কেন স্ক্রিন প্রিন্টিং কালার কাস্ট তৈরি করে? আমরা যদি বিভিন্ন রঙের মিশ্রণকে একপাশে রাখি এবং শুধুমাত্র একটি রঙ বিবেচনা করি, তাহলে রঙ নিক্ষেপের কারণগুলি নিয়ে আলোচনা করা সহজ হতে পারে। এই নিবন্ধটি স্ক্রিন প্রিন্টিং-এ রঙের বিচ্যুতিকে প্রভাবিত করে এমন কয়েকটি বিষয় শেয়ার করে। বিষয়বস্তুটি বন্ধুদের রেফারেন্সের জন্য যারা Youpin প্যাকেজিং উপাদান সিস্টেম ক্রয় এবং সরবরাহ করে:
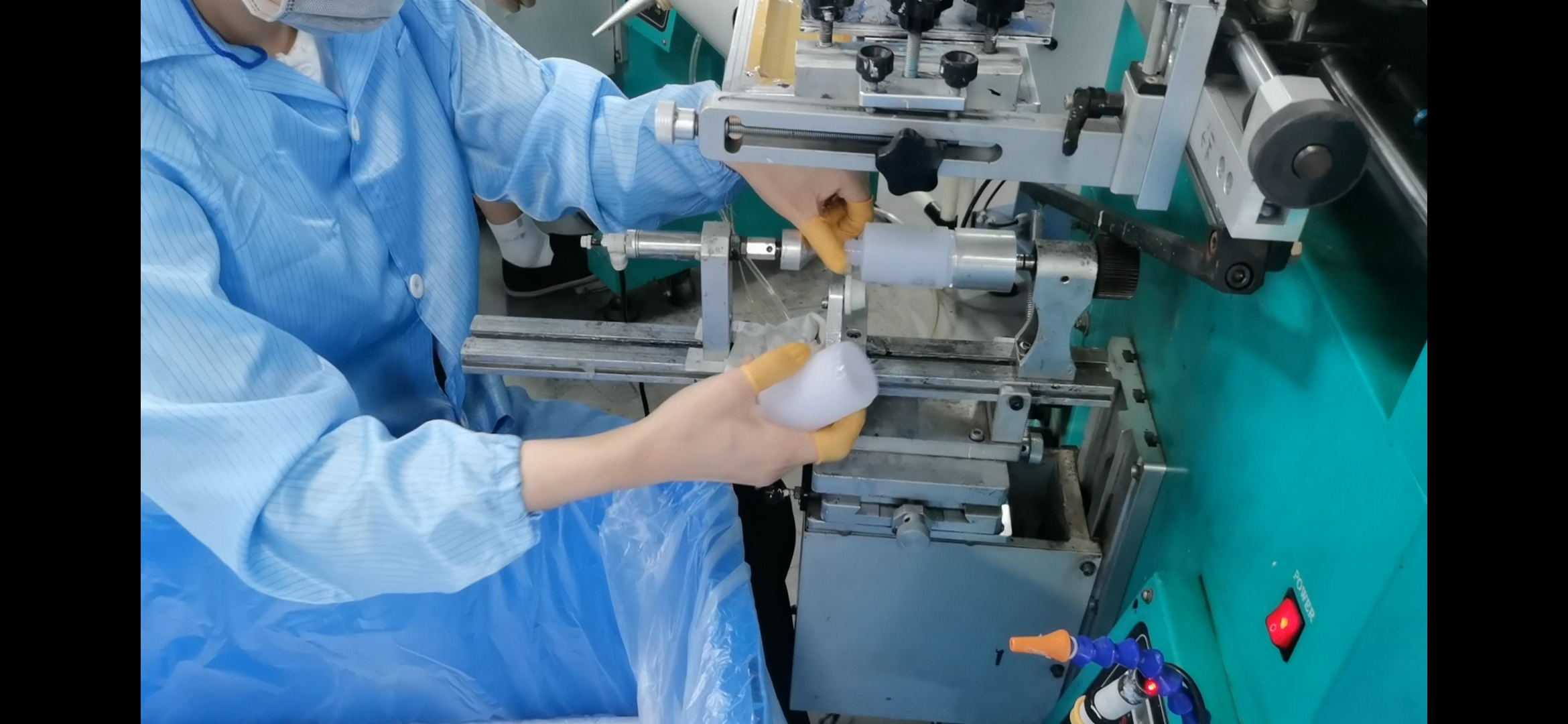
কেন স্ক্রিন প্রিন্টিং কালার কাস্ট তৈরি করে? আমরা যদি বিভিন্ন রঙের মিশ্রণকে একপাশে রাখি এবং শুধুমাত্র একটি রঙ বিবেচনা করি, তাহলে রঙ নিক্ষেপের কারণগুলি নিয়ে আলোচনা করা সহজ হতে পারে। এই নিবন্ধটি স্ক্রিন প্রিন্টিং-এ রঙের বিচ্যুতিকে প্রভাবিত করে এমন কয়েকটি বিষয় শেয়ার করে। বিষয়বস্তুটি বন্ধুদের রেফারেন্সের জন্য যারা Youpin প্যাকেজিং উপাদান সিস্টেম ক্রয় এবং সরবরাহ করে:
স্ক্রিন প্রিন্টিং-এ রঙের বিচ্যুতি ঘটায় এমন কিছু সাধারণ কারণ নীচে তালিকাভুক্ত করা হল: কালি তৈরি, জাল নির্বাচন, জাল টান, চাপ, শুকানো, স্তর বৈশিষ্ট্য, পর্যবেক্ষণ শর্ত ইত্যাদি।
01 কালি প্রস্তুতি
কালি মিশ্রন অনুমান করা হয় যে ব্যবহৃত কালির রঙ্গকটি একটি আদর্শ রঙ্গক, রঙের বিচ্যুতির সবচেয়ে বড় কারণ হল কালির সাথে কালি মেশানো তেলের মতো দ্রাবক যোগ করা। ভাল রঙ নিয়ন্ত্রণ সরঞ্জাম সহ একটি কর্মশালায়, নিয়ন্ত্রণ সরঞ্জাম অনুযায়ী কালি মিশ্রিত করা যেতে পারে। যাইহোক, বেশিরভাগ মুদ্রণ সংস্থার জন্য, এই সুবিধাগুলি থাকা অসম্ভব। কালি মেশানোর সময় তারা শুধুমাত্র মাস্টার কর্মীদের অভিজ্ঞতার উপর নির্ভর করে।
সাধারণত, কালিকে ছাপার জন্য আরও উপযুক্ত করতে কালি-সামঞ্জস্যকারী তেল যোগ করা হয়। যাইহোক, একবার কালিতে তেল যোগ করা হলে, কালিতে রঙ্গকগুলির ঘনত্ব পরিবর্তিত হবে, যা মুদ্রণের সময় কালির রঙের বৈশিষ্ট্যে পরিবর্তন আনবে। এছাড়াও, কালিতে অতিরিক্ত দ্রাবক শুকানোর পরে কালির একটি পাতলা ফিল্ম তৈরি করবে, যা রঙের উজ্জ্বলতা হ্রাস করবে।
কালি দেওয়ার আগে কালি মিশ্রিত হওয়ার সমস্যাও রয়েছে। উদাহরণস্বরূপ, কালির দোকানের কর্মীরা কালি মেশানো বা পাতলা করার সময় তাদের সূত্রের উপর ভিত্তি করে রায় দেয়। এটি অনিবার্য রঙের বিচ্যুতির দিকে পরিচালিত করে। যদি কালি কয়েক দিন আগে মিশ্রিত হয়, আপনি যদি ভাল কালি দিয়ে মুদ্রণ করেন, তাহলে এই পরিস্থিতির কারণে রঙের ঢালাই আরও স্পষ্ট হবে। অতএব, রঙ ঢালাই সম্পূর্ণরূপে এড়ানো প্রায় অসম্ভব।
02 জাল নির্বাচন
আপনি যদি মনে করেন যে পর্দার জালের আকারই একমাত্র কারণ যা কালি স্থানান্তরকে প্রভাবিত করে, আপনি অনেক সমস্যায় পড়বেন। জাল ব্যাস এবং wrinkles এছাড়াও কালি স্থানান্তর প্রভাবিত. সাধারণত, স্ক্রিনের কালি গর্তের সাথে যত বেশি কালি যুক্ত হবে, মুদ্রণ প্রক্রিয়ার সময় তত বেশি কালি সাবস্ট্রেটে স্থানান্তরিত হবে।
প্রতিটি জাল দ্বারা কতটা কালি স্থানান্তর করা যেতে পারে তা আগাম অনুমান করার জন্য, অনেক স্ক্রীন সরবরাহকারী প্রতিটি জালের তাত্ত্বিক কালি স্থানান্তর ভলিউম (TIV) প্রদান করে। TIV হল একটি প্যারামিটার যা স্ক্রিনের কালি স্থানান্তরের পরিমাণ নির্দেশ করে। এটি নির্দিষ্ট প্রিন্টিং অবস্থার অধীনে প্রতিটি জাল দ্বারা কতটা কালি স্থানান্তরিত হবে তা নির্দিষ্ট সময়ে স্থানান্তরিত কালির পরিমাণ বোঝায়। এর একক হল প্রতি ইউনিট এলাকায় কালির আয়তন।
মুদ্রণে সামঞ্জস্যপূর্ণ টোন নিশ্চিত করার জন্য, পর্দার জাল সংখ্যা অপরিবর্তিত রাখা যথেষ্ট নয়, তবে পর্দার ব্যাস এবং এর তরঙ্গায়িততা স্থির থাকে তাও নিশ্চিত করা। স্ক্রিনের যেকোনো প্যারামিটারে পরিবর্তনের ফলে মুদ্রণের সময় কালি ফিল্মের পুরুত্বের পরিবর্তন হবে, ফলে রঙ পরিবর্তন হবে।
03 নেট টেনশন
যদি নেটের টান খুব ছোট হয় তবে এটি ফিল্মটিকে খোসা ছাড়িয়ে দেবে। যদি জালের মধ্যে খুব বেশি কালি থাকে তবে মুদ্রিত জিনিসটি নোংরা হয়ে যাবে।
স্ক্রীন এবং সাবস্ট্রেটের মধ্যে দূরত্ব বাড়িয়ে এই সমস্যাটি সমাধান করা যেতে পারে। যাইহোক, স্ক্রীন এবং সাবস্ট্রেটের মধ্যে দূরত্ব বাড়ানোর জন্য চাপ বাড়াতে হবে, যার ফলে সাবস্ট্রেটে আরও কালি স্থানান্তরিত হবে। রঙের ঘনত্ব পরিবর্তন করতে। সর্বোত্তম উপায় হল স্ট্রেচ নেট এর টান সমান রাখা, যাতে রঙের সামঞ্জস্য নিশ্চিত করা যায়।
04 চাপ স্তর
সঙ্গতিপূর্ণ রঙ বজায় রাখার জন্য সঠিক চাপ সেটিংস অত্যন্ত গুরুত্বপূর্ণ, এবং মুদ্রণ প্রক্রিয়া চলাকালীন অভিন্ন চাপের মাত্রা নিশ্চিত করা গুরুত্বপূর্ণ। বিশেষ করে উচ্চ ভলিউম, পুনরাবৃত্তিমূলক মুদ্রণ কাজ.
যখন চাপের কথা আসে, তখন বিবেচনা করা প্রথম জিনিসটি হল স্কুইজির কঠোরতা। স্কুইজির কঠোরতা ছোট, যা যোগাযোগের হারের জন্য ভাল, তবে এটি নমন প্রতিরোধের জন্য ভাল নয়। যদি কঠোরতা খুব বেশি হয়, তাহলে মুদ্রণের সময় পর্দার ঘর্ষণও বড় হবে, এইভাবে মুদ্রণের সঠিকতাকে প্রভাবিত করবে। দ্বিতীয়টি হল squeegee এবং squeegee গতির কোণ। কালি ছুরির কোণটি কালি স্থানান্তরের পরিমাণের উপর একটি উল্লেখযোগ্য প্রভাব ফেলে। কালি ছুরির কোণ যত ছোট হবে, কালি স্থানান্তরের পরিমাণ তত বেশি হবে। যদি কালি ছুরির গতি খুব দ্রুত হয় তবে এটি অপর্যাপ্ত কালি ভরাট এবং অসম্পূর্ণ ছাপের কারণ হবে, এইভাবে মুদ্রণের গুণমানকে প্রভাবিত করবে।
একবার আপনি একটি মুদ্রণ কাজের জন্য সঠিক চাপ সেটিংস পেয়ে গেলে এবং সেগুলিকে নির্ভুলভাবে রেকর্ড করলে, যতক্ষণ না আপনি মুদ্রণ প্রক্রিয়া চলাকালীন এই সেটিংসগুলি সঠিকভাবে অনুসরণ করেন, আপনি সামঞ্জস্যপূর্ণ রঙের সাথে একটি সন্তোষজনক মুদ্রণ পণ্য পাবেন।
05 শুকনো
কখনও কখনও, মুদ্রণের পরে রঙটি সামঞ্জস্যপূর্ণ দেখায়, তবে সমাপ্ত পণ্যটি পাওয়া যাওয়ার পরে রঙ পরিবর্তন হয়। এটি প্রায়শই শুকানোর সরঞ্জামগুলির ভুল সেটিংসের কারণে ঘটে। সবচেয়ে সাধারণ কারণ হল ড্রায়ারের তাপমাত্রা খুব বেশি সেট করা হয়, যার ফলে কাগজ বা কার্ডবোর্ডের কালি রঙ পরিবর্তন হয়।
06 সাবস্ট্রেট বৈশিষ্ট্য
একটি সমস্যা যা স্ক্রিন প্রিন্টিং মাস্টাররা প্রায়শই উপেক্ষা করে তা হল সাবস্ট্রেটের পৃষ্ঠের বৈশিষ্ট্য। কাগজ, পিচবোর্ড, প্লাস্টিক, ইত্যাদি সবই ব্যাচে উত্পাদিত হয় এবং উচ্চ-মানের সাবস্ট্রেটগুলি স্থিতিশীল এবং সামঞ্জস্যপূর্ণ পৃষ্ঠের বৈশিষ্ট্যগুলি নিশ্চিত করতে পারে। কিন্তু ব্যাপারটা এমন নয়। সাবস্ট্রেটের পৃষ্ঠের বৈশিষ্ট্যে ছোট পরিবর্তন মুদ্রণে রঙের বিচ্যুতি ঘটাবে। এমনকি যদি মুদ্রণের চাপ অভিন্ন হয় এবং এমনকি প্রতিটি প্রক্রিয়া সঠিকভাবে পরিচালিত হয়, তবে সাবস্ট্রেটের পৃষ্ঠের বৈশিষ্ট্যগুলির অসঙ্গতিগুলিও মুদ্রণে বড় রঙের পরিবর্তন ঘটাবে। কালার কাস্ট।
যখন একই পণ্য একই মুদ্রণ সরঞ্জাম দিয়ে বিভিন্ন স্তরে মুদ্রিত হয়, তখন রঙের উপর সাবস্ট্রেটের পৃষ্ঠের বৈশিষ্ট্যগুলির প্রভাব বিশেষভাবে স্পষ্ট হয়। গ্রাহকদের প্লাস্টিক বা অন্যান্য কার্ডবোর্ডে মুদ্রিত উইন্ডো বিজ্ঞাপনের প্রয়োজন হতে পারে। এবং ক্লায়েন্টদের একই টুকরার জন্য সামঞ্জস্যপূর্ণ রঙের প্রয়োজন হতে পারে।
এই ধরনের পরিস্থিতিতে, একমাত্র সমাধান হল সঠিক রঙ পরিমাপ করা। রঙের ঘনত্ব পরিমাপ করতে একটি বর্ণালী ফোটোমিটার বা বর্ণালী ঘনত্ব মিটার ব্যবহার করুন। যদি রঙের পরিবর্তন হয়, তবে ঘনত্বের মিটার স্পষ্টভাবে এটিকে প্রতিফলিত করতে পারে এবং আপনি অন্যান্য প্রক্রিয়াগুলি নিয়ন্ত্রণ করে এই রঙের পরিবর্তনটি কাটিয়ে উঠতে পারেন।
07 পর্যবেক্ষণ শর্ত
মানুষের চোখ রঙের সূক্ষ্ম পরিবর্তনের জন্য খুব সংবেদনশীল, এবং শুধুমাত্র আলোর অবস্থাতেই রঙগুলিকে আলাদা করতে পারে। এই কারণে, একই আলো অবস্থার অধীনে রং তুলনা নিশ্চিত করুন. অন্যথায়, কালির ভলিউম বা চাপ সামঞ্জস্য করলে আরও কালি উৎপন্ন হবে। বড় রঙের ঢালাই।
সর্বোপরি, সামঞ্জস্যপূর্ণ রঙ বজায় রাখার মূল চাবিকাঠি প্রতিটি প্রক্রিয়ার স্থিতিশীল নিয়ন্ত্রণের মধ্যে রয়েছে যাতে কালির স্থিতিশীল কর্মক্ষমতা নিশ্চিত করা যায়। জালের আকার নির্বাচন, প্রসারিত পর্দার টান এবং চাপ, সাবস্ট্রেটের পৃষ্ঠের বৈশিষ্ট্য এবং পর্যবেক্ষণের অবস্থা সবই রঙের বিচ্যুতির উপর একটি নির্দিষ্ট প্রভাব ফেলে। যাইহোক, সঠিক সেটিং রেকর্ড এবং প্রতিটি প্রক্রিয়ার স্থিতিশীল নিয়ন্ত্রণ হল ধারাবাহিক স্ক্রিন প্রিন্টিং রং নিশ্চিত করার চাবিকাঠি।
পোস্টের সময়: জানুয়ারি-০৮-২০২৪