ABS, allgemein bekannt als Acrylnitril-Butadien-Styrol, entsteht durch die Copolymerisation von drei Monomeren aus Acrylnitril-Butadien-Styrol. Aufgrund der unterschiedlichen Anteile der drei Monomere kann es zu unterschiedlichen Eigenschaften und Schmelztemperaturen, Mobilitätsleistungen von ABS, Mischungen mit anderen Kunststoffen oder Additiven kommen, wodurch die Verwendung und Leistung von ABS erweitert werden kann.
Die Fließfähigkeit von ABS liegt zwischen PS und PC und ihre Fließfähigkeit hängt von der Einspritztemperatur und dem Einspritzdruck ab, wobei der Einfluss des Einspritzdrucks etwas größer ist. Daher wird beim Formen häufig ein höherer Einspritzdruck verwendet, um die Schmelzviskosität zu verringern und die Formfüllung zu verbessern. Leistung.
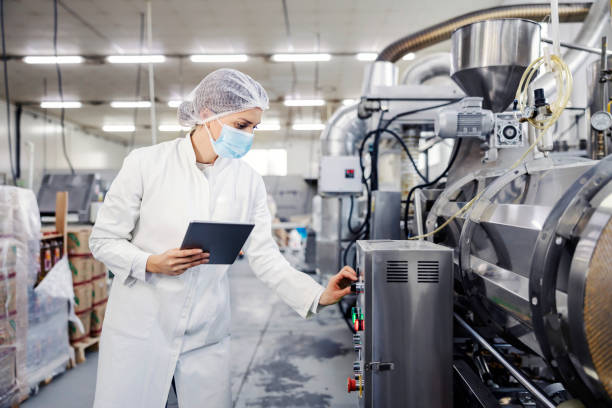
1. Kunststoffverarbeitung
Die Wasseraufnahmerate von ABS beträgt etwa 0,2–0,8 %. ABS allgemeiner Qualität sollte vor der Verarbeitung 2–4 Stunden lang in einem Ofen bei 80–85 °C oder 1–2 Stunden lang in einem Trocknungstrichter bei 80 °C gebrannt werden. Bei hitzebeständigem ABS mit PC-Komponenten sollte die Trocknungstemperatur entsprechend auf 100 °C erhöht werden und die spezifische Trocknungszeit kann durch Luftextrusion ermittelt werden.
Der Anteil recycelter Materialien darf 30 % nicht überschreiten, und ABS in Galvanikqualität kann keine recycelten Materialien verwenden.
2. Auswahl der Spritzgießmaschine
Es kann die Standard-Spritzgießmaschine von Ramada ausgewählt werden (Verhältnis Schneckenlänge zu Durchmesser 20:1, Kompressionsverhältnis größer als 2, Einspritzdruck größer als 1500 bar). Wenn das Farbmasterbatch verwendet wird oder das Erscheinungsbild des Produkts hoch ist, kann eine Schnecke mit kleinerem Durchmesser gewählt werden. Die Spannkraft wird nach 4700-6200t/m2 bestimmt, was von der Kunststoffsorte und den Produktanforderungen abhängt.
3. Formen- und Angussdesign
Die Formtemperatur kann auf 60-65°C eingestellt werden. Läuferdurchmesser 6–8 mm. Die Anschnittbreite beträgt etwa 3 mm, die Dicke entspricht der des Produkts und die Anschnittlänge sollte weniger als 1 mm betragen. Das Entlüftungsloch ist 4–6 mm breit und 0,025–0,05 mm dick.
4. Schmelztemperatur
Sie kann mit der Luftinjektionsmethode genau bestimmt werden. Unterschiedliche Qualitäten haben unterschiedliche Schmelztemperaturen. Die empfohlenen Einstellungen sind wie folgt:
Schlagfestigkeit: 220°C-260°C, vorzugsweise 250°C
Galvanikgrad: 250°C-275°C, vorzugsweise 270°C
Hitzebeständige Sorte: 240°C-280°C, vorzugsweise 265°C-270°C
Flammhemmender Grad: 200°C-240°C, vorzugsweise 220°C-230°C
Transparenter Grad: 230°C-260°C, vorzugsweise 245°C
Glasfaserverstärkter Typ: 230℃-270℃
Verwenden Sie für Produkte mit hohen Oberflächenanforderungen eine höhere Schmelztemperatur und Formtemperatur.
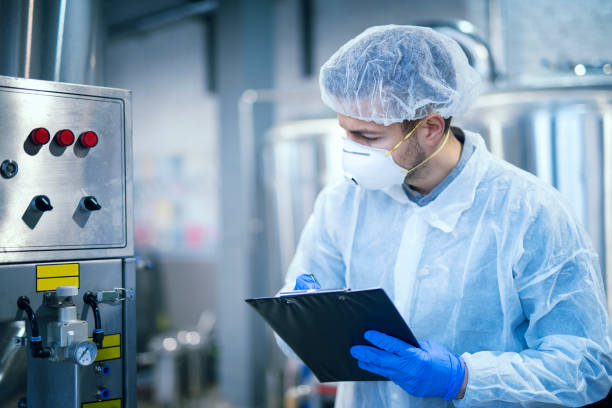
5. Einspritzgeschwindigkeit
Für die feuerbeständige Qualität wird eine langsame Geschwindigkeit und für die hitzebeständige Qualität eine hohe Geschwindigkeit verwendet. Wenn die Oberflächenanforderungen des Produkts hoch sind, sollte eine Hochgeschwindigkeits- und mehrstufige Spritzgeschwindigkeitsregelung beim Spritzgießen verwendet werden.
6. Gegendruck
Generell gilt: Je geringer der Gegendruck, desto besser. Der üblicherweise verwendete Gegendruck beträgt 5 bar, und das Färbematerial benötigt einen höheren Gegendruck, um eine gleichmäßige Farbmischung zu erreichen.
7. Verweilzeit
Bei einer Temperatur von 265°C sollte die Verweilzeit von ABS im Schmelzzylinder höchstens 5-6 Minuten betragen. Die Flammschutzzeit ist kürzer. Wenn es notwendig ist, die Maschine anzuhalten, sollte die eingestellte Temperatur zunächst auf 100 °C gesenkt werden, und dann sollte der geschmolzene Kunststoffzylinder mit Allzweck-ABS gereinigt werden. Die gereinigte Mischung sollte in kaltes Wasser gegeben werden, um eine weitere Zersetzung zu verhindern. Wenn Sie von anderen Kunststoffen auf ABS umsteigen müssen, müssen Sie den geschmolzenen Kunststoffzylinder zunächst mit PS, PMMA oder PE reinigen. Bei einigen ABS-Produkten treten keine Probleme auf, wenn sie direkt aus der Form gelöst werden. Sie verändern jedoch nach einiger Zeit ihre Farbe, was durch Überhitzung oder durch zu langes Verbleib des Kunststoffs im Schmelzzylinder verursacht werden kann.
8. Nachbearbeitung von Produkten
Im Allgemeinen ist bei ABS-Produkten keine Nachbearbeitung erforderlich. Lediglich Produkte in Galvanisierungsqualität müssen eingebrannt werden (70–80 °C, 2–4 Stunden), um die Oberflächenmarkierungen zu passivieren, und die Produkte, die galvanisiert werden müssen, können kein Trennmittel verwenden , und die Produkte müssen unmittelbar nach der Entnahme verpackt werden .
9. Dinge, die beim Formen besondere Aufmerksamkeit erfordern
Es gibt verschiedene ABS-Qualitäten (insbesondere die flammhemmende Qualität), deren Schmelze nach dem Plastifizieren eine starke Haftung an der Schraubenoberfläche aufweist und sich nach längerer Zeit zersetzt. Wenn die obige Situation auftritt, ist es notwendig, den Schneckenhomogenisierungsabschnitt und den Kompressor zum Abwischen herauszuziehen und die Schnecke regelmäßig mit PS usw. zu reinigen.
Zeitpunkt der Veröffentlichung: 09.08.2023