ಪರದೆಯ ಮುದ್ರಣವು ಬಣ್ಣ ಎರಕಹೊಯ್ದಗಳನ್ನು ಏಕೆ ಉತ್ಪಾದಿಸುತ್ತದೆ? ನಾವು ಹಲವಾರು ಬಣ್ಣಗಳ ಮಿಶ್ರಣವನ್ನು ಬದಿಗಿಟ್ಟು ಒಂದು ಬಣ್ಣವನ್ನು ಮಾತ್ರ ಪರಿಗಣಿಸಿದರೆ, ಬಣ್ಣ ಎರಕಹೊಯ್ದ ಕಾರಣಗಳನ್ನು ಚರ್ಚಿಸಲು ಇದು ಸರಳವಾಗಬಹುದು. ಈ ಲೇಖನವು ಪರದೆಯ ಮುದ್ರಣದಲ್ಲಿ ಬಣ್ಣ ವಿಚಲನದ ಮೇಲೆ ಪರಿಣಾಮ ಬೀರುವ ಹಲವಾರು ಅಂಶಗಳನ್ನು ಹಂಚಿಕೊಳ್ಳುತ್ತದೆ. ಯೂಪಿನ್ ಪ್ಯಾಕೇಜಿಂಗ್ ಮೆಟೀರಿಯಲ್ ಸಿಸ್ಟಮ್ ಅನ್ನು ಖರೀದಿಸುವ ಮತ್ತು ಪೂರೈಸುವ ಸ್ನೇಹಿತರಿಂದ ವಿಷಯವು ಉಲ್ಲೇಖವಾಗಿದೆ:
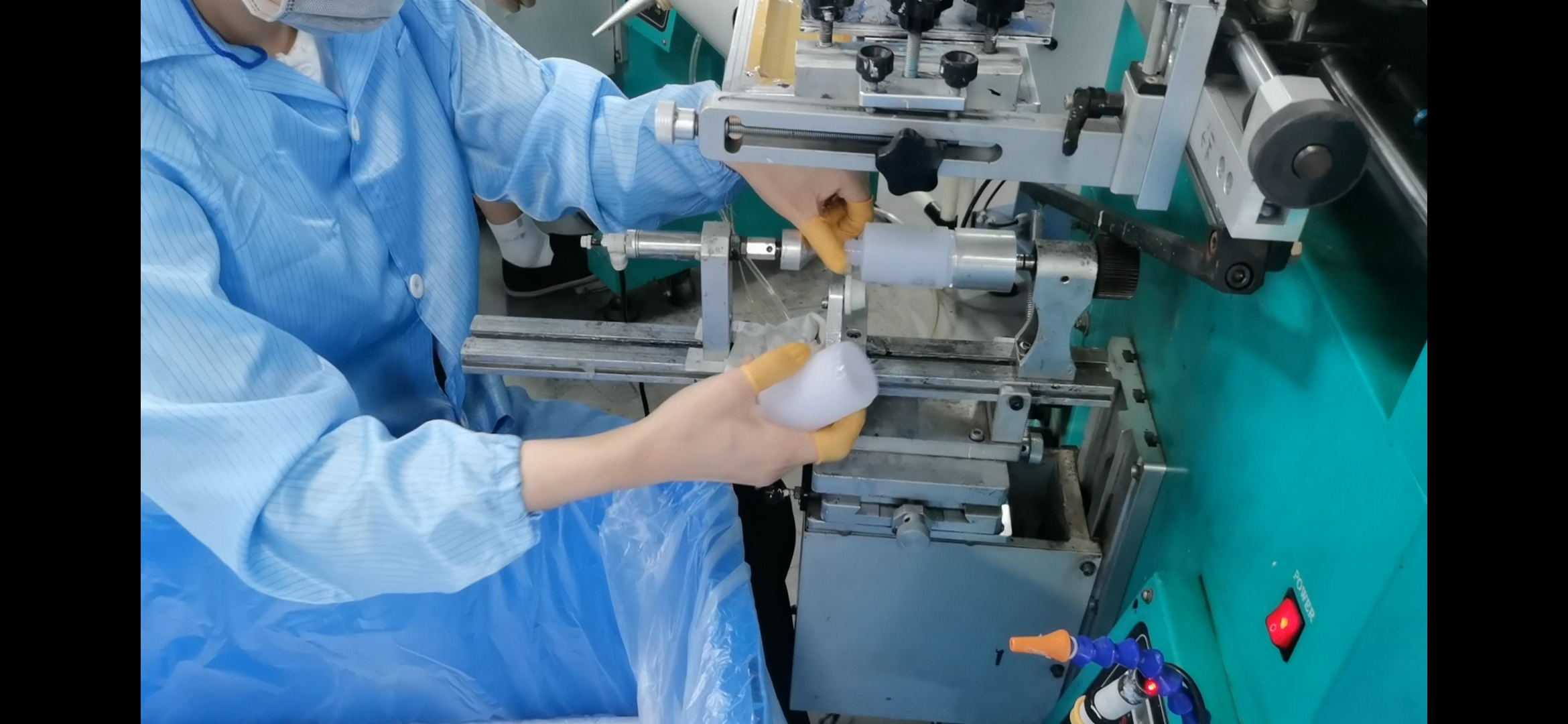
ಪರದೆಯ ಮುದ್ರಣವು ಬಣ್ಣ ಎರಕಹೊಯ್ದಗಳನ್ನು ಏಕೆ ಉತ್ಪಾದಿಸುತ್ತದೆ? ನಾವು ಹಲವಾರು ಬಣ್ಣಗಳ ಮಿಶ್ರಣವನ್ನು ಬದಿಗಿಟ್ಟು ಒಂದು ಬಣ್ಣವನ್ನು ಮಾತ್ರ ಪರಿಗಣಿಸಿದರೆ, ಬಣ್ಣ ಎರಕಹೊಯ್ದ ಕಾರಣಗಳನ್ನು ಚರ್ಚಿಸಲು ಇದು ಸರಳವಾಗಬಹುದು. ಈ ಲೇಖನವು ಪರದೆಯ ಮುದ್ರಣದಲ್ಲಿ ಬಣ್ಣ ವಿಚಲನದ ಮೇಲೆ ಪರಿಣಾಮ ಬೀರುವ ಹಲವಾರು ಅಂಶಗಳನ್ನು ಹಂಚಿಕೊಳ್ಳುತ್ತದೆ. ಯೂಪಿನ್ ಪ್ಯಾಕೇಜಿಂಗ್ ಮೆಟೀರಿಯಲ್ ಸಿಸ್ಟಮ್ ಅನ್ನು ಖರೀದಿಸುವ ಮತ್ತು ಪೂರೈಸುವ ಸ್ನೇಹಿತರಿಂದ ವಿಷಯವು ಉಲ್ಲೇಖವಾಗಿದೆ:
ಪರದೆಯ ಮುದ್ರಣದಲ್ಲಿ ಬಣ್ಣ ವಿಚಲನವನ್ನು ಉಂಟುಮಾಡುವ ಕೆಲವು ಸಾಮಾನ್ಯ ಅಂಶಗಳನ್ನು ಕೆಳಗೆ ಪಟ್ಟಿ ಮಾಡಲಾಗಿದೆ: ಶಾಯಿ ತಯಾರಿಕೆ, ಜಾಲರಿ ಆಯ್ಕೆ, ಜಾಲರಿ ಒತ್ತಡ, ಒತ್ತಡ, ಒಣಗಿಸುವುದು, ತಲಾಧಾರ ಗುಣಲಕ್ಷಣಗಳು, ವೀಕ್ಷಣೆ ಪರಿಸ್ಥಿತಿಗಳು, ಇತ್ಯಾದಿ.
01 ಶಾಯಿ ತಯಾರಿಕೆ
ಶಾಯಿ ಮಿಶ್ರಣವು ಬಳಸಿದ ಶಾಯಿಯ ವರ್ಣದ್ರವ್ಯವು ಪ್ರಮಾಣಿತ ವರ್ಣದ್ರವ್ಯವಾಗಿದೆ ಎಂದು ಭಾವಿಸಿದರೆ, ಬಣ್ಣ ವಿಚಲನಕ್ಕೆ ದೊಡ್ಡ ಕಾರಣವೆಂದರೆ ಶಾಯಿಯನ್ನು ಮಿಶ್ರಣ ಮಾಡುವ ಎಣ್ಣೆಯಂತಹ ದ್ರಾವಕಗಳನ್ನು ಸೇರಿಸುವುದು. ಉತ್ತಮ ಬಣ್ಣ ನಿಯಂತ್ರಣ ಸಾಧನಗಳೊಂದಿಗೆ ಕಾರ್ಯಾಗಾರದಲ್ಲಿ, ನಿಯಂತ್ರಣ ಸಾಧನದ ಪ್ರಕಾರ ಶಾಯಿಯನ್ನು ಬೆರೆಸಬಹುದು. ಆದಾಗ್ಯೂ, ಹೆಚ್ಚಿನ ಮುದ್ರಣ ಕಂಪನಿಗಳಿಗೆ, ಈ ಸೌಲಭ್ಯಗಳನ್ನು ಹೊಂದಲು ಅಸಾಧ್ಯವಾಗಿದೆ. ಶಾಯಿ ಮಿಶ್ರಣ ಮಾಡುವಾಗ ಅವರು ಮಾಸ್ಟರ್ ಕೆಲಸಗಾರರ ಅನುಭವವನ್ನು ಮಾತ್ರ ಅವಲಂಬಿಸುತ್ತಾರೆ.
ಸಾಮಾನ್ಯವಾಗಿ, ಶಾಯಿಯನ್ನು ಮುದ್ರಣಕ್ಕೆ ಹೆಚ್ಚು ಸೂಕ್ತವಾಗಿಸಲು ಶಾಯಿ-ಹೊಂದಾಣಿಕೆ ತೈಲವನ್ನು ಸೇರಿಸಲಾಗುತ್ತದೆ. ಆದಾಗ್ಯೂ, ಒಮ್ಮೆ ಸರಿಹೊಂದಿಸುವ ತೈಲವನ್ನು ಶಾಯಿಗೆ ಸೇರಿಸಿದರೆ, ಶಾಯಿಯಲ್ಲಿನ ವರ್ಣದ್ರವ್ಯಗಳ ಸಾಂದ್ರತೆಯು ಬದಲಾಗುತ್ತದೆ, ಇದು ಮುದ್ರಣದ ಸಮಯದಲ್ಲಿ ಶಾಯಿಯ ಬಣ್ಣ ಗುಣಲಕ್ಷಣಗಳಲ್ಲಿ ಬದಲಾವಣೆಗಳಿಗೆ ಕಾರಣವಾಗುತ್ತದೆ. ಇದರ ಜೊತೆಗೆ, ಶಾಯಿಯಲ್ಲಿನ ಹೆಚ್ಚುವರಿ ದ್ರಾವಕವು ಒಣಗಿದ ನಂತರ ಶಾಯಿಯ ತೆಳುವಾದ ಫಿಲ್ಮ್ ಅನ್ನು ರೂಪಿಸುತ್ತದೆ, ಇದು ಬಣ್ಣದ ಹೊಳಪನ್ನು ಕಡಿಮೆ ಮಾಡುತ್ತದೆ.
ಮಸಿ ಬಳಿಯುವ ಮೊದಲು ಶಾಯಿಯನ್ನು ದುರ್ಬಲಗೊಳಿಸುವ ಸಮಸ್ಯೆಯೂ ಇದೆ. ಉದಾಹರಣೆಗೆ, ಶಾಯಿ ಅಂಗಡಿಯಲ್ಲಿ ಕೆಲಸಗಾರರು ಶಾಯಿಯನ್ನು ಮಿಶ್ರಣ ಮಾಡುವಾಗ ಅಥವಾ ದುರ್ಬಲಗೊಳಿಸುವಾಗ ಅವರ ಸೂತ್ರದ ಆಧಾರದ ಮೇಲೆ ತೀರ್ಪುಗಳನ್ನು ಮಾಡುತ್ತಾರೆ. ಇದು ಅನಿವಾರ್ಯ ಬಣ್ಣ ವಿಚಲನಕ್ಕೆ ಕಾರಣವಾಗುತ್ತದೆ. ಕೆಲವು ದಿನಗಳ ಹಿಂದೆ ಶಾಯಿಯನ್ನು ಬೆರೆಸಿದರೆ, ನೀವು ಉತ್ತಮ ಶಾಯಿಯಿಂದ ಮುದ್ರಿಸಿದರೆ, ಈ ಪರಿಸ್ಥಿತಿಯಿಂದ ಉಂಟಾಗುವ ಬಣ್ಣವು ಹೆಚ್ಚು ಸ್ಪಷ್ಟವಾಗಿರುತ್ತದೆ. ಆದ್ದರಿಂದ, ಬಣ್ಣ ಎರಕಹೊಯ್ದವನ್ನು ಸಂಪೂರ್ಣವಾಗಿ ತಪ್ಪಿಸಲು ಅಸಾಧ್ಯವಾಗಿದೆ.
02 ಮೆಶ್ ಆಯ್ಕೆ
ಪರದೆಯ ಜಾಲರಿಯ ಗಾತ್ರವು ಶಾಯಿ ವರ್ಗಾವಣೆಯ ಮೇಲೆ ಪರಿಣಾಮ ಬೀರುವ ಏಕೈಕ ಅಂಶವಾಗಿದೆ ಎಂದು ನೀವು ಭಾವಿಸಿದರೆ, ನೀವು ಬಹಳಷ್ಟು ತೊಂದರೆಗಳನ್ನು ಎದುರಿಸಬೇಕಾಗುತ್ತದೆ. ಜಾಲರಿಯ ವ್ಯಾಸ ಮತ್ತು ಸುಕ್ಕುಗಳು ಸಹ ಶಾಯಿ ವರ್ಗಾವಣೆಯ ಮೇಲೆ ಪರಿಣಾಮ ಬೀರುತ್ತವೆ. ಸಾಮಾನ್ಯವಾಗಿ, ಪರದೆಯ ಇಂಕ್ ರಂಧ್ರಗಳಿಗೆ ಹೆಚ್ಚು ಶಾಯಿಯನ್ನು ಜೋಡಿಸಲಾಗುತ್ತದೆ, ಮುದ್ರಣ ಪ್ರಕ್ರಿಯೆಯಲ್ಲಿ ಹೆಚ್ಚು ಶಾಯಿಯನ್ನು ತಲಾಧಾರಕ್ಕೆ ವರ್ಗಾಯಿಸಲಾಗುತ್ತದೆ.
ಪ್ರತಿ ಜಾಲರಿಯ ಮೂಲಕ ಎಷ್ಟು ಶಾಯಿಯನ್ನು ವರ್ಗಾಯಿಸಬಹುದು ಎಂಬುದನ್ನು ಮುಂಚಿತವಾಗಿ ಅಂದಾಜು ಮಾಡಲು, ಅನೇಕ ಪರದೆಯ ಪೂರೈಕೆದಾರರು ಪ್ರತಿ ಜಾಲರಿಯ ಸೈದ್ಧಾಂತಿಕ ಶಾಯಿ ವರ್ಗಾವಣೆ ಪರಿಮಾಣವನ್ನು (TIV) ಒದಗಿಸುತ್ತಾರೆ. TIV ಎಂಬುದು ಪರದೆಯ ಶಾಯಿ ವರ್ಗಾವಣೆಯ ಮೊತ್ತದ ಗಾತ್ರವನ್ನು ಸೂಚಿಸುವ ಒಂದು ನಿಯತಾಂಕವಾಗಿದೆ. ನಿರ್ದಿಷ್ಟ ಮುದ್ರಣ ಪರಿಸ್ಥಿತಿಗಳಲ್ಲಿ ಪ್ರತಿ ಜಾಲರಿಯ ಮೂಲಕ ಎಷ್ಟು ಶಾಯಿಯನ್ನು ವರ್ಗಾಯಿಸಲಾಗುತ್ತದೆ ಎಂಬುದನ್ನು ನಿರ್ದಿಷ್ಟವಾಗಿ ವರ್ಗಾಯಿಸಲಾದ ಶಾಯಿಯ ಪ್ರಮಾಣವನ್ನು ಇದು ಸೂಚಿಸುತ್ತದೆ. ಇದರ ಘಟಕವು ಪ್ರತಿ ಯೂನಿಟ್ ಪ್ರದೇಶಕ್ಕೆ ಶಾಯಿಯ ಪರಿಮಾಣವಾಗಿದೆ.
ಮುದ್ರಣದಲ್ಲಿ ಸ್ಥಿರವಾದ ಟೋನ್ಗಳನ್ನು ಖಚಿತಪಡಿಸಿಕೊಳ್ಳಲು, ಪರದೆಯ ಮೆಶ್ ಸಂಖ್ಯೆಯನ್ನು ಬದಲಾಗದೆ ಇರಿಸಲು ಸಾಕಾಗುವುದಿಲ್ಲ, ಆದರೆ ಪರದೆಯ ವ್ಯಾಸ ಮತ್ತು ಅದರ ಅಲೆಯು ಸ್ಥಿರವಾಗಿರುತ್ತದೆ ಎಂದು ಖಚಿತಪಡಿಸಿಕೊಳ್ಳಲು. ಪರದೆಯ ಯಾವುದೇ ಪ್ಯಾರಾಮೀಟರ್ನಲ್ಲಿನ ಬದಲಾವಣೆಗಳು ಮುದ್ರಣದ ಸಮಯದಲ್ಲಿ ಇಂಕ್ ಫಿಲ್ಮ್ನ ದಪ್ಪದಲ್ಲಿ ಬದಲಾವಣೆಗಳಿಗೆ ಕಾರಣವಾಗುತ್ತವೆ, ಇದರ ಪರಿಣಾಮವಾಗಿ ಬಣ್ಣ ಬದಲಾವಣೆಗಳು ಕಂಡುಬರುತ್ತವೆ.
03 ನಿವ್ವಳ ಒತ್ತಡ
ನೆಟ್ನ ಒತ್ತಡವು ತುಂಬಾ ಚಿಕ್ಕದಾಗಿದ್ದರೆ, ಅದು ಫಿಲ್ಮ್ ಅನ್ನು ಸಿಪ್ಪೆ ತೆಗೆಯಲು ಕಾರಣವಾಗುತ್ತದೆ. ಜಾಲರಿಯಲ್ಲಿ ಹೆಚ್ಚು ಶಾಯಿ ಇದ್ದರೆ, ಮುದ್ರಿತ ವಸ್ತುವು ಕೊಳಕು ಆಗುತ್ತದೆ.
ಪರದೆ ಮತ್ತು ತಲಾಧಾರದ ನಡುವಿನ ಅಂತರವನ್ನು ಹೆಚ್ಚಿಸುವ ಮೂಲಕ ಈ ಸಮಸ್ಯೆಯನ್ನು ಪರಿಹರಿಸಬಹುದು. ಆದಾಗ್ಯೂ, ಪರದೆ ಮತ್ತು ತಲಾಧಾರದ ನಡುವಿನ ಅಂತರವನ್ನು ಹೆಚ್ಚಿಸುವುದರಿಂದ ಒತ್ತಡವನ್ನು ಹೆಚ್ಚಿಸುವ ಅಗತ್ಯವಿರುತ್ತದೆ, ಇದು ತಲಾಧಾರಕ್ಕೆ ಹೆಚ್ಚಿನ ಶಾಯಿಯನ್ನು ವರ್ಗಾಯಿಸಲು ಕಾರಣವಾಗುತ್ತದೆ. ಬಣ್ಣದ ಸಾಂದ್ರತೆಯನ್ನು ಬದಲಾಯಿಸಲು. ಸ್ಟ್ರೆಚ್ ನೆಟ್ ಏಕರೂಪದ ಒತ್ತಡವನ್ನು ಇಟ್ಟುಕೊಳ್ಳುವುದು ಉತ್ತಮ ಮಾರ್ಗವಾಗಿದೆ, ಇದರಿಂದಾಗಿ ಬಣ್ಣದ ಸ್ಥಿರತೆಯನ್ನು ಖಚಿತಪಡಿಸುತ್ತದೆ.
04 ಒತ್ತಡದ ಮಟ್ಟ
ಸ್ಥಿರವಾದ ಬಣ್ಣವನ್ನು ಕಾಪಾಡಿಕೊಳ್ಳಲು ಸರಿಯಾದ ಒತ್ತಡದ ಸೆಟ್ಟಿಂಗ್ಗಳು ನಿರ್ಣಾಯಕವಾಗಿವೆ ಮತ್ತು ಮುದ್ರಣ ಪ್ರಕ್ರಿಯೆಯಲ್ಲಿ ಏಕರೂಪದ ಒತ್ತಡದ ಮಟ್ಟವನ್ನು ಖಚಿತಪಡಿಸಿಕೊಳ್ಳುವುದು ನಿರ್ಣಾಯಕವಾಗಿದೆ. ವಿಶೇಷವಾಗಿ ಹೆಚ್ಚಿನ ಪ್ರಮಾಣದ, ಪುನರಾವರ್ತಿತ ಮುದ್ರಣ ಉದ್ಯೋಗಗಳಲ್ಲಿ.
ಒತ್ತಡಕ್ಕೆ ಬಂದಾಗ, ಸ್ಕ್ವೀಜಿಯ ಗಡಸುತನವನ್ನು ಪರಿಗಣಿಸಬೇಕಾದ ಮೊದಲ ವಿಷಯ. ಸ್ಕ್ವೀಜಿಯ ಗಡಸುತನವು ಚಿಕ್ಕದಾಗಿದೆ, ಇದು ಸಂಪರ್ಕ ದರಕ್ಕೆ ಉತ್ತಮವಾಗಿದೆ, ಆದರೆ ಬಾಗುವ ಪ್ರತಿರೋಧಕ್ಕೆ ಇದು ಉತ್ತಮವಲ್ಲ. ಗಡಸುತನವು ತುಂಬಾ ಹೆಚ್ಚಿದ್ದರೆ, ಮುದ್ರಣದ ಸಮಯದಲ್ಲಿ ಪರದೆಯ ಮೇಲಿನ ಘರ್ಷಣೆಯು ದೊಡ್ಡದಾಗಿರುತ್ತದೆ, ಹೀಗಾಗಿ ಮುದ್ರಣದ ನಿಖರತೆಯ ಮೇಲೆ ಪರಿಣಾಮ ಬೀರುತ್ತದೆ. ಎರಡನೆಯದು ಸ್ಕ್ವೀಜಿಯ ಕೋನ ಮತ್ತು ಸ್ಕ್ವೀಗೀ ವೇಗ. ಶಾಯಿ ಚಾಕುವಿನ ಕೋನವು ಶಾಯಿ ವರ್ಗಾವಣೆಯ ಪ್ರಮಾಣದ ಮೇಲೆ ಗಮನಾರ್ಹ ಪರಿಣಾಮ ಬೀರುತ್ತದೆ. ಶಾಯಿ ಚಾಕುವಿನ ಕೋನವು ಚಿಕ್ಕದಾಗಿದ್ದರೆ, ಶಾಯಿ ವರ್ಗಾವಣೆಯ ಪ್ರಮಾಣವು ಹೆಚ್ಚಾಗುತ್ತದೆ. ಶಾಯಿ ಚಾಕುವಿನ ವೇಗವು ತುಂಬಾ ವೇಗವಾಗಿದ್ದರೆ, ಇದು ಸಾಕಷ್ಟು ಶಾಯಿ ತುಂಬುವಿಕೆ ಮತ್ತು ಅಪೂರ್ಣ ಮುದ್ರೆಯನ್ನು ಉಂಟುಮಾಡುತ್ತದೆ, ಹೀಗಾಗಿ ಮುದ್ರಣದ ಗುಣಮಟ್ಟವನ್ನು ಪರಿಣಾಮ ಬೀರುತ್ತದೆ.
ಮುದ್ರಣ ಕಾರ್ಯಕ್ಕಾಗಿ ನೀವು ಸರಿಯಾದ ಒತ್ತಡದ ಸೆಟ್ಟಿಂಗ್ಗಳನ್ನು ಪಡೆದ ನಂತರ ಮತ್ತು ಅವುಗಳನ್ನು ನಿಖರವಾಗಿ ದಾಖಲಿಸಿದರೆ, ಮುದ್ರಣ ಪ್ರಕ್ರಿಯೆಯಲ್ಲಿ ನೀವು ಈ ಸೆಟ್ಟಿಂಗ್ಗಳನ್ನು ಸರಿಯಾಗಿ ಅನುಸರಿಸುವವರೆಗೆ, ನೀವು ಸ್ಥಿರವಾದ ಬಣ್ಣಗಳೊಂದಿಗೆ ತೃಪ್ತಿದಾಯಕ ಮುದ್ರಣ ಉತ್ಪನ್ನವನ್ನು ಪಡೆಯುತ್ತೀರಿ.
05 ಶುಷ್ಕ
ಕೆಲವೊಮ್ಮೆ, ಮುದ್ರಣದ ನಂತರ ಬಣ್ಣವು ಸ್ಥಿರವಾಗಿ ಕಾಣುತ್ತದೆ, ಆದರೆ ಸಿದ್ಧಪಡಿಸಿದ ಉತ್ಪನ್ನವು ಕಂಡುಬಂದ ನಂತರ ಬಣ್ಣವು ಬದಲಾಗುತ್ತದೆ. ಒಣಗಿಸುವ ಸಲಕರಣೆಗಳ ತಪ್ಪಾದ ಸೆಟ್ಟಿಂಗ್ಗಳಿಂದ ಇದು ಹೆಚ್ಚಾಗಿ ಉಂಟಾಗುತ್ತದೆ. ಅತ್ಯಂತ ಸಾಮಾನ್ಯವಾದ ಕಾರಣವೆಂದರೆ ಡ್ರೈಯರ್ ತಾಪಮಾನವು ತುಂಬಾ ಹೆಚ್ಚಾಗಿರುತ್ತದೆ, ಇದು ಕಾಗದ ಅಥವಾ ರಟ್ಟಿನ ಮೇಲೆ ಶಾಯಿ ಬಣ್ಣವನ್ನು ಬದಲಾಯಿಸುತ್ತದೆ.
06 ತಲಾಧಾರದ ಗುಣಲಕ್ಷಣಗಳು
ಸ್ಕ್ರೀನ್ ಪ್ರಿಂಟಿಂಗ್ ಮಾಸ್ಟರ್ಗಳು ಸಾಮಾನ್ಯವಾಗಿ ಕಡೆಗಣಿಸುವ ಒಂದು ಸಮಸ್ಯೆಯು ತಲಾಧಾರದ ಮೇಲ್ಮೈ ಗುಣಲಕ್ಷಣಗಳಾಗಿವೆ. ಪೇಪರ್, ಕಾರ್ಡ್ಬೋರ್ಡ್, ಪ್ಲ್ಯಾಸ್ಟಿಕ್ ಇತ್ಯಾದಿಗಳನ್ನು ಬ್ಯಾಚ್ಗಳಲ್ಲಿ ಉತ್ಪಾದಿಸಲಾಗುತ್ತದೆ ಮತ್ತು ಉತ್ತಮ-ಗುಣಮಟ್ಟದ ತಲಾಧಾರಗಳು ಸ್ಥಿರ ಮತ್ತು ಸ್ಥಿರವಾದ ಮೇಲ್ಮೈ ಗುಣಲಕ್ಷಣಗಳನ್ನು ಖಚಿತಪಡಿಸಿಕೊಳ್ಳಬಹುದು. ಆದರೆ ಇದು ಹಾಗಲ್ಲ. ತಲಾಧಾರದ ಮೇಲ್ಮೈ ಗುಣಲಕ್ಷಣಗಳಲ್ಲಿನ ಸಣ್ಣ ಬದಲಾವಣೆಗಳು ಮುದ್ರಣದಲ್ಲಿ ಬಣ್ಣ ವ್ಯತ್ಯಾಸಗಳನ್ನು ಉಂಟುಮಾಡುತ್ತವೆ. ಮುದ್ರಣ ಒತ್ತಡವು ಏಕರೂಪವಾಗಿದ್ದರೂ ಮತ್ತು ಪ್ರತಿ ಪ್ರಕ್ರಿಯೆಯು ಸರಿಯಾಗಿ ಕಾರ್ಯನಿರ್ವಹಿಸಿದರೂ ಸಹ, ತಲಾಧಾರದ ಮೇಲ್ಮೈ ಗುಣಲಕ್ಷಣಗಳಲ್ಲಿನ ಅಸಮಂಜಸತೆಯು ಮುದ್ರಣದಲ್ಲಿ ದೊಡ್ಡ ಬಣ್ಣ ಬದಲಾವಣೆಗಳನ್ನು ಉಂಟುಮಾಡುತ್ತದೆ. ಬಣ್ಣ ಎರಕಹೊಯ್ದ.
ಒಂದೇ ಉತ್ಪನ್ನವನ್ನು ಒಂದೇ ಮುದ್ರಣ ಸಾಧನದೊಂದಿಗೆ ವಿವಿಧ ತಲಾಧಾರಗಳಲ್ಲಿ ಮುದ್ರಿಸಿದಾಗ, ಬಣ್ಣದ ಮೇಲೆ ತಲಾಧಾರದ ಮೇಲ್ಮೈ ಗುಣಲಕ್ಷಣಗಳ ಪ್ರಭಾವವು ನಿರ್ದಿಷ್ಟವಾಗಿ ಸ್ಪಷ್ಟವಾಗಿರುತ್ತದೆ. ಗ್ರಾಹಕರು ಕಿಟಕಿ ಜಾಹೀರಾತುಗಳನ್ನು ಪ್ಲಾಸ್ಟಿಕ್ ಅಥವಾ ಇತರ ರಟ್ಟಿನ ಮೇಲೆ ಮುದ್ರಿಸಬೇಕಾಗಬಹುದು. ಮತ್ತು ಗ್ರಾಹಕರಿಗೆ ಒಂದೇ ತುಂಡುಗೆ ಸ್ಥಿರವಾದ ಬಣ್ಣಗಳು ಬೇಕಾಗಬಹುದು.
ಅಂತಹ ಸಂದರ್ಭಗಳಲ್ಲಿ, ನಿಖರವಾದ ಬಣ್ಣ ಮಾಪನಗಳನ್ನು ಮಾಡುವುದು ಏಕೈಕ ಪರಿಹಾರವಾಗಿದೆ. ಬಣ್ಣದ ಸಾಂದ್ರತೆಯನ್ನು ಅಳೆಯಲು ಸ್ಪೆಕ್ಟ್ರೋಫೋಟೋಮೀಟರ್ ಅಥವಾ ಸ್ಪೆಕ್ಟ್ರಲ್ ಡೆನ್ಸಿಟೋಮೀಟರ್ ಬಳಸಿ. ಬಣ್ಣ ಬದಲಾವಣೆಯಿದ್ದರೆ, ಡೆನ್ಸಿಟೋಮೀಟರ್ ಅದನ್ನು ಸ್ಪಷ್ಟವಾಗಿ ಪ್ರತಿಬಿಂಬಿಸುತ್ತದೆ ಮತ್ತು ಇತರ ಪ್ರಕ್ರಿಯೆಗಳನ್ನು ನಿಯಂತ್ರಿಸುವ ಮೂಲಕ ನೀವು ಈ ಬಣ್ಣ ಬದಲಾವಣೆಯನ್ನು ಜಯಿಸಬಹುದು.
07 ವೀಕ್ಷಣಾ ಪರಿಸ್ಥಿತಿಗಳು
ಮಾನವನ ಕಣ್ಣುಗಳು ಬಣ್ಣದಲ್ಲಿನ ಸೂಕ್ಷ್ಮ ಬದಲಾವಣೆಗಳಿಗೆ ಬಹಳ ಸೂಕ್ಷ್ಮವಾಗಿರುತ್ತವೆ ಮತ್ತು ಬೆಳಕಿನ ಪರಿಸ್ಥಿತಿಗಳಲ್ಲಿ ಮಾತ್ರ ಬಣ್ಣಗಳನ್ನು ಪ್ರತ್ಯೇಕಿಸಬಹುದು. ಈ ಕಾರಣದಿಂದಾಗಿ, ಅದೇ ಬೆಳಕಿನ ಪರಿಸ್ಥಿತಿಗಳಲ್ಲಿ ಬಣ್ಣಗಳನ್ನು ಹೋಲಿಸಲು ಖಚಿತಪಡಿಸಿಕೊಳ್ಳಿ. ಇಲ್ಲದಿದ್ದರೆ, ಶಾಯಿಯ ಪರಿಮಾಣ ಅಥವಾ ಒತ್ತಡವನ್ನು ಸರಿಹೊಂದಿಸುವುದು ಹೆಚ್ಚು ಶಾಯಿಯನ್ನು ಉತ್ಪಾದಿಸುತ್ತದೆ. ದೊಡ್ಡ ಬಣ್ಣದ ಎರಕಹೊಯ್ದ.
ಒಟ್ಟಾರೆಯಾಗಿ, ಸ್ಥಿರವಾದ ಬಣ್ಣವನ್ನು ಕಾಪಾಡಿಕೊಳ್ಳುವ ಕೀಲಿಯು ಶಾಯಿಯ ಸ್ಥಿರ ಕಾರ್ಯಕ್ಷಮತೆಯನ್ನು ಖಚಿತಪಡಿಸಿಕೊಳ್ಳಲು ಪ್ರತಿ ಪ್ರಕ್ರಿಯೆಯ ಸ್ಥಿರ ನಿಯಂತ್ರಣದಲ್ಲಿದೆ. ಜಾಲರಿಯ ಗಾತ್ರ, ಒತ್ತಡ ಮತ್ತು ಹಿಗ್ಗಿಸಲಾದ ಪರದೆಯ ಒತ್ತಡ, ತಲಾಧಾರದ ಮೇಲ್ಮೈ ಗುಣಲಕ್ಷಣಗಳು ಮತ್ತು ವೀಕ್ಷಣಾ ಪರಿಸ್ಥಿತಿಗಳ ಆಯ್ಕೆಯು ಬಣ್ಣ ವಿಚಲನದ ಮೇಲೆ ಒಂದು ನಿರ್ದಿಷ್ಟ ಪರಿಣಾಮವನ್ನು ಬೀರುತ್ತದೆ. ಆದಾಗ್ಯೂ, ನಿಖರವಾದ ಸೆಟ್ಟಿಂಗ್ ದಾಖಲೆಗಳು ಮತ್ತು ಪ್ರತಿ ಪ್ರಕ್ರಿಯೆಯ ಸ್ಥಿರ ನಿಯಂತ್ರಣವು ಸ್ಥಿರವಾದ ಪರದೆಯ ಮುದ್ರಣ ಬಣ್ಣಗಳನ್ನು ಖಾತ್ರಿಪಡಿಸುವ ಕೀಲಿಗಳಾಗಿವೆ.
ಪೋಸ್ಟ್ ಸಮಯ: ಜನವರಿ-08-2024