¿Por qué la serigrafía produce matices de color? Si dejamos de lado la mezcla de varios colores y consideramos solo un color, puede ser más sencillo discutir las causas de la dominancia cromática. Este artículo comparte varios factores que afectan la desviación del color en la serigrafía. El contenido es de referencia para amigos que compran y suministran el sistema de material de embalaje Youpin:
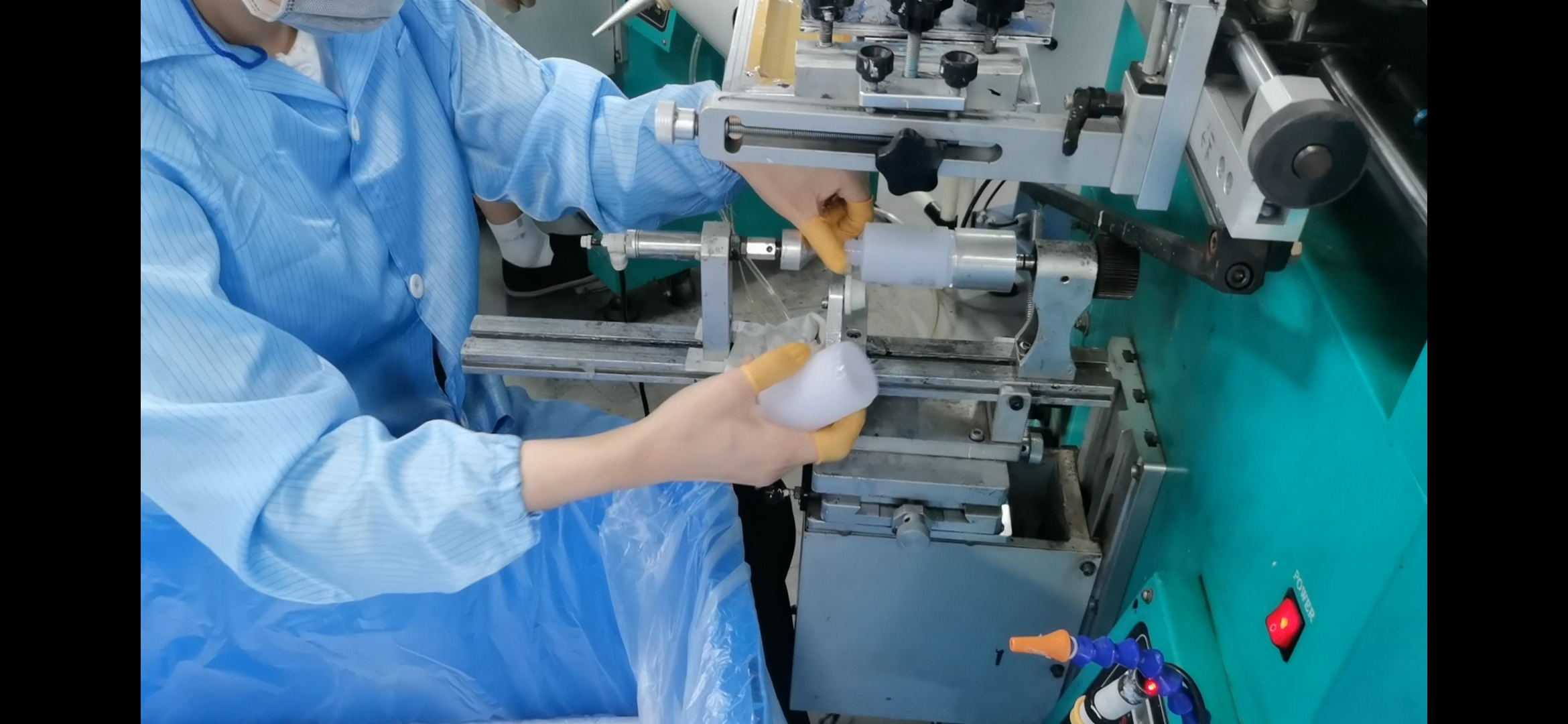
¿Por qué la serigrafía produce matices de color? Si dejamos de lado la mezcla de varios colores y consideramos solo un color, puede ser más sencillo discutir las causas de la dominancia cromática. Este artículo comparte varios factores que afectan la desviación del color en la serigrafía. El contenido es de referencia para amigos que compran y suministran el sistema de material de embalaje Youpin:
A continuación se enumeran algunos de los factores más comunes que causan desviación de color en la serigrafía: preparación de la tinta, selección de la malla, tensión de la malla, presión, secado, características del sustrato, condiciones de observación, etc.
01 preparación de tinta
Mezcla de tinta Suponiendo que el pigmento de la tinta utilizada es un pigmento estándar, la principal causa de desviación del color es la adición de disolventes como el aceite para mezclar tinta a la tinta. En un taller con un buen equipo de control del color, la tinta se puede mezclar según el equipo de control. Sin embargo, para la mayoría de las imprentas es imposible disponer de estas instalaciones. Sólo confían en la experiencia de los maestros trabajadores a la hora de mezclar tinta.
Generalmente, se agrega aceite de ajuste de tinta para que la tinta sea más adecuada para la impresión. Sin embargo, una vez que se agrega aceite de ajuste a la tinta, la concentración de pigmentos en la tinta cambiará, lo que provocará cambios en las características de color de la tinta durante la impresión. Además, el exceso de disolvente en la tinta formará una fina película de tinta después del secado, lo que reducirá el brillo del color.
También existe el problema de que la tinta se diluya antes de entintar. Por ejemplo, los trabajadores del taller de tinta hacen juicios basándose en su fórmula al mezclar o diluir tinta. Esto conduce a una inevitable desviación del color. Si la tinta se mezcló hace unos días, si imprime con buena tinta, la tonalidad de color provocada por esta situación será más evidente. Por lo tanto, es casi imposible evitar por completo el matiz de color.
02 Selección de malla
Si cree que el tamaño de la malla de la pantalla es el único factor que afecta la transferencia de tinta, encontrará muchos problemas. El diámetro de la malla y las arrugas también afectan la transferencia de tinta. Generalmente, cuanta más tinta se adhiera a los orificios de tinta de la pantalla, más tinta se transferirá al sustrato durante el proceso de impresión.
Para estimar de antemano cuánta tinta puede transferir cada malla, muchos proveedores de mallas proporcionan el volumen teórico de transferencia de tinta (TIV) de cada malla. TIV es un parámetro que indica el tamaño de la cantidad de transferencia de tinta de la pantalla. Se refiere a la cantidad de tinta transferida en una determinada cantidad de tinta que transferirá cada malla en condiciones de impresión específicas. Su unidad es el volumen de tinta por unidad de área.
Para garantizar tonos consistentes en la impresión, no basta con mantener inalterado el número de malla de la pantalla, sino también garantizar que el diámetro de la pantalla y su ondulación permanezcan constantes. Los cambios en cualquier parámetro de la pantalla darán como resultado cambios en el espesor de la película de tinta durante la impresión, lo que resultará en cambios de color.
03 tensión neta
Si la tensión de la red es demasiado pequeña, la película se despegará. Si queda demasiada tinta en la malla, el material impreso se ensuciará.
Este problema se puede solucionar aumentando la distancia entre la pantalla y el sustrato. Sin embargo, aumentar la distancia entre la pantalla y el sustrato requiere aumentar la presión, lo que hará que se transfiera más tinta al sustrato. para cambiar la densidad del color. La mejor manera es mantener uniforme la tensión de la red elástica para garantizar la consistencia del color.
04 Nivel de presión
Los ajustes de presión adecuados son cruciales para mantener un color uniforme y garantizar niveles de presión uniformes durante el proceso de impresión es fundamental. Especialmente en trabajos de impresión repetitivos y de gran volumen.
A la hora de presionar, lo primero que hay que tener en cuenta es la dureza de la espátula. La dureza de la escobilla de goma es pequeña, lo que es bueno para la velocidad de contacto, pero no es bueno para la resistencia a la flexión. Si la dureza es demasiado alta, la fricción en la pantalla también será grande durante la impresión, lo que afectará la precisión de la impresión. El segundo es el ángulo de la escobilla de goma y la velocidad de la escobilla de goma. El ángulo de la cuchilla de tinta tiene un impacto significativo en la cantidad de transferencia de tinta. Cuanto menor sea el ángulo de la cuchilla de tinta, mayor será la cantidad de tinta transferida. Si la velocidad de la cuchilla de tinta es demasiado rápida, provocará un llenado insuficiente de tinta y una impresión incompleta, lo que afectará la calidad de la impresión.
Una vez que haya obtenido los ajustes de presión correctos para un trabajo de impresión y los haya registrado con precisión, siempre que siga estos ajustes correctamente durante el proceso de impresión, obtendrá un producto de impresión satisfactorio con colores consistentes.
05 seco
A veces, el color parece uniforme justo después de la impresión, pero cambia una vez que se encuentra el producto terminado. Esto suele deberse a una configuración incorrecta del equipo de secado. La causa más común es que la temperatura de la secadora está demasiado alta, lo que hace que cambie el color de la tinta del papel o cartón.
06 Características del sustrato
Una cuestión que los maestros de la serigrafía suelen pasar por alto son las propiedades de la superficie del sustrato. El papel, el cartón, el plástico, etc. se producen en lotes y los sustratos de alta calidad pueden garantizar propiedades superficiales estables y consistentes. Pero este no es el caso. Pequeños cambios en las propiedades de la superficie del sustrato provocarán desviaciones de color en la impresión. Incluso si la presión de impresión es uniforme y cada proceso se opera correctamente, las inconsistencias en las propiedades de la superficie del sustrato también causarán mayores cambios de color en la impresión. Tono de color.
Cuando el mismo producto se imprime sobre diferentes sustratos con el mismo equipo de impresión, la influencia de las propiedades de la superficie del sustrato en el color es particularmente obvia. Los clientes pueden exigir que los anuncios en escaparates se impriman en plástico u otro cartón. Y los clientes pueden requerir colores consistentes para la misma pieza.
En situaciones como ésta, la única solución es realizar mediciones de color precisas. Utilice un espectrofotómetro o un densitómetro espectral para medir la densidad del color. Si hay un cambio de color, el densitómetro puede reflejarlo claramente y este cambio de color se puede superar controlando otros procesos.
07 Condiciones de observación
Los ojos humanos son muy sensibles a los cambios sutiles de color y sólo pueden distinguir los colores en condiciones de iluminación. Por esta razón, asegúrese de comparar colores bajo las mismas condiciones de iluminación. De lo contrario, ajustar el volumen o la presión de la tinta producirá más tinta. Gran matiz de color.
Con todo, la clave para mantener un color uniforme reside en el control estable de cada proceso para garantizar un rendimiento estable de la tinta. La selección del tamaño de la malla, la tensión y presión de la pantalla extensible, las características de la superficie del sustrato y las condiciones de observación tienen un cierto impacto en la desviación del color. Sin embargo, los registros de configuración precisos y el control estable de cada proceso son las claves para garantizar colores consistentes en la serigrafía.
Hora de publicación: 08-ene-2024