Pourquoi la sérigraphie produit-elle des dominantes de couleur ? Si l’on met de côté le mélange de plusieurs couleurs et ne considère qu’une seule couleur, il peut être plus simple de discuter des causes de la dominante chromatique. Cet article partage plusieurs facteurs qui affectent l’écart de couleur en sérigraphie. Le contenu est destiné à la référence des amis qui achètent et fournissent le système de matériel d'emballage Youpin :
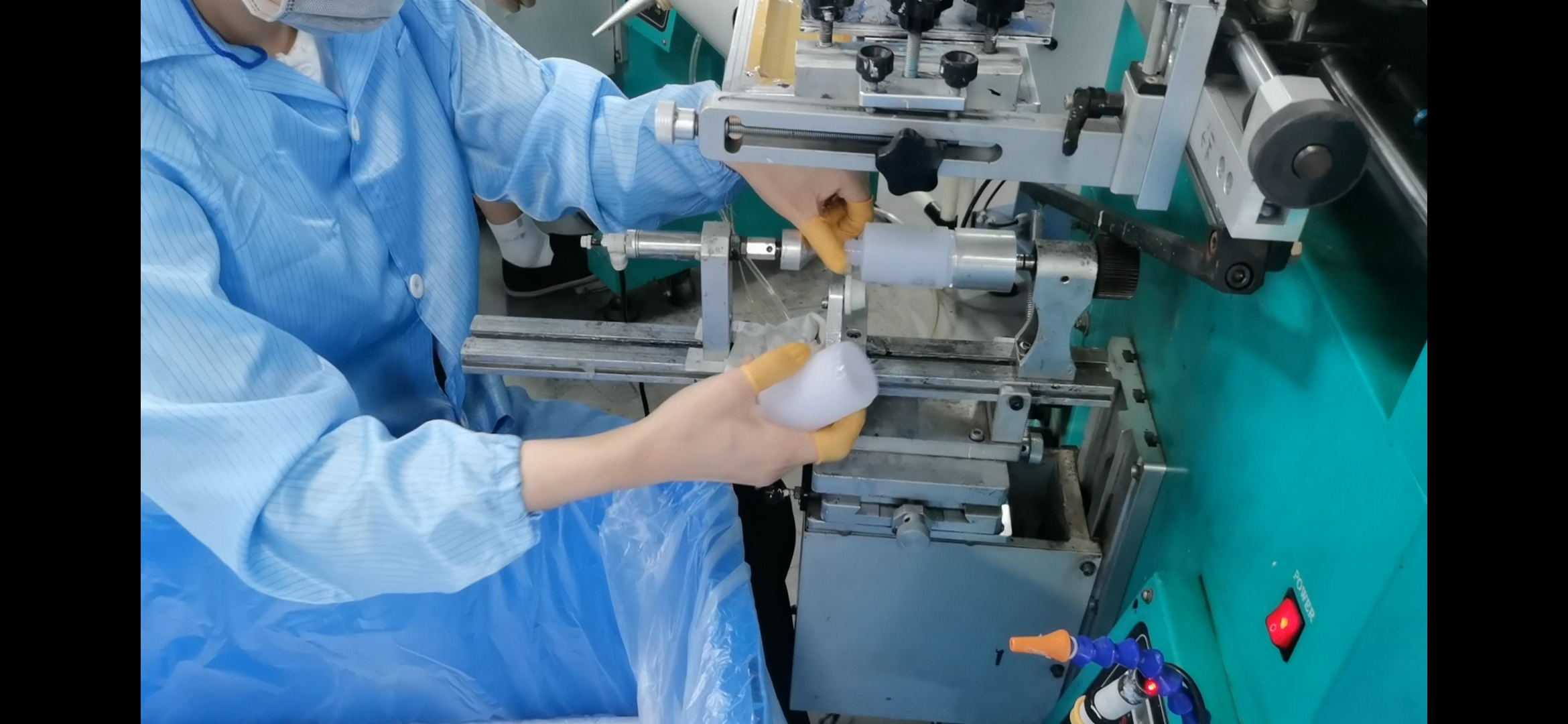
Pourquoi la sérigraphie produit-elle des dominantes de couleur ? Si l’on met de côté le mélange de plusieurs couleurs et ne considère qu’une seule couleur, il peut être plus simple de discuter des causes de la dominante chromatique. Cet article partage plusieurs facteurs qui affectent l’écart de couleur en sérigraphie. Le contenu est destiné à la référence des amis qui achètent et fournissent le système de matériel d'emballage Youpin :
Vous trouverez ci-dessous quelques-uns des facteurs les plus courants qui provoquent des écarts de couleur en sérigraphie : préparation de l'encre, sélection du maillage, tension du maillage, pression, séchage, caractéristiques du substrat, conditions d'observation, etc.
01 Préparation de l'encre
Mélange d'encres En supposant que le pigment de l'encre utilisée est un pigment standard, la principale cause de déviation de couleur est l'ajout de solvants tels que l'huile de mélange d'encre à l'encre. Dans un atelier doté d’un bon équipement de contrôle des couleurs, l’encre peut être mélangée en fonction de l’équipement de contrôle. Cependant, pour la plupart des imprimeries, il est impossible de disposer de ces installations. Ils s'appuient uniquement sur l'expérience des maîtres ouvriers pour mélanger l'encre.
Généralement, de l’huile d’ajustement de l’encre est ajoutée pour rendre l’encre plus adaptée à l’impression. Cependant, une fois l'huile d'ajustement ajoutée à l'encre, la concentration de pigments dans l'encre changera, ce qui entraînera des changements dans les caractéristiques de couleur de l'encre pendant l'impression. De plus, l’excès de solvant dans l’encre formera une fine pellicule d’encre après séchage, ce qui réduira la luminosité de la couleur.
Il y a aussi le problème de la dilution de l’encre avant l’encrage. Par exemple, les employés de l'atelier d'encre portent des jugements en fonction de leur formule lorsqu'ils mélangent ou diluent l'encre. Cela conduit à une déviation inévitable des couleurs. Si l'encre a été mélangée il y a quelques jours, si vous imprimez avec une bonne encre, la dominante de couleur provoquée par cette situation sera plus évidente. Par conséquent, il est presque impossible d’éviter complètement la dominante de couleur.
02 Sélection du maillage
Si vous pensez que la taille des mailles de l'écran est le seul facteur qui affecte le transfert d'encre, vous rencontrerez beaucoup de problèmes. Le diamètre du maillage et les rides affectent également le transfert d’encre. Généralement, plus il y a d’encre attachée aux trous d’encre de l’écran, plus d’encre sera transférée sur le substrat pendant le processus d’impression.
Afin d'estimer à l'avance la quantité d'encre pouvant être transférée par chaque maille, de nombreux fournisseurs de sérigraphies fournissent le volume théorique de transfert d'encre (TIV) de chaque maille. TIV est un paramètre indiquant la taille de la quantité de transfert d'encre de l'écran. Il fait référence à la quantité d'encre transférée dans une certaine quantité d'encre qui sera transférée par chaque maille dans des conditions d'impression spécifiques. Son unité est le volume d’encre par unité de surface.
Pour garantir des tons cohérents lors de l'impression, il ne suffit pas de maintenir inchangé le nombre de mailles de l'écran, mais également de garantir que le diamètre de l'écran et son ondulation restent constants. Les modifications de n'importe quel paramètre de l'écran entraîneront des modifications de l'épaisseur du film d'encre pendant l'impression, entraînant des changements de couleur.
03 Tension nette
Si la tension du filet est trop faible, le film se décollera. S’il reste trop d’encre dans le maillage, les imprimés se salissent.
Ce problème peut être résolu en augmentant la distance entre l'écran et le substrat. Cependant, augmenter la distance entre l’écran et le substrat nécessite d’augmenter la pression, ce qui entraînera un transfert d’encre plus important vers le substrat. pour changer la densité de la couleur. Le meilleur moyen est de maintenir la tension du filet extensible uniforme, de manière à garantir la cohérence de la couleur.
04 Niveau de pression
Des réglages de pression appropriés sont essentiels pour maintenir des couleurs cohérentes, et il est essentiel de garantir des niveaux de pression uniformes pendant le processus d'impression. Surtout dans les travaux d’impression répétitifs et à grand volume.
Concernant la pression, la première chose à considérer est la dureté de la raclette. La dureté de la raclette est faible, ce qui est bon pour le taux de contact, mais ce n'est pas bon pour la résistance à la flexion. Si la dureté est trop élevée, la friction sur l'écran sera également importante lors de l'impression, affectant ainsi la précision de l'impression. La seconde est l’angle de la raclette et la vitesse de la raclette. L’angle du couteau à encre a un impact significatif sur la quantité de transfert d’encre. Plus l’angle du couteau à encre est petit, plus la quantité de transfert d’encre est importante. Si la vitesse du couteau à encre est trop rapide, cela entraînera un remplissage d'encre insuffisant et une impression incomplète, affectant ainsi la qualité de l'impression.
Une fois que vous avez obtenu les paramètres de pression corrects pour un travail d'impression et que vous les avez enregistrés avec précision, tant que vous suivez correctement ces paramètres pendant le processus d'impression, vous obtiendrez un produit d'impression satisfaisant avec des couleurs cohérentes.
05 sec
Parfois, la couleur semble constante juste après l’impression, mais elle change une fois le produit fini trouvé. Ceci est souvent dû à des réglages incorrects de l'équipement de séchage. La cause la plus courante est que la température du séchoir est trop élevée, ce qui entraîne une modification de la couleur de l'encre sur le papier ou le carton.
06 Caractéristiques du substrat
Un problème que les maîtres de la sérigraphie négligent souvent concerne les propriétés de surface du substrat. Le papier, le carton, le plastique, etc. sont tous produits par lots, et des substrats de haute qualité peuvent garantir des propriétés de surface stables et constantes. Mais ce n’est pas le cas. De petits changements dans les propriétés de surface du substrat entraîneront des écarts de couleur lors de l’impression. Même si la pression d'impression est uniforme et même si chaque processus est exécuté correctement, les incohérences dans les propriétés de surface du substrat entraîneront également des changements de couleur plus importants lors de l'impression. dominante de couleur.
Lorsque le même produit est imprimé sur différents substrats avec le même équipement d’impression, l’influence des propriétés de surface du substrat sur la couleur est particulièrement évidente. Les clients peuvent exiger que les publicités en vitrine soient imprimées sur du plastique ou un autre carton. Et les clients peuvent exiger des couleurs cohérentes pour la même pièce.
Dans de telles situations, la seule solution consiste à effectuer des mesures de couleur précises. Utilisez un spectrophotomètre ou un densitomètre spectral pour mesurer la densité des couleurs. S'il y a un changement de couleur, le densitomètre peut le refléter clairement et vous pouvez surmonter ce changement de couleur en contrôlant d'autres processus.
07 Conditions d'observation
Les yeux humains sont très sensibles aux changements subtils de couleur et ne peuvent distinguer les couleurs que dans des conditions d’éclairage. Pour cette raison, assurez-vous de comparer les couleurs dans les mêmes conditions d’éclairage. Sinon, l’ajustement du volume ou de la pression de l’encre produira plus d’encre. Grande dominante de couleur.
Dans l’ensemble, la clé du maintien d’une couleur cohérente réside dans le contrôle stable de chaque processus afin de garantir des performances stables de l’encre. Le choix de la taille des mailles, la tension et la pression du tamis étirable, les caractéristiques de surface du substrat et les conditions d'observation ont tous un certain impact sur l'écart de couleur. Cependant, des enregistrements de réglages précis et un contrôle stable de chaque processus sont les clés pour garantir des couleurs de sérigraphie cohérentes.
Heure de publication : 08 janvier 2024