Perché la serigrafia produce dominanti di colore? Se mettiamo da parte la miscela di più colori e consideriamo un solo colore, potrebbe essere più semplice discutere le cause della dominante di colore. Questo articolo condivide diversi fattori che influenzano la deviazione del colore nella serigrafia. Il contenuto è di riferimento per gli amici che acquistano e forniscono il sistema di materiali di imballaggio Youpin:
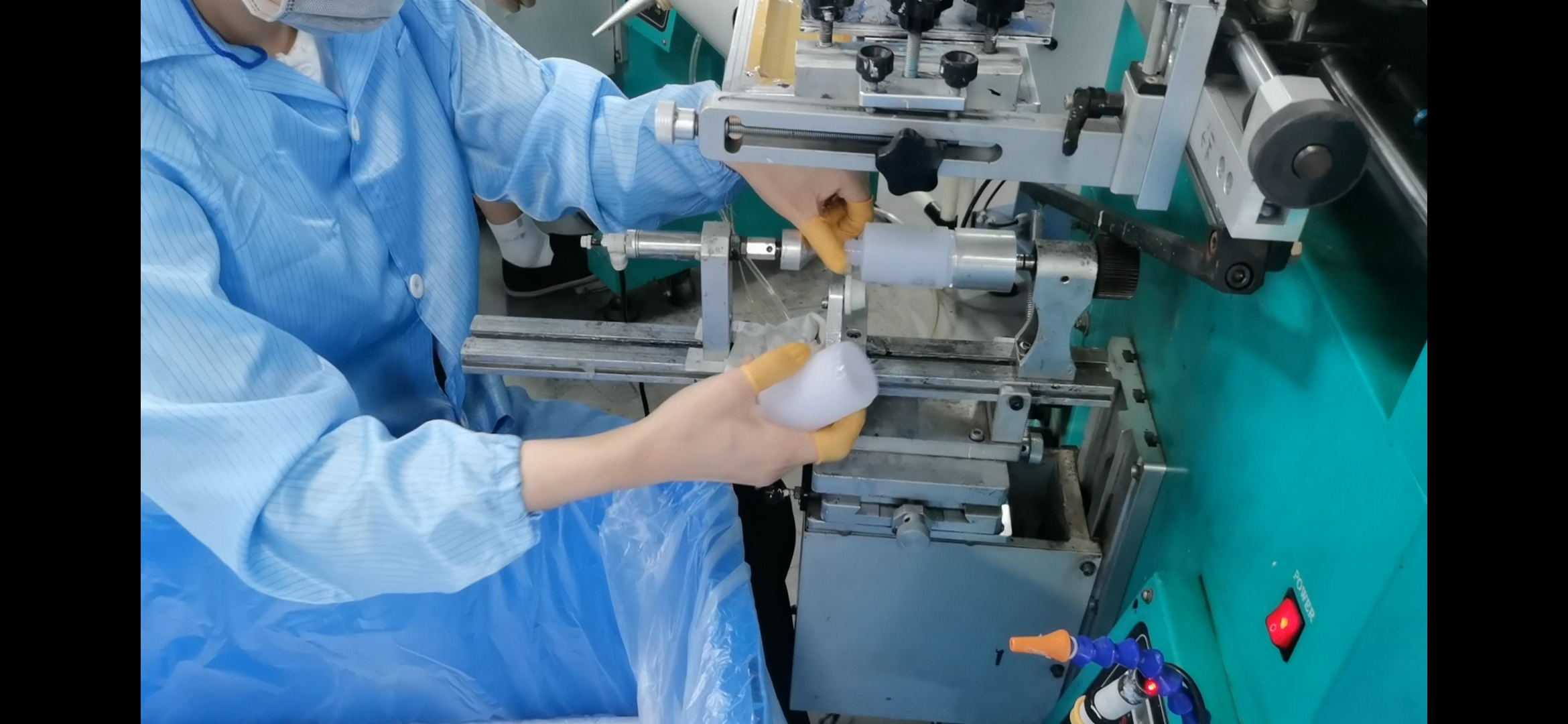
Perché la serigrafia produce dominanti di colore? Se mettiamo da parte la miscela di più colori e consideriamo un solo colore, potrebbe essere più semplice discutere le cause della dominante di colore. Questo articolo condivide diversi fattori che influenzano la deviazione del colore nella serigrafia. Il contenuto è di riferimento per gli amici che acquistano e forniscono il sistema di materiali di imballaggio Youpin:
Di seguito sono elencati alcuni dei fattori più comuni che causano deviazioni del colore nella serigrafia: preparazione dell'inchiostro, selezione della rete, tensione della rete, pressione, asciugatura, caratteristiche del substrato, condizioni di osservazione, ecc.
01 Preparazione dell'inchiostro
Miscelazione dell'inchiostro Supponendo che il pigmento dell'inchiostro utilizzato sia un pigmento standard, la causa principale della deviazione del colore è l'aggiunta di solventi come l'olio per la miscelazione dell'inchiostro all'inchiostro. In un'officina dotata di una buona attrezzatura per il controllo del colore, l'inchiostro può essere miscelato in base all'attrezzatura di controllo. Tuttavia, per la maggior parte delle aziende di stampa è impossibile disporre di queste strutture. Si affidano solo all'esperienza dei maestri artigiani quando mescolano l'inchiostro.
Generalmente, viene aggiunto olio per la regolazione dell'inchiostro per rendere l'inchiostro più adatto alla stampa. Tuttavia, una volta aggiunto l'olio di regolazione all'inchiostro, la concentrazione dei pigmenti nell'inchiostro cambierà, il che porterà a cambiamenti nelle caratteristiche cromatiche dell'inchiostro durante la stampa. Inoltre, il solvente in eccesso nell'inchiostro formerà una sottile pellicola di inchiostro dopo l'essiccazione, che ridurrà la brillantezza del colore.
C'è anche il problema della diluizione dell'inchiostro prima dell'inchiostrazione. Ad esempio, i lavoratori del negozio di inchiostri esprimono giudizi in base alla loro formula quando mescolano o diluiscono l'inchiostro. Ciò porta a un'inevitabile deviazione del colore. Se l'inchiostro è stato mescolato qualche giorno fa, se si stampa con un buon inchiostro, la dominante di colore causata da questa situazione sarà più evidente. Pertanto, è quasi impossibile evitare completamente la dominante di colore.
02 Selezione della maglia
Se pensi che la dimensione della mesh del retino sia l'unico fattore che influenza il trasferimento dell'inchiostro, incontrerai molti problemi. Anche il diametro della maglia e le rughe influiscono sul trasferimento dell'inchiostro. In generale, maggiore è la quantità di inchiostro attaccata ai fori dello schermo, maggiore sarà la quantità di inchiostro trasferita al substrato durante il processo di stampa.
Per stimare in anticipo la quantità di inchiostro che può essere trasferita da ciascuna rete, molti fornitori di telai forniscono il volume teorico di trasferimento dell'inchiostro (TIV) di ciascuna rete. TIV è un parametro che indica la dimensione della quantità di trasferimento di inchiostro del telaio. Si riferisce alla quantità di inchiostro trasferito in una determinata quantità di inchiostro verrà trasferita da ciascuna rete in condizioni di stampa specifiche. La sua unità è il volume di inchiostro per unità di area.
Per garantire toni costanti nella stampa, non è sufficiente mantenere invariato il numero di maglie del telaio, ma anche garantire che il diametro del telaio e la sua ondulazione rimangano costanti. Le modifiche a qualsiasi parametro dello schermo comporteranno modifiche nello spessore della pellicola di inchiostro durante la stampa, con conseguenti variazioni di colore.
03 Tensione netta
Se la tensione della rete è troppo piccola, la pellicola si staccherà. Se rimane troppo inchiostro nella rete, il materiale stampato si sporcherà.
Questo problema può essere risolto aumentando la distanza tra lo schermo e il substrato. Tuttavia, l'aumento della distanza tra il retino e il substrato richiede un aumento della pressione, che causerà il trasferimento di una maggiore quantità di inchiostro al substrato. per modificare la densità del colore. Il modo migliore è mantenere uniforme la tensione della rete elastica, in modo da garantire la consistenza del colore.
04 Livello di pressione
Le impostazioni di pressione corrette sono fondamentali per mantenere un colore uniforme e garantire livelli di pressione uniformi durante il processo di stampa è fondamentale. Soprattutto nei lavori di stampa ripetitivi e con volumi elevati.
Quando si parla di pressione, la prima cosa da considerare è la durezza della spatola. La durezza della spatola è ridotta, il che è positivo per la velocità di contatto, ma non è positivo per la resistenza alla flessione. Se la durezza è troppo elevata, anche l'attrito sullo schermo sarà elevato durante la stampa, influenzando così la precisione della stampa. Il secondo è l'angolo della spatola e la velocità della spatola. L'angolazione della lama dell'inchiostro ha un impatto significativo sulla quantità di inchiostro trasferito. Minore è l'angolo della lama dell'inchiostro, maggiore sarà la quantità di inchiostro trasferito. Se la velocità della lama dell'inchiostro è troppo elevata, ciò causerà un riempimento insufficiente dell'inchiostro e una stampa incompleta, compromettendo così la qualità della stampa.
Dopo aver ottenuto le impostazioni di pressione corrette per un lavoro di stampa e averle registrate accuratamente, purché si rispettino correttamente queste impostazioni durante il processo di stampa, si otterrà un prodotto di stampa soddisfacente con colori uniformi.
05 secco
A volte, il colore appare uniforme subito dopo la stampa, ma cambia una volta trovato il prodotto finito. Ciò è spesso causato da impostazioni errate dell'apparecchiatura di asciugatura. La causa più comune è che la temperatura dell'essiccatore è impostata troppo alta, causando il cambiamento del colore dell'inchiostro sulla carta o sul cartone.
06 Caratteristiche del supporto
Un problema che i maestri della serigrafia spesso trascurano sono le proprietà superficiali del substrato. Carta, cartone, plastica, ecc. sono tutti prodotti in lotti e substrati di alta qualità possono garantire proprietà superficiali stabili e costanti. Ma non è così. Piccoli cambiamenti nelle proprietà superficiali del substrato causeranno deviazioni di colore nella stampa. Anche se la pressione di stampa è uniforme e anche ogni processo viene eseguito correttamente, anche le incoerenze nelle proprietà superficiali del substrato causeranno maggiori variazioni di colore nella stampa. Dominazione del colore.
Quando lo stesso prodotto viene stampato su substrati diversi con la stessa attrezzatura di stampa, l'influenza delle proprietà superficiali del substrato sul colore è particolarmente evidente. I clienti possono richiedere che gli annunci pubblicitari sulle vetrine siano stampati su plastica o altro cartone. E i clienti potrebbero richiedere colori coerenti per lo stesso pezzo.
In situazioni come questa, l’unica soluzione è effettuare misurazioni accurate del colore. Utilizzare uno spettrofotometro o un densitometro spettrale per misurare la densità del colore. Se c'è uno spostamento di colore, il densitometro può rifletterlo chiaramente e puoi superare questo spostamento di colore controllando altri processi.
07 Condizioni di osservazione
Gli occhi umani sono molto sensibili ai sottili cambiamenti di colore e possono distinguere i colori solo in condizioni di illuminazione. Per questo motivo, assicurati di confrontare i colori nelle stesse condizioni di illuminazione. Altrimenti, la regolazione del volume o della pressione dell'inchiostro produrrà più inchiostro. Grande dominante di colore.
Nel complesso, la chiave per mantenere un colore uniforme risiede nel controllo stabile di ciascun processo per garantire prestazioni stabili dell'inchiostro. La scelta della dimensione delle maglie, della tensione e della pressione del vaglio estensibile, delle caratteristiche superficiali del substrato e delle condizioni di osservazione hanno tutti un certo impatto sulla deviazione del colore. Tuttavia, registrazioni di impostazioni accurate e un controllo stabile di ciascun processo sono la chiave per garantire colori di serigrafia coerenti.
Orario di pubblicazione: 08 gennaio 2024