L'ABS, communément appelé acrylonitrile butadiène styrène, est formé par la copolymérisation de trois monomères acrylonitrile-butadiène-styrène. En raison des différentes proportions des trois monomères, il peut y avoir différentes propriétés et températures de fusion, performances de mobilité de l'ABS, mélange avec d'autres plastiques ou additifs, cela peut étendre l'utilisation et les performances de l'ABS.
La fluidité de l'ABS se situe entre PS et PC, et sa fluidité est liée à la température et à la pression d'injection, et l'influence de la pression d'injection est légèrement plus grande. Par conséquent, une pression d’injection plus élevée est souvent utilisée dans le moulage pour réduire la viscosité de la matière fondue et améliorer le remplissage du moule. performance.
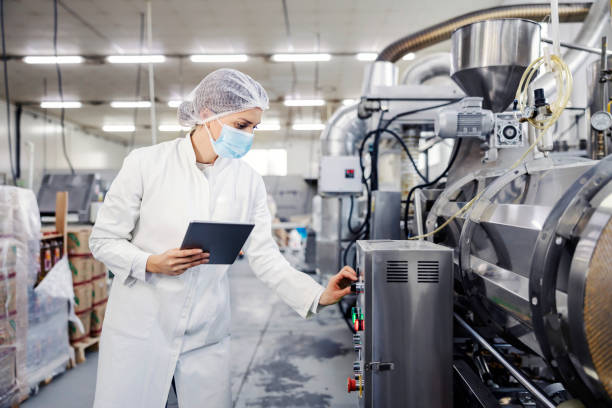
1. Transformation du plastique
Le taux d'absorption d'eau de l'ABS est d'environ 0,2 % à 0,8 %. Pour l'ABS de qualité générale, il doit être cuit dans un four à 80-85°C pendant 2 à 4 heures ou dans une trémie de séchage à 80°C pendant 1 à 2 heures avant d'être traité. Pour les composants ABS résistants à la chaleur contenant du PC, la température de séchage doit être augmentée de manière appropriée à 100 °C et le temps de séchage spécifique peut être déterminé par extrusion d'air.
La proportion de matériaux recyclés ne peut pas dépasser 30 % et l'ABS de qualité galvanoplastie ne peut pas utiliser de matériaux recyclés.
2. Sélection de la machine de moulage par injection
La machine de moulage par injection standard de Ramada peut être sélectionnée (rapport longueur/diamètre de vis 20:1, taux de compression supérieur à 2, pression d'injection supérieure à 1500 bars). Si le mélange maître de couleur est utilisé ou si l'aspect du produit est élevé, une vis d'un diamètre plus petit peut être sélectionnée. La force de serrage est déterminée selon 4 700-6 200 t/m2, qui dépend de la qualité du plastique et des exigences du produit.
3. Conception de moules et de portes
La température du moule peut être réglée entre 60 et 65°C. Diamètre du coureur 6-8 mm. La largeur du portail est d'environ 3 mm, l'épaisseur est la même que celle du produit et la longueur du portail doit être inférieure à 1 mm. Le trou d'aération mesure 4 à 6 mm de large et 0,025 à 0,05 mm d'épaisseur.
4. Température de fusion
Il peut être déterminé avec précision par la méthode d'injection d'air. Différentes qualités ont des températures de fusion différentes, les réglages recommandés sont les suivants :
Degré d'impact : 220°C-260°C, de préférence 250°C
Qualité de galvanoplastie : 250°C-275°C, de préférence 270°C
Qualité résistante à la chaleur : 240°C-280°C, de préférence 265°C-270°C
Qualité ignifuge : 200°C-240°C, de préférence 220°C-230°C
Qualité transparente : 230°C-260°C, de préférence 245°C
Qualité renforcée de fibre de verre : 230℃-270℃
Pour les produits ayant des exigences de surface élevées, utilisez une température de fusion et une température de moule plus élevées.
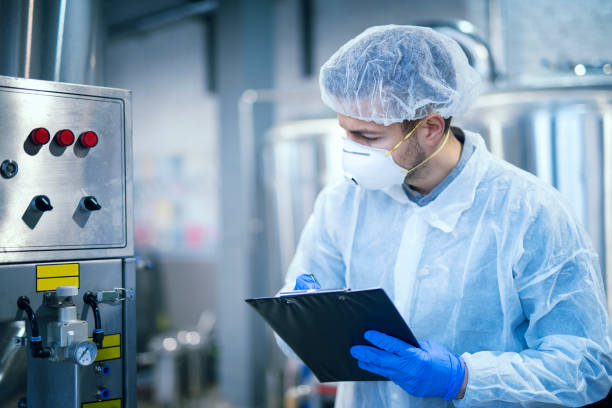
5. Vitesse d'injection
La vitesse lente est utilisée pour le grade résistant au feu, et la vitesse rapide est utilisée pour le grade résistant à la chaleur. Si les exigences de surface du produit sont élevées, un contrôle de la vitesse d'injection du moulage par injection à grande vitesse et à plusieurs étages doit être utilisé.
6. Contre-pression
En général, plus la contre-pression est faible, mieux c'est. La contre-pression couramment utilisée est de 5 bars et le matériau de teinture a besoin d'une contre-pression plus élevée pour uniformiser le mélange des couleurs.
7. Temps de séjour
À une température de 265°C, le temps de séjour de l'ABS dans le cylindre de fusion ne doit pas dépasser 5 à 6 minutes au maximum. Le temps d'ignifugation est plus court. S'il est nécessaire d'arrêter la machine, la température réglée doit d'abord être abaissée à 100°C, puis le cylindre en plastique fondu doit être nettoyé avec de l'ABS à usage général. Le mélange nettoyé doit être placé dans de l'eau froide pour éviter toute décomposition ultérieure. Si vous devez passer d'autres plastiques à l'ABS, vous devez d'abord nettoyer le cylindre en plastique fondu avec du PS, du PMMA ou du PE. Certains produits ABS n'ont aucun problème lorsqu'ils sont juste démoulés, mais ils changent de couleur après un certain temps, ce qui peut être dû à une surchauffe ou au fait que le plastique reste trop longtemps dans le cylindre de fusion.
8. Post-traitement des produits
Généralement, les produits ABS n'ont pas besoin de post-traitement, seuls les produits de qualité galvanoplastie doivent être cuits (70-80°C, 2-4 heures) pour passiver les marques de surface, et les produits qui doivent être galvanisés ne peuvent pas utiliser d'agent de démoulage. , et les produits doivent être emballés immédiatement après leur sortie .
9. Points nécessitant une attention particulière lors du moulage
Il existe plusieurs qualités d'ABS (en particulier la qualité ignifuge), dont la masse fondue a une forte adhérence à la surface de la vis après plastification et se décomposera après une longue période. Lorsque la situation ci-dessus se produit, il est nécessaire de retirer la section d'homogénéisation de la vis et le compresseur pour les essuyer, et de nettoyer régulièrement la vis avec du PS, etc.
Heure de publication : 09 août 2023