스크린 인쇄에서 색상 경향성이 나타나는 이유는 무엇입니까? 여러 색상의 혼합을 제쳐두고 한 가지 색상만 고려한다면, 색조의 원인을 논의하는 것이 더 간단할 수 있습니다. 이 문서에서는 스크린 인쇄의 색상 편차에 영향을 미치는 몇 가지 요소를 공유합니다. 해당 내용은 Youpin 포장재 시스템을 구매하고 공급하는 친구가 참조할 수 있는 것입니다.
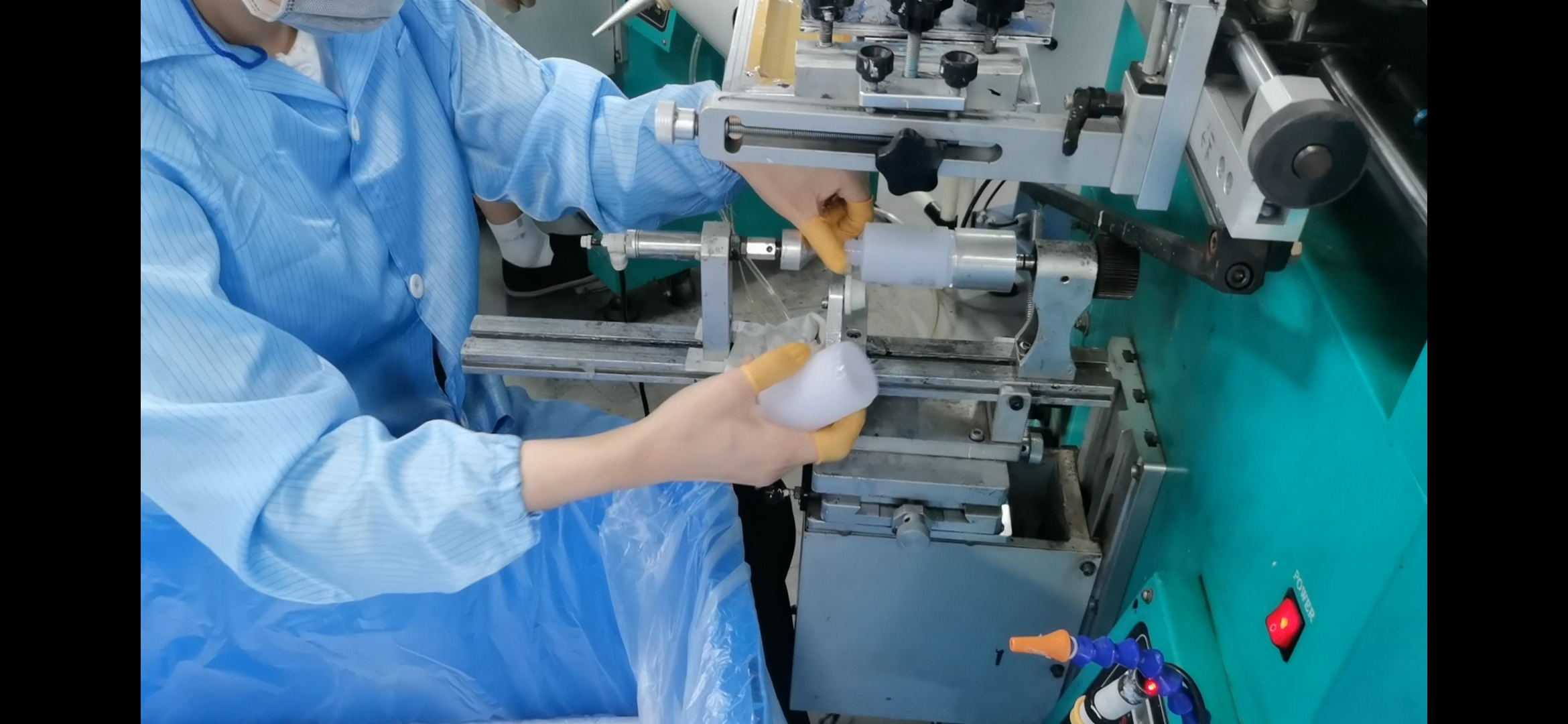
스크린 인쇄에서 색상 경향성이 나타나는 이유는 무엇입니까? 여러 색상의 혼합을 제쳐두고 한 가지 색상만 고려한다면, 색조의 원인을 논의하는 것이 더 간단할 수 있습니다. 이 문서에서는 스크린 인쇄의 색상 편차에 영향을 미치는 몇 가지 요소를 공유합니다. 해당 내용은 Youpin 포장재 시스템을 구매하고 공급하는 친구가 참조할 수 있는 것입니다.
다음은 스크린 인쇄에서 색상 편차를 유발하는 가장 일반적인 요소 중 일부입니다: 잉크 준비, 메시 선택, 메시 장력, 압력, 건조, 인쇄물 특성, 관찰 조건 등.
01 잉크 준비
잉크 혼합 사용된 잉크의 안료를 표준안료라고 가정할 때 색편차의 가장 큰 원인은 잉크에 잉크 혼합유 등의 용제를 첨가하는 것입니다. 색상 조절 장비가 좋은 작업장에서는 제어 장비에 따라 잉크를 혼합할 수 있습니다. 그러나 대부분의 인쇄회사에서는 이러한 시설을 갖추는 것이 불가능합니다. 그들은 잉크를 섞을 때 장인의 경험에만 의존합니다.
일반적으로 잉크를 인쇄에 더 적합하게 만들기 위해 잉크 조정 오일이 첨가됩니다. 그러나 조정유를 잉크에 첨가하면 잉크의 안료 농도가 변하여 인쇄 중 잉크의 색상 특성이 변하게 됩니다. 또한, 잉크에 용제가 너무 많이 함유되어 있으면 건조 후 얇은 잉크막이 형성되어 색상의 밝기가 감소합니다.
잉크를 칠하기 전에 잉크가 희석되는 문제도 있습니다. 예를 들어, 잉크 가게의 작업자는 잉크를 혼합하거나 희석할 때 공식에 따라 판단을 내립니다. 이는 불가피한 색상 편차로 이어집니다. 며칠 전에 잉크가 혼합된 경우 좋은 잉크로 인쇄하면 이러한 상황으로 인한 색상 경향이 더 뚜렷해집니다. 따라서 컬러캐스트를 완전히 방지하는 것은 거의 불가능합니다.
02 메쉬 선택
화면의 메쉬 크기가 잉크 전달에 영향을 미치는 유일한 요소라고 생각하면 많은 문제에 직면하게 될 것입니다. 메쉬 직경과 주름도 잉크 전달에 영향을 미칩니다. 일반적으로 스크린의 잉크 구멍에 더 많은 잉크가 부착될수록 인쇄 과정에서 더 많은 잉크가 인쇄물에 전달됩니다.
각 메시에서 얼마나 많은 잉크가 전사될 수 있는지 미리 예측하기 위해 많은 스크린 공급업체에서는 각 메시의 이론적인 잉크 전사량(TIV)을 제공합니다. TIV는 화면의 잉크 전사량의 크기를 나타내는 매개변수이다. 이는 특정 인쇄 조건에서 각 메시에 의해 전송되는 잉크의 양을 나타냅니다. 단위는 단위 면적당 잉크의 양입니다.
인쇄 시 일관된 톤을 보장하려면 스크린의 메쉬 수를 변경하지 않고 유지하는 것만으로는 충분하지 않고 스크린의 직경과 물결 모양도 일정하게 유지해야 합니다. 화면의 매개변수를 변경하면 인쇄 중 잉크 필름의 두께가 변경되어 색상이 변경됩니다.
03 순장력
네트의 장력이 너무 약하면 필름이 벗겨지는 원인이 됩니다. 메쉬에 잉크가 너무 많이 남아 있으면 인쇄물이 더러워집니다.
이 문제는 스크린과 기판 사이의 거리를 늘리면 해결될 수 있습니다. 그러나 스크린과 인쇄물 사이의 거리를 늘리려면 압력을 높여야 하므로 더 많은 잉크가 인쇄물에 전달됩니다. 색상의 농도를 변경합니다. 가장 좋은 방법은 스트레치 네트의 장력을 균일하게 유지하여 색상의 일관성을 유지하는 것입니다.
04 압력 수준
적절한 압력 설정은 일관된 색상을 유지하는 데 중요하며 인쇄 과정에서 균일한 압력 수준을 보장하는 것이 중요합니다. 특히 대량의 반복적인 인쇄 작업에서는 더욱 그렇습니다.
압력에 있어서 가장 먼저 고려해야 할 것은 스퀴지의 경도입니다. 스퀴지의 경도가 작아 접촉률은 좋으나 내굴곡성은 좋지 않습니다. 경도가 너무 높으면 인쇄 중에 화면 마찰도 커져 인쇄 정확도에 영향을 미칩니다. 두 번째는 스퀴지의 각도와 스퀴지 속도입니다. 잉크 칼의 각도는 잉크 전사량에 큰 영향을 미칩니다. 잉크칼의 각도가 작을수록 잉크 전사량이 많아집니다. 잉크 나이프 속도가 너무 빠르면 잉크 채우기가 부족하고 인쇄가 불완전하여 인쇄 품질에 영향을 미칩니다.
인쇄 작업에 대한 올바른 압력 설정을 얻고 이를 정확하게 기록한 후에는 인쇄 프로세스 중에 이러한 설정을 올바르게 따르는 한 일관된 색상의 만족스러운 인쇄 제품을 얻을 수 있습니다.
05 드라이
때로는 인쇄 직후에는 색상이 일관되게 보이지만 완제품을 찾은 후에는 색상이 변경됩니다. 이는 건조 장비의 잘못된 설정으로 인해 발생하는 경우가 많습니다. 가장 흔한 원인은 건조기 온도를 너무 높게 설정하여 종이나 판지의 잉크 색상이 변하는 것입니다.
06 기판특성
스크린 인쇄 전문가가 종종 간과하는 한 가지 문제는 인쇄물의 표면 특성입니다. 종이, 판지, 플라스틱 등은 모두 일괄 생산되며 고품질 기판은 안정적이고 일관된 표면 특성을 보장할 수 있습니다. 그러나 이것은 사실이 아니다. 인쇄물 표면 특성의 작은 변화로 인해 인쇄 시 색상 편차가 발생할 수 있습니다. 인쇄 압력이 균일하고 각 공정이 올바르게 작동하더라도 인쇄물 표면 특성의 불일치로 인해 인쇄 시 색상 변화가 더 커집니다. 컬러 캐스트.
동일한 인쇄 장비를 사용하여 동일한 제품을 다른 인쇄물에 인쇄하는 경우 인쇄물의 표면 특성이 색상에 미치는 영향이 특히 뚜렷합니다. 고객은 창 광고를 플라스틱이나 기타 판지에 인쇄하도록 요구할 수 있습니다. 그리고 고객은 동일한 제품에 대해 일관된 색상을 요구할 수도 있습니다.
이와 같은 상황에서 유일한 해결책은 정확한 색상 측정을 수행하는 것입니다. 색 농도를 측정하려면 분광 광도계 또는 분광 농도계를 사용하십시오. 색상 변화가 있는 경우 농도계는 이를 명확하게 반영할 수 있으며, 다른 프로세스를 제어하여 이러한 색상 변화를 극복할 수 있습니다.
07 관찰조건
인간의 눈은 색상의 미묘한 변화에 매우 민감하며 조명 조건에서만 색상을 구별할 수 있습니다. 그렇기 때문에 반드시 동일한 조명 조건에서 색상을 비교해보세요. 그렇지 않으면 잉크 양이나 압력을 조정하면 더 많은 잉크가 생성됩니다. 대형 컬러 캐스트.
결국, 일관된 색상을 유지하는 열쇠는 각 공정을 안정적으로 제어하여 잉크의 안정적인 성능을 보장하는 데 있습니다. 메쉬 크기 선택, 스트레치 스크린의 장력 및 압력, 기판의 표면 특성 및 관찰 조건은 모두 색상 편차에 일정한 영향을 미칩니다. 그러나 일관된 스크린 인쇄 색상을 보장하려면 정확한 설정 기록과 각 프로세스의 안정적인 제어가 중요합니다.
게시 시간: 2024년 1월 8일