スクリーン印刷で色かぶりが発生するのはなぜですか?複数の色の混合を脇に置いて、1 つの色だけを考慮すると、色かぶりの原因を議論するのが簡単になるかもしれません。この記事では、スクリーン印刷の色の偏差に影響を与えるいくつかの要因を紹介します。この内容は、Youpin 梱包材システムを購入および提供する友人による参考用です。
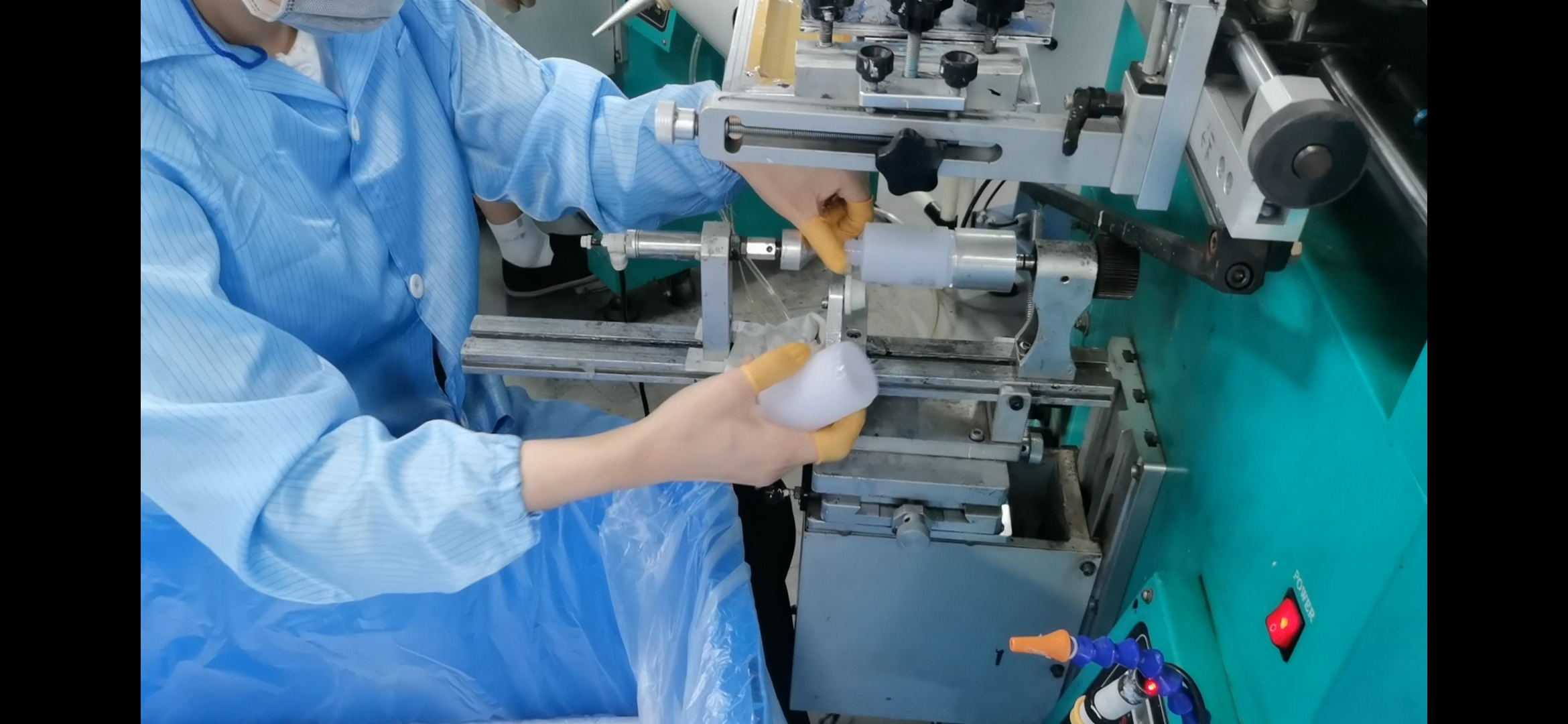
スクリーン印刷で色かぶりが発生するのはなぜですか?複数の色の混合を脇に置いて、1 つの色だけを考慮すると、色かぶりの原因を議論するのが簡単になるかもしれません。この記事では、スクリーン印刷の色の偏差に影響を与えるいくつかの要因を紹介します。この内容は、Youpin 梱包材システムを購入および提供する友人による参考用です。
スクリーン印刷で色ずれを引き起こす最も一般的な要因のいくつかを以下に示します。インクの準備、メッシュの選択、メッシュの張力、圧力、乾燥、基板の特性、観察条件などです。
01 インクの準備
インクの配合 使用するインクの顔料が標準顔料であると仮定すると、色ずれの最大の原因はインク混合油などの溶剤をインクに添加することです。色管理設備が整った工場では、管理設備に合わせてインクを調合することができます。しかし、ほとんどの印刷会社にとって、これらの設備を備えることは不可能です。インクを混ぜるときは、職人の経験だけが頼りです。
一般に、インキを印刷に適した状態にするためにインキ調整油が添加されます。しかし、調整オイルをインキに添加すると、インキ中の顔料濃度が変化し、印刷時のインキの色特性が変化してしまいます。さらに、インク内の過剰な溶剤は乾燥後にインクの薄い膜を形成し、色の明るさが低下します。
また、インキを入れる前にインキが薄まってしまうという問題もあります。たとえば、インク工場の労働者は、インクを混ぜたり、薄めたりするときに、その配合に基づいて判断します。これは避けられない色ずれにつながります。数日前にインクを混ぜた場合、良好なインクで印刷すると、この状況による色かぶりがより顕著になります。したがって、色かぶりを完全に避けることはほぼ不可能です。
02 メッシュ選択
スクリーンのメッシュ サイズだけがインク転写に影響を与えると考えていると、多くの問題に遭遇することになります。メッシュの直径やシワもインク転写に影響します。一般に、スクリーンのインク穴に付着するインクが多ければ多いほど、印刷プロセス中により多くのインクが素材に転写されます。
各メッシュがどれだけのインクを転写できるかを事前に見積もるために、多くのスクリーン サプライヤーは各メッシュの理論上のインク転写量 (TIV) を提供しています。 TIVは、スクリーンのインク転写量の大小を示すパラメータである。これは、特定の印刷条件下で各メッシュによって転写されるインクの量を指します。単位は単位面積当たりのインクの体積です。
印刷の階調を一定にするためには、スクリーンのメッシュ数を変えるだけではなく、スクリーンの直径やうねりを一定にすることが重要です。スクリーンのパラメータを変更すると、印刷中のインク膜の厚さが変化し、色の変化が生じます。
03 ネットテンション
ネットの張力が弱すぎるとフィルムが剥がれる原因となります。メッシュ内にインクが滞留しすぎると印刷物が汚れてしまいます。
この問題は、スクリーンと基板の間の距離を長くすることで解決できます。ただし、スクリーンと素材の間の距離を大きくすると、圧力を高める必要があり、より多くのインクが素材に転写されます。色の濃さを変更します。色の一貫性を確保するには、ストレッチネットの張力を均一に保つことが最善の方法です。
04 圧力レベル
一貫した色を維持するには適切な圧力設定が重要であり、印刷プロセス中に均一な圧力レベルを確保することが重要です。特に大量の反復的な印刷ジョブの場合はそうです。
圧力に関しては、まずスキージの硬さを考慮する必要があります。スキージの硬度が低く、接触率には優れていますが、耐屈曲性には劣ります。硬度が高すぎると印刷時にスクリーンとの摩擦が大きくなり、印刷精度に影響を与えます。 2つ目はスキージの角度とスキージ速度です。インクナイフの角度は、インクの転写量に大きく影響します。インクナイフの角度が小さいほど、インクの転移量が多くなります。インクナイフの速度が速すぎると、インクの充填が不十分になり、印刷が不完全になり、印刷品質に影響を与えます。
印刷ジョブの正しい圧力設定を取得し、それを正確に記録したら、印刷プロセス中にこれらの設定に正しく従う限り、一貫した色の満足のいく印刷製品が得られます。
05 ドライ
印刷直後は色が安定しているように見えても、完成品を確認した後に色が変わってしまうこともあります。これは多くの場合、乾燥装置の設定が間違っていることが原因で発生します。最も一般的な原因は、乾燥機の温度設定が高すぎることで、紙やボール紙上のインクの色が変化することです。
06 基板の特性
スクリーン印刷マスターが見落としがちな問題の 1 つは、基板の表面特性です。紙、ボール紙、プラスチックなどはすべてバッチで生産され、高品質の基材により安定した一貫した表面特性が保証されます。しかしそうではありません。素材の表面特性がわずかに変化すると、印刷に色のずれが生じます。たとえ印圧が均一で各工程が正しく行われていたとしても、基材の表面特性にばらつきがあると、印刷時に大きな色ずれが発生します。色かぶり。
同じ製品を同じ印刷装置を使用して異なる基材に印刷する場合、基材の表面特性が色に与える影響は特に顕著です。顧客は、ウィンドウ広告をプラスチックまたはその他のボール紙に印刷することを要求する場合があります。また、クライアントは同じ作品に一貫した色を要求する場合があります。
このような状況では、唯一の解決策は正確な色測定を行うことです。色の濃度を測定するには、分光光度計または分光濃度計を使用します。カラーシフトがある場合、濃度計はそれを明確に反映することができ、他のプロセスを制御することでこのカラーシフトを克服できます。
07 観測条件
人間の目は色の微妙な変化に非常に敏感で、照明条件下でのみ色を識別できます。このため、必ず同じ照明条件下で色を比較してください。それ以外の場合は、インクの量または圧力を調整すると、より多くのインクが生成されます。大きな色かぶり。
安定した色を維持するには、各工程を安定的に制御し、インクの安定した性能を確保することが重要です。メッシュサイズの選択、ストレッチスクリーンの張力と圧力、基材の表面特性、および観察条件はすべて、色の偏差に一定の影響を与えます。しかし、スクリーン印刷の色を安定させるには、正確な設定記録と各工程の安定した制御が鍵となります。
投稿時刻: 2024 年 1 月 8 日