O ABS, comunmente coñecido como acrilonitrilo butadieno estireno, fórmase pola copolimerización de tres monómeros de acrilonitrilo-butadieno-estireno. Debido ás diferentes proporcións dos tres monómeros, pode haber diferentes propiedades e temperatura de fusión, o rendemento de mobilidade do ABS, a mestura con outros plásticos ou aditivos, pode ampliar o uso e o rendemento do ABS.
A fluidez do ABS está entre PS e PC, e a súa fluidez está relacionada coa temperatura e presión de inxección, e a influencia da presión de inxección é lixeiramente maior. Polo tanto, a presión de inxección máis alta úsase a miúdo no moldeado para reducir a viscosidade do fundido e mellorar o recheo do molde. rendemento.
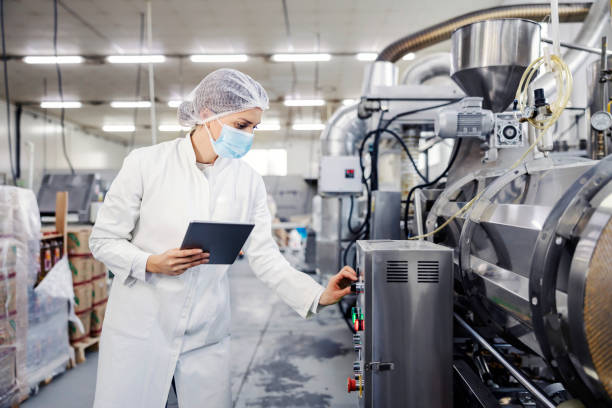
1. Procesado de plásticos
A taxa de absorción de auga do ABS é de aproximadamente 0,2%-0,8%. Para o ABS de grao xeral, debe cocerse nun forno a 80-85 °C durante 2-4 horas ou nunha tolva de secado a 80 °C durante 1-2 horas antes de procesar. Para os compoñentes de PC que conteñen ABS resistente á calor, a temperatura de secado debe aumentarse adecuadamente ata 100 °C e o tempo de secado específico pódese determinar mediante extrusión de aire.
A proporción de materiais reciclados non pode exceder o 30%, e o ABS de galvanoplastia non pode usar materiais reciclados.
2. Selección da máquina de moldaxe por inxección
Pódese seleccionar a máquina de moldaxe por inxección estándar de Ramada (relación lonxitude-diámetro do parafuso 20:1, relación de compresión superior a 2, presión de inxección superior a 1500 bar). Se se usa o masterbatch de cor ou o aspecto do produto é alto, pódese seleccionar un parafuso cun diámetro menor. A forza de suxeición determínase segundo 4700-6200t/m2, que depende da calidade do plástico e dos requisitos do produto.
3. Deseño de moldes e portas
A temperatura do molde pódese configurar entre 60 e 65 °C. Diámetro de guía 6-8 mm. O ancho da porta é de aproximadamente 3 mm, o grosor é o mesmo que o do produto e a lonxitude da porta debe ser inferior a 1 mm. O orificio de ventilación ten 4-6 mm de ancho e 0,025-0,05 mm de espesor.
4. Temperatura de fusión
Pódese determinar con precisión polo método de inxección de aire. Os diferentes graos teñen unha temperatura de fusión diferente, os axustes recomendados son os seguintes:
Grao de impacto: 220°C-260°C, preferentemente 250°C
Grao de galvanoplastia: 250°C-275°C, preferentemente 270°C
Grao de resistencia á calor: 240°C-280°C, preferentemente 265°C-270°C
Grao retardador de chama: 200°C-240°C, preferentemente 220°C-230°C
Grao transparente: 230°C-260°C, preferentemente 245°C
Grao reforzado con fibra de vidro: 230 ℃-270 ℃
Para produtos con altos requisitos de superficie, use unha temperatura de fusión e unha temperatura do molde máis altas.
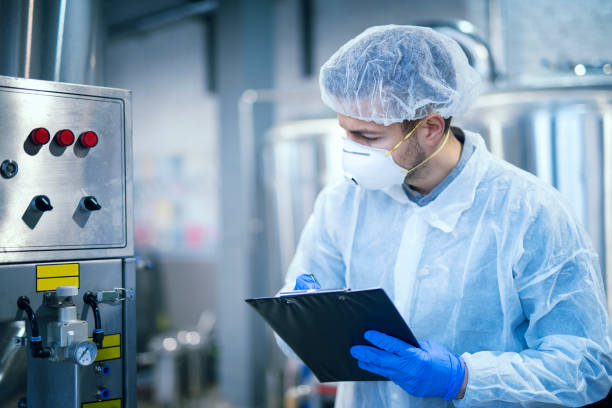
5. Velocidade de inxección
A velocidade lenta úsase para o grao resistente ao lume e a velocidade rápida para o grao resistente á calor. Se os requisitos de superficie do produto son altos, débese utilizar o control da velocidade de inxección de moldeo por inxección de alta velocidade e de varias etapas.
6. Contrapresión
En xeral, canto menor sexa a contrapresión, mellor. A contrapresión que se usa habitualmente é de 5 bar, e o material de tinguido necesita unha contrapresión máis alta para que a mestura de cores sexa uniforme.
7. Tempo de residencia
A unha temperatura de 265 °C, o tempo de permanencia do ABS no cilindro de fusión non debe exceder de 5-6 minutos como máximo. O tempo de retardo de chama é máis curto. Se é necesario parar a máquina, primeiro debe baixar a temperatura establecida a 100 °C e, a continuación, limpar o cilindro de plástico fundido con ABS de uso xeral. A mestura limpa debe colocarse en auga fría para evitar unha maior descomposición. Se precisa cambiar doutros plásticos a ABS, primeiro debe limpar o cilindro de plástico fundido con PS, PMMA ou PE. Algúns produtos ABS non teñen ningún problema cando se acaban de liberar do molde, pero cambiarán de cor despois dun período de tempo, o que pode ser causado por un sobreenriquecido ou o plástico que permanece no cilindro de fusión durante moito tempo.
8. Post-elaboración dos produtos
Xeralmente, os produtos ABS non precisan posprocesamento, só os produtos de calidade galvanoplastia deben ser cocidos (70-80 °C, 2-4 horas) para pasivar as marcas de superficie, e os produtos que deben ser galvanizados non poden usar un axente de liberación. , e os produtos deben ser embalados inmediatamente despois da súa retirada .
9. Asuntos que precisan especial atención ao moldear
Hai varios graos de ABS (especialmente o grao retardador de chama), cuxa fusión ten unha forte adhesión á superficie do parafuso despois da plastificación e descompoñerase despois de moito tempo. Cando se produce a situación anterior, é necesario sacar a sección de homoxeneización do parafuso e o compresor para limpar e limpar regularmente o parafuso con PS, etc.
Hora da publicación: 09-ago-2023