Kial ekranprintado produktas kolorajn rolantarojn? Se ni flankenmetas la miksaĵon de pluraj koloroj kaj pripensas nur unu koloron, eble estos pli simple diskuti la kaŭzojn de kolora rolantaro. Ĉi tiu artikolo dividas plurajn faktorojn kiuj influas kolordevion en ekranprintado. La enhavo estas por referenco de amikoj, kiuj aĉetas kaj provizas la pakaĵmaterialan sistemon de Youpin:
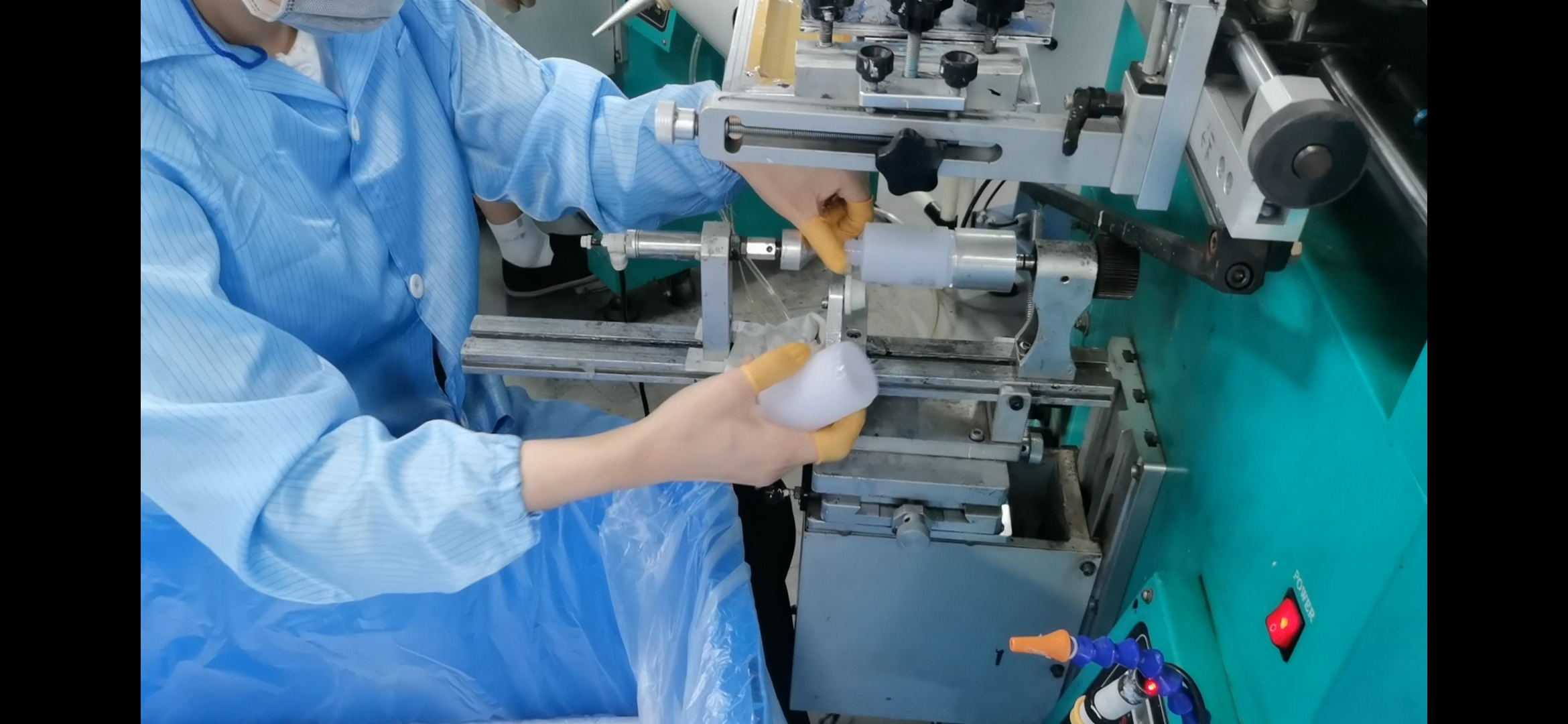
Kial ekranprintado produktas kolorajn rolantarojn? Se ni flankenmetas la miksaĵon de pluraj koloroj kaj pripensas nur unu koloron, eble estos pli simple diskuti la kaŭzojn de kolora rolantaro. Ĉi tiu artikolo dividas plurajn faktorojn kiuj influas kolordevion en ekranprintado. La enhavo estas por referenco de amikoj, kiuj aĉetas kaj provizas la pakaĵmaterialan sistemon de Youpin:
Listigitaj malsupre estas kelkaj el la plej oftaj faktoroj kiuj kaŭzas kolordevion en ekranprintado: inkpreparo, retselektado, retstreĉo, premo, sekigado, substratkarakterizaĵoj, observadkondiĉoj ktp.
01 Inkpreparo
Inka miksado Supozante, ke la pigmento de la uzata inko estas norma pigmento, la plej granda kaŭzo de kolordevio estas aldono de solviloj kiel inko miksanta oleon al la inko. En laborejo kun bona kolorkontrola ekipaĵo, inko povas esti miksita laŭ la kontrola ekipaĵo. Tamen, por plej multaj presaj kompanioj, estas neeble havi ĉi tiujn instalaĵojn. Ili nur dependas de la sperto de la majstraj laboristoj dum miksado de inko.
Ĝenerale, ink-ĝustiganta oleo estas aldonita por fari la inkon pli taŭga por presado. Tamen, post kiam alĝustigi oleon estas aldonita al la inko, la koncentriĝo de pigmentoj en la inko ŝanĝiĝos, kio kondukos al ŝanĝoj en la koloraj trajtoj de la inko dum presado. Krome, troa solvilo en la inko formos maldikan filmon de inko post sekiĝo, kiu reduktos la brilecon de la koloro.
Ekzistas ankaŭ la problemo de inko esti diluita antaŭ tinktado. Ekzemple, laboristoj en la inkbutiko faras juĝojn bazitajn sur sia formulo dum miksado aŭ diluado de inko. Ĉi tio kondukas al neevitebla kolordevio. Se la inko estas miksita antaŭ kelkaj tagoj, Se vi presas per bona inko, la kolora rolantaro kaŭzita de ĉi tiu situacio estos pli evidenta. Sekve, estas preskaŭ neeble tute eviti koloran roladon.
02 Maŝo-elekto
Se vi pensas, ke la maŝo-grandeco de la ekrano estas la sola faktoro, kiu influas inkan translokigon, vi renkontos multajn problemojn. Maŝo-diametro kaj sulkoj ankaŭ influas inktranslokigon. Ĝenerale, ju pli da inko alfiksita al la inktruoj de la ekrano, des pli da inko estos transdonita al la substrato dum la presa procezo.
Por anticipe taksi kiom da inko povas esti transdonita per ĉiu maŝo, multaj ekranprovizantoj disponigas la teorian inktransigan volumenon (TIV) de ĉiu maŝo. TIV estas parametro indikanta la grandecon de la inka transiga kvanto de la ekrano. Ĝi rilatas al la kvanto de inko translokigita en certa Kiom da inko estos transdonita de ĉiu maŝo sub specifaj presaj kondiĉoj. Ĝia unuo estas la volumeno de inko per unuo-areo.
Por certigi konsekvencajn tonojn en presado, ne sufiĉas konservi la maŝan nombron de la ekrano senŝanĝa, sed ankaŭ certigi, ke la diametro de la ekrano kaj ĝia ondeco restas konstantaj. Ŝanĝoj en iu parametro de la ekrano rezultigos ŝanĝojn en la dikeco de la inka filmo dum presado, rezultigante kolorŝanĝojn.
03 Reta streĉiĝo
Se la streĉiĝo de la reto estas tro malgranda, ĝi igos la filmon senŝeliĝi. Se estas tro da inko restanta en la maŝo, la presita materialo malpuriĝos.
Ĉi tiu problemo povas esti solvita pliigante la distancon inter la ekrano kaj la substrato. Tamen, pliigi la distancon inter la ekrano kaj la substrato postulas pliigi la premon, kio igos pli da inko translokiĝi al la substrato. ŝanĝi la densecon de la koloro. La plej bona maniero estas konservi la streĉiĝon de la streĉa reto uniforma, por certigi la konsistencon de la koloro.
04 Nivelo de premo
Taŭgaj premaj agordoj estas decidaj por konservi konsekvencan koloron, kaj certigi unuformajn premajn nivelojn dum la presa procezo estas kritika. Precipe en altvolumaj, ripetemaj presaj laboroj.
Kiam temas pri premo, la unua afero por konsideri estas la malmoleco de la racilo. La malmoleco de la racilo estas malgranda, kio estas bona por la kontaktorapideco, sed ĝi ne estas bona por fleksebla rezisto. Se la malmoleco estas tro alta, la frotado sur la ekrano ankaŭ estos granda dum presado, tiel influante la presan precizecon. La dua estas la angulo de la racilo kaj la rapido de la kravilo. La angulo de la inka tranĉilo havas gravan efikon sur la kvanto de inko-transigo. Ju pli malgranda estas la angulo de la inka tranĉilo, des pli granda estas la kvanto de inktransigo. Se la rapido de inka tranĉilo estas tro rapida, ĝi kaŭzos nesufiĉan inkplenigon kaj nekompletan impreson, tiel influante la kvaliton de la presaĵo.
Post kiam vi akiris la ĝustajn premajn agordojn por presa laboro kaj registris ilin precize, kondiĉe ke vi sekvas ĉi tiujn agordojn ĝuste dum la presa procezo, vi ricevos kontentigan presan produkton kun konsekvencaj koloroj.
05 seka
Kelkfoje, la koloro aspektas konsekvenca tuj post presado, sed la koloro ŝanĝiĝas post kiam la preta produkto estas trovita. Ĉi tio ofte estas kaŭzita de malĝustaj agordoj de la sekiga ekipaĵo. La plej ofta kaŭzo estas ke la sekigilo temperaturo estas tro alta, igante la inkkoloron sur la papero aŭ kartono ŝanĝiĝi.
06 Substrataj trajtoj
Unu afero, kiun ekranprintaj majstroj ofte preteratentas, estas la surfacaj trajtoj de la substrato. Papero, kartono, plasto ktp estas ĉiuj produktitaj en aroj, kaj altkvalitaj substratoj povas certigi stabilajn kaj konsekvencajn surfacajn proprietojn. Sed ĉi tio ne estas la kazo. Malgrandaj ŝanĝoj en la surfacaj propraĵoj de la substrato kaŭzos kolorajn deviojn en presado. Eĉ se la presa premo estas unuforma kaj eĉ ĉiu procezo estas funkciigita ĝuste, faktkonfliktoj en la surfacaj trajtoj de la substrato ankaŭ kaŭzos pli grandajn kolorŝanĝojn en printado. Koloro rolantaro.
Kiam la sama produkto estas presita sur malsamaj substratoj kun la sama presa ekipaĵo, la influo de la surfacaj propraĵoj de la substrato sur la koloro estas aparte evidenta. Klientoj povas postuli fenestroreklamojn esti presitaj sur plasto aŭ alia kartono. Kaj klientoj povas postuli konsekvencajn kolorojn por la sama peco.
En tiaj situacioj, la sola solvo estas fari precizajn kolormezurojn. Uzu spektrofotometron aŭ spektran densitometron por mezuri kolordensecon. Se estas kolorŝanĝo, la densitometro povas klare reflekti ĝin, kaj vi povas venki ĉi tiun kolorŝanĝon kontrolante aliajn procezojn.
07 Observkondiĉoj
Homaj okuloj estas tre sentemaj al subtilaj ŝanĝoj en koloro, kaj povas nur distingi kolorojn sub lumkondiĉoj. Pro tio, nepre kompari kolorojn sub la samaj lumkondiĉoj. Alie, ĝustigi la inkvolumon aŭ premon produktos pli da inko. Granda kolora rolantaro.
Entute, la ŝlosilo por konservi konsekvencan koloron kuŝas en la stabila kontrolo de ĉiu procezo por certigi stabilan agadon de la inko. La elekto de maŝgrandeco, streĉiĝo kaj premo de la streĉa ekrano, surfacaj trajtoj de la substrato kaj observkondiĉoj ĉiuj havas certan efikon sur kolordevio. Tamen, Precizaj fiksaj rekordoj kaj stabila kontrolo de ĉiu procezo estas la ŝlosiloj por certigi konsekvencajn ekranprintajn kolorojn.
Afiŝtempo: Jan-08-2024