Hoekom produseer skermdruk kleure? As ons die mengsel van verskeie kleure opsy sit en slegs een kleur oorweeg, kan dit makliker wees om die oorsake van kleurverspreiding te bespreek. Hierdie artikel deel verskeie faktore wat kleurafwyking in skermdrukwerk beïnvloed. Die inhoud is vir verwysing deur vriende wat die Youpin-verpakkingsmateriaalstelsel koop en verskaf:
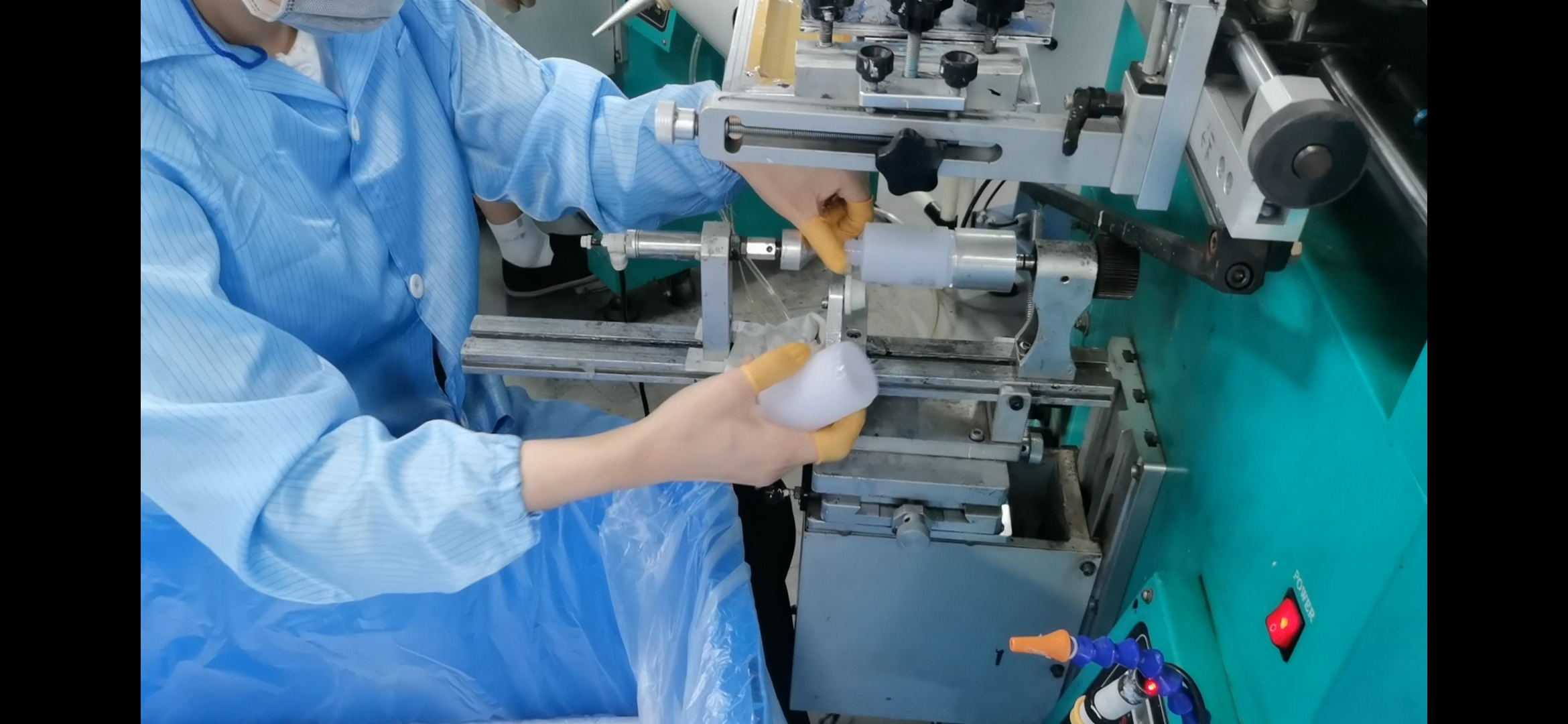
Hoekom produseer skermdruk kleure? As ons die mengsel van verskeie kleure opsy sit en slegs een kleur oorweeg, kan dit makliker wees om die oorsake van kleurverspreiding te bespreek. Hierdie artikel deel verskeie faktore wat kleurafwyking in skermdrukwerk beïnvloed. Die inhoud is vir verwysing deur vriende wat die Youpin-verpakkingsmateriaalstelsel koop en verskaf:
Hieronder is 'n paar van die mees algemene faktore wat kleurafwyking in sifdruk veroorsaak: inkvoorbereiding, maaskeuse, maasspanning, druk, droging, substraatkenmerke, waarnemingstoestande, ens.
01 Ink voorbereiding
Inkvermenging As aanvaar word dat die pigment van die ink wat gebruik word 'n standaardpigment is, is die grootste oorsaak van kleurafwyking die byvoeging van oplosmiddels soos inkmengolie by die ink. In 'n werkswinkel met goeie kleurbeheertoerusting kan ink volgens die beheertoerusting gemeng word. Vir die meeste drukkerye is dit egter onmoontlik om hierdie fasiliteite te hê. Hulle maak slegs staat op die ervaring van die meesterwerkers wanneer ink gemeng word.
Oor die algemeen word inkaanpassingsolie bygevoeg om die ink meer geskik vir drukwerk te maak. Sodra aanpassingsolie egter by die ink gevoeg is, sal die konsentrasie van pigmente in die ink verander, wat sal lei tot veranderinge in die kleureienskappe van die ink tydens druk. Daarbenewens sal oortollige oplosmiddel in die ink 'n dun film ink vorm na droog, wat die helderheid van die kleur sal verminder.
Daar is ook die probleem dat ink verdun word voor ink. Werkers in die inkwinkel maak byvoorbeeld oordeel op grond van hul formule wanneer ink gemeng of verdun word. Dit lei tot onvermydelike kleurafwyking. As die ink 'n paar dae gelede gemeng is, As jy met goeie ink druk, sal die kleur wat deur hierdie situasie veroorsaak word meer duidelik wees. Daarom is dit byna onmoontlik om kleurverspreiding heeltemal te vermy.
02 Maas seleksie
As jy dink dat die maasgrootte van die skerm die enigste faktor is wat inkoordrag beïnvloed, sal jy baie probleme ondervind. Maasdeursnee en plooie beïnvloed ook inkoordrag. Oor die algemeen, hoe meer ink aan die inkgate van die skerm geheg word, hoe meer ink sal tydens die drukproses na die substraat oorgedra word.
Om vooraf te skat hoeveel ink deur elke maas oorgedra kan word, verskaf baie skermverskaffers die teoretiese inkoordragvolume (TIV) van elke maas. TIV is 'n parameter wat die grootte van die inkoordraghoeveelheid van die skerm aandui. Dit verwys na die hoeveelheid ink wat in 'n sekere hoeveelheid ink oorgedra word deur elke maas onder spesifieke druktoestande. Die eenheid daarvan is die volume ink per eenheidsoppervlakte.
Om konsekwente kleure in drukwerk te verseker, is dit nie genoeg om die maasnommer van die skerm onveranderd te hou nie, maar ook om te verseker dat die deursnee van die skerm en sy golwing konstant bly. Veranderinge in enige parameter van die skerm sal lei tot veranderinge in die dikte van die inkfilm tydens druk, wat lei tot kleurveranderinge.
03 Netto spanning
As die spanning van die net te klein is, sal dit die film laat afdop. As daar te veel ink in die maas bly, sal die drukwerk vuil word.
Hierdie probleem kan opgelos word deur die afstand tussen die skerm en die substraat te vergroot. Die verhoging van die afstand tussen die skerm en die substraat vereis egter dat die druk verhoog word, wat sal veroorsaak dat meer ink na die substraat oorgedra word. om die digtheid van die kleur te verander. Die beste manier is om die spanning van die reknet eenvormig te hou om die konsekwentheid van die kleur te verseker.
04 Drukvlak
Behoorlike drukinstellings is van kardinale belang om konsekwente kleur te handhaaf, en om eenvormige drukvlakke tydens die drukproses te verseker, is van kritieke belang. Veral in hoëvolume, herhalende druktake.
Wanneer dit by druk kom, is die eerste ding om te oorweeg die hardheid van die squeegee. Die hardheid van die squeegee is klein, wat goed is vir die kontaktempo, maar dit is nie goed vir buigweerstand nie. As die hardheid te hoog is, sal die wrywing op die skerm ook groot wees tydens druk, wat dus die drukakkuraatheid beïnvloed. Die tweede is die hoek van die squeegee en die squeegee spoed. Die hoek van die inkmes het 'n beduidende impak op die hoeveelheid inkoordrag. Hoe kleiner die hoek van die inkmes, hoe groter is die hoeveelheid inkoordrag. As die spoed van die inkmes te vinnig is, sal dit onvoldoende inkvulling en onvolledige indruk veroorsaak, wat dus die kwaliteit van die druk beïnvloed.
Sodra jy die korrekte drukinstellings vir 'n druktaak verkry het en dit akkuraat aangeteken het, solank jy hierdie instellings korrek volg tydens die drukproses, sal jy 'n bevredigende drukproduk met konsekwente kleure kry.
05 droog
Soms lyk die kleur konsekwent net na druk, maar die kleur verander nadat die finale produk gevind is. Dit word dikwels veroorsaak deur verkeerde instellings van die droogtoerusting. Die mees algemene oorsaak is dat die droër se temperatuur te hoog gestel is, wat veroorsaak dat die inkkleur op die papier of karton verander.
06 Substraat eienskappe
Een kwessie wat skermdrukmeesters dikwels miskyk, is die oppervlak-eienskappe van die substraat. Papier, karton, plastiek, ens. word almal in bondels vervaardig, en hoë kwaliteit substrate kan stabiele en konsekwente oppervlak eienskappe verseker. Maar dit is nie die geval nie. Klein veranderinge in die oppervlak eienskappe van die substraat sal kleurafwykings in druk veroorsaak. Selfs as die drukdruk eenvormig is en selfs elke proses korrek uitgevoer word, sal teenstrydighede in die oppervlak eienskappe van die substraat ook groter kleurverskuiwings in druk veroorsaak. Kleur cast.
Wanneer dieselfde produk op verskillende substrate met dieselfde druktoerusting gedruk word, is die invloed van die oppervlak-eienskappe van die substraat op die kleur besonder duidelik. Kliënte mag vereis dat vensteradvertensies op plastiek of ander karton gedruk word. En kliënte kan konsekwente kleure vir dieselfde stuk benodig.
In situasies soos hierdie is die enigste oplossing om akkurate kleurmetings te maak. Gebruik 'n spektrofotometer of spektrale densitometer om kleurdigtheid te meet. As daar 'n kleurverskuiwing is, kan die densitometer dit duidelik weerspieël, en jy kan hierdie kleurverskuiwing oorkom deur ander prosesse te beheer.
07 Waarnemingstoestande
Menslike oë is baie sensitief vir subtiele veranderinge in kleur, en kan kleure slegs onder beligtingstoestande onderskei. As gevolg hiervan, maak seker dat u kleure onder dieselfde beligtingstoestande vergelyk. Andersins sal die aanpassing van die inkvolume of druk meer ink produseer. Groot kleurslag.
Al met al lê die sleutel tot die handhawing van konsekwente kleur in die stabiele beheer van elke proses om stabiele werkverrigting van die ink te verseker. Die keuse van maasgrootte, spanning en druk van die rekskerm, oppervlakkenmerke van die substraat en waarnemingstoestande het alles 'n sekere impak op kleurafwyking. Akkurate opstelrekords en stabiele beheer van elke proses is egter die sleutels om konsekwente skermdrukkleure te verseker.
Postyd: Jan-08-2024