स्क्रीन प्रिंटिंग रंगीन कास्ट क्यों उत्पन्न करती है? यदि हम कई रंगों के मिश्रण को अलग रख दें और केवल एक रंग पर विचार करें, तो रंग ढलने के कारणों पर चर्चा करना आसान हो सकता है। यह आलेख कई कारकों को साझा करता है जो स्क्रीन प्रिंटिंग में रंग विचलन को प्रभावित करते हैं। यह सामग्री उन मित्रों के संदर्भ के लिए है जो यूपिन पैकेजिंग सामग्री प्रणाली खरीदते और आपूर्ति करते हैं:
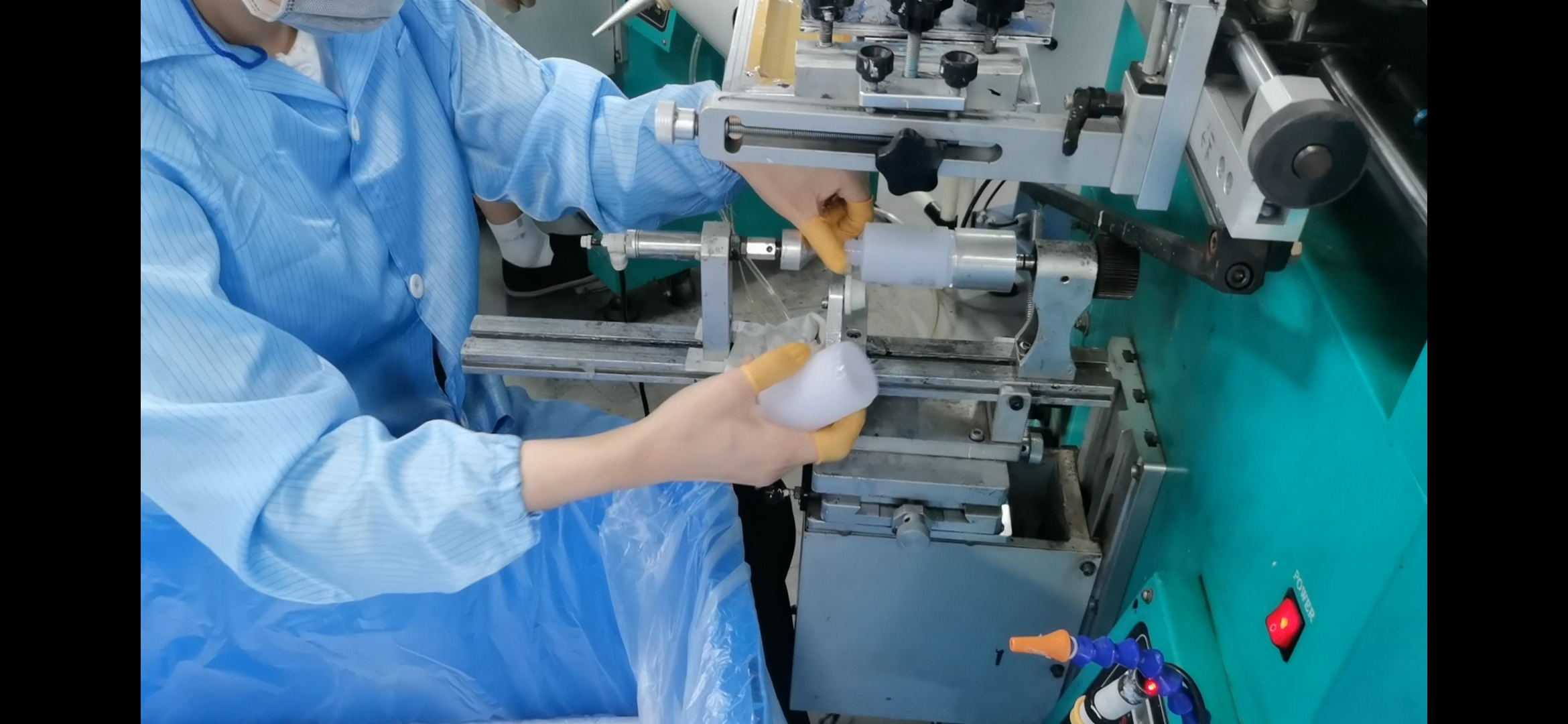
स्क्रीन प्रिंटिंग रंगीन कास्ट क्यों उत्पन्न करती है? यदि हम कई रंगों के मिश्रण को अलग रख दें और केवल एक रंग पर विचार करें, तो रंग ढलने के कारणों पर चर्चा करना आसान हो सकता है। यह आलेख कई कारकों को साझा करता है जो स्क्रीन प्रिंटिंग में रंग विचलन को प्रभावित करते हैं। यह सामग्री उन मित्रों के संदर्भ के लिए है जो यूपिन पैकेजिंग सामग्री प्रणाली खरीदते और आपूर्ति करते हैं:
नीचे सूचीबद्ध कुछ सबसे सामान्य कारक हैं जो स्क्रीन प्रिंटिंग में रंग विचलन का कारण बनते हैं: स्याही की तैयारी, जाल चयन, जाल तनाव, दबाव, सुखाने, सब्सट्रेट विशेषताएँ, अवलोकन की स्थिति, आदि।
01 स्याही की तैयारी
स्याही सम्मिश्रण यह मानते हुए कि उपयोग की गई स्याही का रंग एक मानक रंगद्रव्य है, रंग विचलन का सबसे बड़ा कारण स्याही में तेल मिश्रण करने वाले स्याही जैसे सॉल्वैंट्स का मिश्रण है। अच्छे रंग नियंत्रण उपकरण वाली कार्यशाला में स्याही को नियंत्रण उपकरण के अनुसार मिलाया जा सकता है। हालाँकि, अधिकांश मुद्रण कंपनियों के लिए ये सुविधाएँ प्राप्त करना असंभव है। स्याही मिलाते समय वे केवल मास्टर श्रमिकों के अनुभव पर भरोसा करते हैं।
आम तौर पर, स्याही को मुद्रण के लिए अधिक उपयुक्त बनाने के लिए स्याही-समायोजन तेल जोड़ा जाता है। हालाँकि, एक बार जब समायोजन तेल को स्याही में जोड़ दिया जाता है, तो स्याही में रंगद्रव्य की सांद्रता बदल जाएगी, जिससे मुद्रण के दौरान स्याही की रंग विशेषताओं में बदलाव आएगा। इसके अलावा, स्याही में अतिरिक्त विलायक सूखने के बाद स्याही की एक पतली फिल्म बनाएगा, जिससे रंग की चमक कम हो जाएगी।
स्याही लगाने से पहले स्याही के पतला होने की भी समस्या है। उदाहरण के लिए, स्याही की दुकान में कर्मचारी स्याही को मिलाते या पतला करते समय अपने फॉर्मूले के आधार पर निर्णय लेते हैं। इससे अपरिहार्य रंग विचलन होता है। यदि स्याही कुछ दिन पहले मिश्रित की गई है, यदि आप अच्छी स्याही से प्रिंट करते हैं, तो इस स्थिति के कारण होने वाला रंग अधिक स्पष्ट होगा। इसलिए, कलर कास्ट से पूरी तरह बचना लगभग असंभव है।
02 मेष चयन
यदि आप सोचते हैं कि स्क्रीन का जाल आकार ही एकमात्र कारक है जो स्याही हस्तांतरण को प्रभावित करता है, तो आपको बहुत परेशानी का सामना करना पड़ेगा। जाल का व्यास और झुर्रियाँ भी स्याही स्थानांतरण को प्रभावित करती हैं। आम तौर पर, जितनी अधिक स्याही स्क्रीन के स्याही छिद्रों से जुड़ी होगी, उतनी ही अधिक स्याही मुद्रण प्रक्रिया के दौरान सब्सट्रेट में स्थानांतरित की जाएगी।
पहले से अनुमान लगाने के लिए कि प्रत्येक जाल द्वारा कितनी स्याही स्थानांतरित की जा सकती है, कई स्क्रीन आपूर्तिकर्ता प्रत्येक जाल की सैद्धांतिक स्याही हस्तांतरण मात्रा (टीआईवी) प्रदान करते हैं। TIV एक पैरामीटर है जो स्क्रीन की स्याही हस्तांतरण मात्रा के आकार को दर्शाता है। यह एक निश्चित में हस्तांतरित स्याही की मात्रा को संदर्भित करता है कि विशिष्ट मुद्रण स्थितियों के तहत प्रत्येक जाल द्वारा कितनी स्याही स्थानांतरित की जाएगी। इसकी इकाई प्रति इकाई क्षेत्र स्याही की मात्रा है।
मुद्रण में लगातार टोन सुनिश्चित करने के लिए, स्क्रीन की जाली संख्या को अपरिवर्तित रखना ही पर्याप्त नहीं है, बल्कि यह भी सुनिश्चित करना है कि स्क्रीन का व्यास और उसकी लहरदारता स्थिर रहे। स्क्रीन के किसी भी पैरामीटर में परिवर्तन के परिणामस्वरूप मुद्रण के दौरान स्याही फिल्म की मोटाई में परिवर्तन होगा, जिसके परिणामस्वरूप रंग बदल जाएगा।
03 नेट तनाव
यदि नेट का तनाव बहुत कम है, तो इससे फिल्म छिल जाएगी। यदि जाली में बहुत अधिक स्याही रह जाएगी, तो मुद्रित पदार्थ गंदा हो जाएगा।
स्क्रीन और सब्सट्रेट के बीच की दूरी बढ़ाकर इस समस्या को हल किया जा सकता है। हालाँकि, स्क्रीन और सब्सट्रेट के बीच की दूरी बढ़ाने के लिए दबाव बढ़ाने की आवश्यकता होती है, जिससे अधिक स्याही सब्सट्रेट में स्थानांतरित हो जाएगी। रंग का घनत्व बदलने के लिए. सबसे अच्छा तरीका यह है कि स्ट्रेच नेट के तनाव को एक समान रखा जाए, ताकि रंग की स्थिरता सुनिश्चित हो सके।
04 दबाव स्तर
लगातार रंग बनाए रखने के लिए उचित दबाव सेटिंग्स महत्वपूर्ण हैं, और मुद्रण प्रक्रिया के दौरान एक समान दबाव स्तर सुनिश्चित करना महत्वपूर्ण है। विशेष रूप से उच्च-मात्रा, दोहराव वाले मुद्रण कार्यों में।
जब दबाव की बात आती है, तो सबसे पहले विचार करने वाली बात निचोड़ की कठोरता है। स्क्वीजी की कठोरता छोटी है, जो संपर्क दर के लिए अच्छा है, लेकिन यह झुकने के प्रतिरोध के लिए अच्छा नहीं है। यदि कठोरता बहुत अधिक है, तो मुद्रण के दौरान स्क्रीन पर घर्षण भी बड़ा होगा, जिससे मुद्रण सटीकता प्रभावित होगी। दूसरा स्क्वीजी का कोण और स्क्वीजी गति है। स्याही चाकू के कोण का स्याही हस्तांतरण की मात्रा पर महत्वपूर्ण प्रभाव पड़ता है। स्याही चाकू का कोण जितना छोटा होगा, स्याही स्थानांतरण की मात्रा उतनी ही अधिक होगी। यदि स्याही चाकू की गति बहुत तेज है, तो यह अपर्याप्त स्याही भरने और अधूरी छाप का कारण बनेगी, जिससे प्रिंट की गुणवत्ता प्रभावित होगी।
एक बार जब आप प्रिंट कार्य के लिए सही दबाव सेटिंग्स प्राप्त कर लेते हैं और उन्हें सटीक रूप से रिकॉर्ड कर लेते हैं, जब तक आप प्रिंटिंग प्रक्रिया के दौरान इन सेटिंग्स का सही ढंग से पालन करते हैं, आपको लगातार रंगों के साथ एक संतोषजनक प्रिंट उत्पाद मिलेगा।
05 सूखा
कभी-कभी, छपाई के तुरंत बाद रंग एक जैसा दिखता है, लेकिन तैयार उत्पाद मिलने के बाद रंग बदल जाता है। यह अक्सर सुखाने वाले उपकरण की गलत सेटिंग्स के कारण होता है। सबसे आम कारण यह है कि ड्रायर का तापमान बहुत अधिक सेट कर दिया जाता है, जिससे कागज या कार्डबोर्ड पर स्याही का रंग बदल जाता है।
06 सब्सट्रेट विशेषताएँ
एक मुद्दा जिसे स्क्रीन प्रिंटिंग मास्टर अक्सर अनदेखा कर देते हैं वह है सब्सट्रेट की सतह के गुण। कागज, कार्डबोर्ड, प्लास्टिक आदि सभी बैचों में उत्पादित होते हैं, और उच्च गुणवत्ता वाले सब्सट्रेट स्थिर और सुसंगत सतह गुणों को सुनिश्चित कर सकते हैं। पर ये स्थिति नहीं है। सब्सट्रेट की सतह के गुणों में छोटे परिवर्तन से मुद्रण में रंग विचलन हो जाएगा। भले ही मुद्रण दबाव एक समान हो और यहां तक कि प्रत्येक प्रक्रिया सही ढंग से संचालित हो, सब्सट्रेट की सतह के गुणों में विसंगतियां भी मुद्रण में बड़े रंग बदलाव का कारण बनेंगी। रंग डाली।
जब एक ही उत्पाद को एक ही मुद्रण उपकरण के साथ विभिन्न सब्सट्रेट्स पर मुद्रित किया जाता है, तो रंग पर सब्सट्रेट की सतह के गुणों का प्रभाव विशेष रूप से स्पष्ट होता है। ग्राहकों को विंडो विज्ञापनों को प्लास्टिक या अन्य कार्डबोर्ड पर मुद्रित करने की आवश्यकता हो सकती है। और ग्राहकों को एक ही टुकड़े के लिए लगातार रंगों की आवश्यकता हो सकती है।
ऐसी स्थितियों में, सटीक रंग माप करना ही एकमात्र समाधान है। रंग घनत्व मापने के लिए स्पेक्ट्रोफोटोमीटर या स्पेक्ट्रल डेंसिटोमीटर का उपयोग करें। यदि कोई रंग परिवर्तन होता है, तो डेंसिटोमीटर इसे स्पष्ट रूप से प्रतिबिंबित कर सकता है, और आप अन्य प्रक्रियाओं को नियंत्रित करके इस रंग परिवर्तन को दूर कर सकते हैं।
07 अवलोकन स्थितियाँ
मानव आंखें रंग में सूक्ष्म परिवर्तनों के प्रति बहुत संवेदनशील होती हैं, और केवल प्रकाश की स्थिति में ही रंगों को अलग कर सकती हैं। इस वजह से, समान प्रकाश स्थितियों के तहत रंगों की तुलना करना सुनिश्चित करें। अन्यथा, स्याही की मात्रा या दबाव को समायोजित करने से अधिक स्याही का उत्पादन होगा। बड़े रंग का कास्ट.
कुल मिलाकर, लगातार रंग बनाए रखने की कुंजी स्याही के स्थिर प्रदर्शन को सुनिश्चित करने के लिए प्रत्येक प्रक्रिया के स्थिर नियंत्रण में निहित है। जाल के आकार का चयन, स्ट्रेच स्क्रीन का तनाव और दबाव, सब्सट्रेट की सतह की विशेषताएं और अवलोकन की स्थिति सभी का रंग विचलन पर एक निश्चित प्रभाव पड़ता है। हालाँकि, सटीक सेटिंग रिकॉर्ड और प्रत्येक प्रक्रिया का स्थिर नियंत्रण लगातार स्क्रीन प्रिंटिंग रंगों को सुनिश्चित करने की कुंजी है।
पोस्ट समय: जनवरी-08-2024