniere te manipuleer. Dit kan met ander materiale gebind word om die eienskappe daarvan te verbeter. Met termovorming word dit buigsaam wanneer dit verhit word en stol wanneer dit afgekoel word. Dit kan die regte grootte met 'n saag of lasersny gebruik. As dit gepoleer is, kan jy skrape van die oppervlak verwyder en help om die integriteit daarvan te behou.
6. Wat is die verskillende tipes akriel?
Die twee hooftipes akrielplastiek is gegote akriel en geëxtrudeerde akriel. Gegote akriel is duurder om te vervaardig, maar het 'n beter sterkte, duursaamheid, helderheid, termovormbereik en stabiliteit as geëxtrudeerde akriel. Gegote akriel bied uitstekende chemiese weerstand en duursaamheid, en is maklik om in te kleur en te vorm tydens die vervaardigingsproses. Gegote akriel is ook beskikbaar in 'n verskeidenheid diktes. Geëxtrudeerde akriel is meer ekonomies as gegote akriel en bied meer konsekwente, werkbare akriel as gegote akriel (ten koste van verminderde sterkte). Geëxtrudeerde akriel is maklik om te verwerk en te masjien, wat dit 'n uitstekende alternatief vir glasplate in toepassings maak.
7. Waarom word akriel so algemeen gebruik?
Akriel word dikwels gebruik omdat dit dieselfde voordelige eienskappe as glas het, maar sonder die brosheidsprobleme. Akrielglas het uitstekende optiese eienskappe en het dieselfde brekingsindeks as glas in die vaste toestand. As gevolg van sy splintervaste eienskappe, kan ontwerpers akriel gebruik op plekke waar glas te gevaarlik sou wees of andersins sou misluk (soos duikboot-periskope, vliegtuigvensters, ens.). Byvoorbeeld, die mees algemene vorm van koeëlvaste glas is 'n 1/4-duim-dik stuk akriel, genaamd soliede akriel. Akriel vaar ook goed in spuitgiet en kan gevorm word in byna enige vorm wat 'n vormmaker kan skep. Die sterkte van akrielglas gekombineer met die gemak van verwerking en bewerking maak dit 'n uitstekende materiaal, wat verduidelik hoekom dit wyd in verbruikers- en kommersiële nywerhede gebruik word.
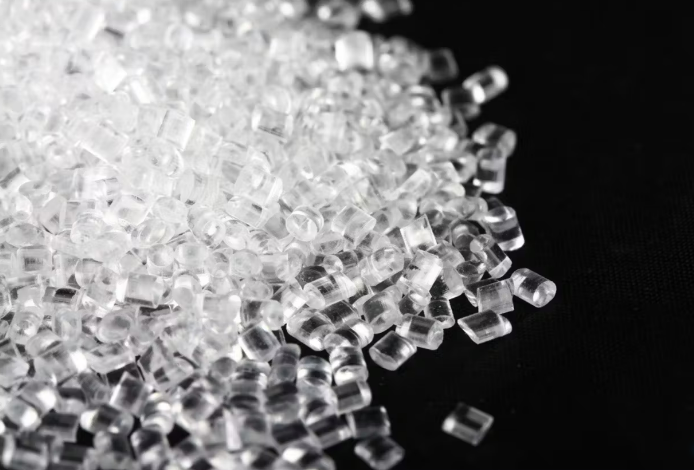
Postyd: 13 Desember 2023