Por que a serigrafía produce tons de cores? Se deixamos de lado a mestura de varias cores e consideramos só unha cor, pode ser máis sinxelo discutir as causas do elenco de cores. Este artigo comparte varios factores que afectan á desviación da cor na serigrafía. O contido é para referencia dos amigos que compran e fornecen o sistema de material de embalaxe Youpin:
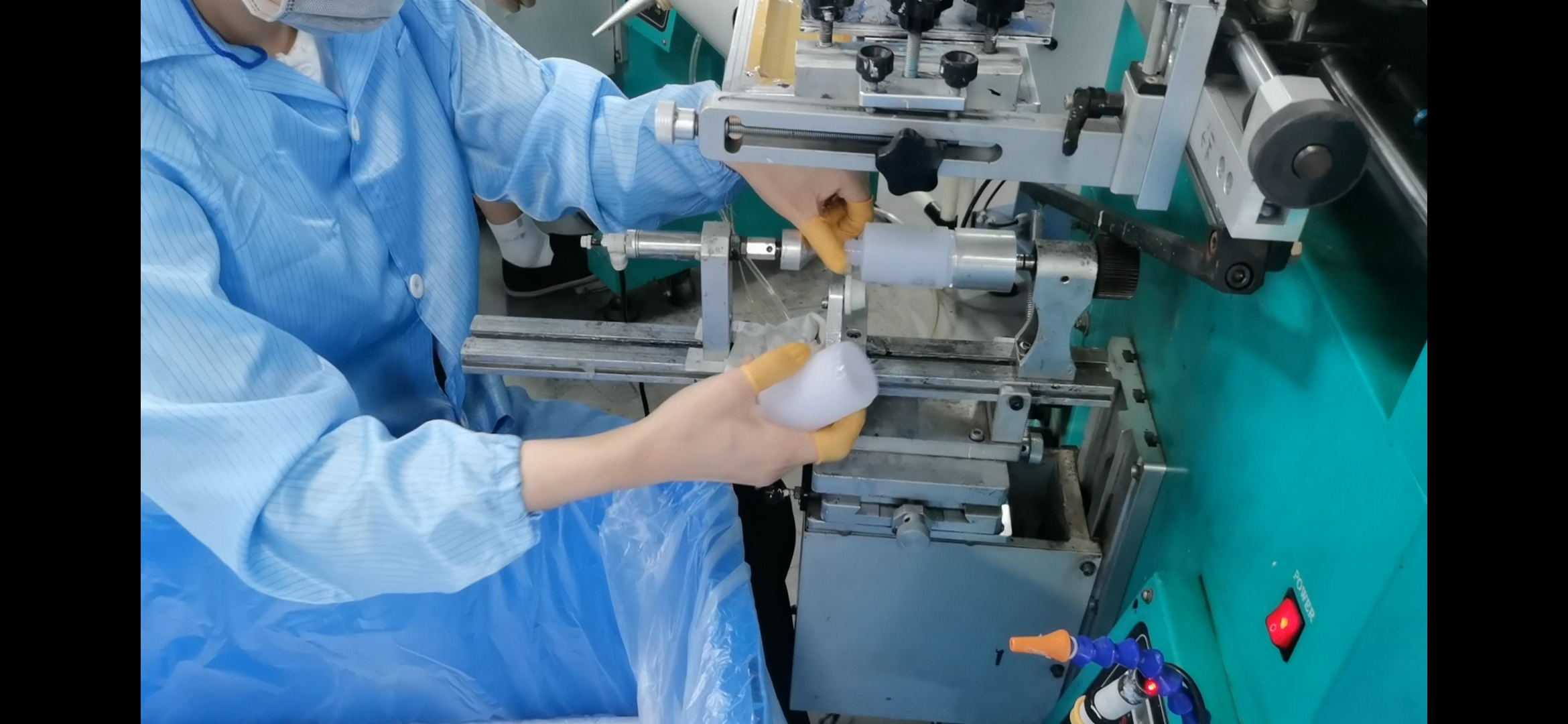
Por que a serigrafía produce tons de cores? Se deixamos de lado a mestura de varias cores e consideramos só unha cor, pode ser máis sinxelo discutir as causas do elenco de cores. Este artigo comparte varios factores que afectan á desviación da cor na serigrafía. O contido é para referencia dos amigos que compran e fornecen o sistema de material de embalaxe Youpin:
A continuación móstranse algúns dos factores máis comúns que provocan a desviación da cor na serigrafía: preparación da tinta, selección da malla, tensión da malla, presión, secado, características do substrato, condicións de observación, etc.
01 Preparación da tinta
Mestura de tinta Asumindo que o pigmento da tinta utilizada é un pigmento estándar, a principal causa da desviación da cor é a adición de disolventes como o aceite de mestura de tinta á tinta. Nun taller cun bo equipo de control de cor, a tinta pódese mesturar segundo o equipo de control. Non obstante, para a maioría das empresas de impresión, é imposible ter estas instalacións. Só confían na experiencia dos mestres obreiros á hora de mesturar tinta.
Xeralmente, engádese aceite para axustar a tinta para que a tinta sexa máis adecuada para a impresión. Non obstante, unha vez que se engade aceite de axuste á tinta, a concentración de pigmentos na tinta cambiará, o que provocará cambios nas características de cor da tinta durante a impresión. Ademais, o exceso de disolvente na tinta formará unha fina película de tinta despois do secado, o que reducirá o brillo da cor.
Tamén existe o problema de diluír a tinta antes de entintar. Por exemplo, os traballadores da tenda de tinta fan xuízos en función da súa fórmula ao mesturar ou diluír a tinta. Isto leva á inevitable desviación da cor. Se a tinta se mestura hai uns días, se imprime con boa tinta, a cor causada por esta situación será máis evidente. Polo tanto, é case imposible evitar por completo a cor.
02 Selección de malla
Se pensas que o tamaño da malla da pantalla é o único factor que afecta a transferencia de tinta, atoparás moitos problemas. O diámetro da malla e as engurras tamén afectan a transferencia de tinta. Xeralmente, canto máis tinta estea unida aos orificios de tinta da pantalla, máis tinta se transferirá ao substrato durante o proceso de impresión.
Para estimar con antelación a cantidade de tinta que pode transferir cada malla, moitos provedores de pantallas proporcionan o volume teórico de transferencia de tinta (TIV) de cada malla. TIV é un parámetro que indica o tamaño da cantidade de transferencia de tinta da pantalla. Refírese á cantidade de tinta transferida nun determinado Canto de tinta transferirá cada malla en condicións de impresión específicas. A súa unidade é o volume de tinta por unidade de superficie.
Para garantir tons consistentes na impresión, non abonda con manter o número de malla da pantalla sen cambios, senón tamén para garantir que o diámetro da pantalla e a súa ondulación permanezan constantes. Os cambios en calquera parámetro da pantalla provocarán cambios no grosor da película de tinta durante a impresión, o que provocará cambios de cor.
03 Tensión neta
Se a tensión da rede é demasiado pequena, fará que a película se desprenda. Se queda demasiada tinta na malla, o material impreso ensuciarase.
Este problema pódese resolver aumentando a distancia entre a pantalla e o substrato. Non obstante, aumentar a distancia entre a pantalla e o substrato require aumentar a presión, o que fará que se transfira máis tinta ao substrato. para cambiar a densidade da cor. A mellor forma é manter a tensión da rede elástica uniforme, para garantir a consistencia da cor.
04 Nivel de presión
As configuracións de presión adecuadas son fundamentais para manter unha cor consistente, e é fundamental garantir niveis de presión uniformes durante o proceso de impresión. Especialmente nos traballos de impresión repetitivos de gran volume.
Cando se trata de presión, o primeiro que hai que ter en conta é a dureza da escobilla. A dureza da escobilla é pequena, o que é bo para a taxa de contacto, pero non é bo para a resistencia á flexión. Se a dureza é demasiado alta, a fricción na pantalla tamén será grande durante a impresión, afectando así a precisión da impresión. O segundo é o ángulo da raspadora e a súa velocidade. O ángulo do coitelo de tinta ten un impacto significativo na cantidade de transferencia de tinta. Canto menor sexa o ángulo do coitelo de tinta, maior será a cantidade de transferencia de tinta. Se a velocidade da coitela de tinta é demasiado rápida, provocará un recheo de tinta insuficiente e unha impresión incompleta, afectando así a calidade da impresión.
Unha vez que obteña os axustes de presión correctos para un traballo de impresión e os gravou con precisión, sempre que siga estes axustes correctamente durante o proceso de impresión, obterá un produto de impresión satisfactorio con cores consistentes.
05 seco
Ás veces, a cor parece consistente xusto despois da impresión, pero a cor cambia despois de atopar o produto acabado. Isto adoita ser causado por unha configuración incorrecta do equipo de secado. A causa máis común é que a temperatura do secador está demasiado alta, o que fai que cambie a cor da tinta do papel ou cartón.
06 Características do substrato
Un problema que os mestres de serigrafía adoitan pasar por alto son as propiedades da superficie do substrato. O papel, o cartón, o plástico, etc. prodúcense en lotes, e os substratos de alta calidade poden garantir propiedades de superficie estables e consistentes. Pero este non é o caso. Pequenos cambios nas propiedades da superficie do substrato provocarán desviacións de cor na impresión. Aínda que a presión de impresión sexa uniforme e mesmo cada proceso funcione correctamente, as inconsistencias nas propiedades da superficie do substrato tamén provocarán cambios de cor máis grandes na impresión. Cast de cor.
Cando o mesmo produto se imprime en diferentes substratos co mesmo equipo de impresión, a influencia das propiedades da superficie do substrato na cor é particularmente evidente. Os clientes poden requirir que os anuncios das fiestras sexan impresos en plástico ou outro cartón. E os clientes poden requirir cores consistentes para a mesma peza.
En situacións como esta, a única solución é facer medicións de cor precisas. Use un espectrofotómetro ou un densitómetro espectral para medir a densidade da cor. Se hai un cambio de cor, o densitómetro pode reflectilo claramente, e podes superar este cambio de cor controlando outros procesos.
07 Condicións de observación
Os ollos humanos son moi sensibles a cambios sutís de cor e só poden distinguir cores en condicións de iluminación. Por iso, asegúrate de comparar as cores nas mesmas condicións de iluminación. En caso contrario, axustar o volume ou a presión da tinta producirá máis tinta. Gran elenco de cores.
En definitiva, a clave para manter unha cor consistente reside no control estable de cada proceso para garantir un rendemento estable da tinta. A selección do tamaño da malla, a tensión e a presión da pantalla de estiramento, as características da superficie do substrato e as condicións de observación teñen un certo impacto na desviación da cor. Non obstante, os rexistros de configuración precisos e o control estable de cada proceso son as claves para garantir cores de serigrafía consistentes.
Hora de publicación: Xaneiro-08-2024