- AS
1. AS аткаруу
AS пропилен-стирол сополимери, ошондой эле SAN деп аталат, тыгыздыгы болжол менен 1,07 г/см3. Бул ички стресс крекингге жакын эмес. Ал PSге караганда ачык-айкындуулукка, жумшартуу температурасына жана таасири күчтүүлүгүнө жана чарчоого каршылык көрсөтүүгө ээ.
2. AS колдонуу
Табалар, чөйчөктөр, идиш-аяктар, муздаткыч камералары, туткалары, жарык берүүчү аксессуарлар, жасалгалар, приборлордун күзгүлөрү, таңгак кутулары, кеңсе буюмдары, газ зажигалкалары, тиш щеткасынын кармагычтары ж.б.
3. AS иштетүү шарттары
AS иштетүү температурасы жалпысынан 210 ~ 250 ℃ болуп саналат. Бул материал нымдуулукка оңой сиңет жана кайра иштетүүдөн мурун бир сааттан ашык кургатуу керек. Анын суюктугу PSге караганда бир аз начар, ошондуктан инъекциялык басым дагы бир аз жогору, көктүн температурасы 45 ~ 75 ℃ жакшыраак көзөмөлдөнөт.
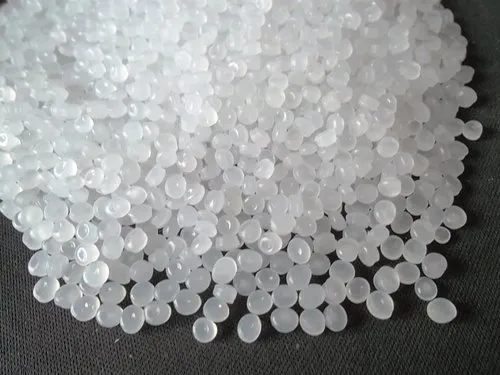
- ABS
1. ABS көрсөткүчү
ABS акрилонитрил-бутадиен-стирол терполимери. Бул болжол менен 1,05 г/см3 тыгыздыгы менен аморфтук полимер. Ал жогорку механикалык күчкө жана "тик, катуу жана болоттун" жакшы комплекстүү касиеттерине ээ. ABS ар кандай сорттору жана кеңири колдонулушу менен кеңири колдонулган инженердик пластик. Ал ошондой эле "жалпы инженердик пластик" деп аталат (MBS ачык ABS деп аталат). Аны калыптандыруу жана иштетүү оңой, химиялык туруктуулугу начар, буюмдарды электропластикалоо оңой.
2. ABS колдонуу
Насостун дөңгөлөктөрү, подшипниктери, туткалары, түтүктөр, электр приборлорунун корпустары, электрондук буюмдардын тетиктери, оюнчуктар, сааттын кутулары, приборлордун кутулары, суу резервуарынын корпустары, муздаткычтын жана муздаткычтын ички корпустары.
3. ABS процессинин мүнөздөмөлөрү
(1) ABS жогорку гигроскопиялык жана начар температурага каршылык бар. 0,03% дан төмөн нымдуулукту көзөмөлдөө үчүн калыпка салуу жана иштетүү алдында аны толугу менен кургатуу жана алдын ала ысытуу керек.
(2) ABS чайырынын эрүү илешкектүүлүгү температурага анча сезгич эмес (башка аморфтук чайырлардан айырмаланат). ABS инъекциясынын температурасы PSге караганда бир аз жогору болсо да, ал PS сыяктуу эркин температуранын көтөрүлүү диапазонуна ээ эмес жана сокур жылытуу колдонулбайт. Анын илешкектүүлүгүн азайтуу үчүн, сиз бурама ылдамдыгын жогорулата аласыз же анын суюктугун жакшыртуу үчүн инъекциянын басымын/ ылдамдыгын жогорулата аласыз. Жалпы иштетүү температурасы 190 ~ 235 ℃ болуп саналат.
(3) ABS эритмесинин илешкектүүлүгү орто, PS, HIPS жана AS ге караганда жогору жана анын суюктугу начар, ошондуктан инъекциянын жогорку басымы талап кылынат.
(4) ABS орто жана орто сайынуу ылдамдыгы менен жакшы таасир этет (эгер татаал формалар жана ичке бөлүктөрү жогорку инъекция ылдамдыгын талап кылбаса), буюмдун соплолору аба белгилерине жакын болот.
(5) ABS калыптоо температурасы салыштырмалуу жогору, анын көк температурасы жалпысынан 45 жана 80 ° C ортосунда жөнгө салынат. Чоңураак буюмдарды өндүрүүдө, туруктуу калыптын (алдыңкы калыптын) температурасы кыймылдуу калыпка (арткы калыпка) караганда болжол менен 5°C жогору болот.
(6) ABS жогорку температурадагы бочкада көпкө турбашы керек (30 мүнөттөн аз болушу керек), антпесе ал оңой чирип, саргайып кетет.
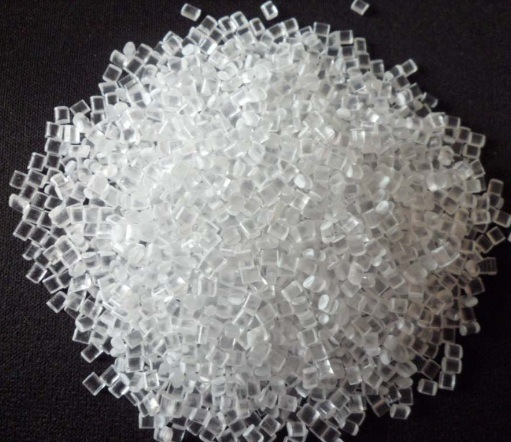
- PMMA
1. PMMA аткаруу
PMMA аморфтук полимер, адатта plexiglass (суб-акрил) катары белгилүү, тыгыздыгы болжол менен 1,18 г/см3. Ал сонун тунуктукка жана 92% жарык өткөрүмдүүлүккө ээ. Бул жакшы оптикалык материал болуп саналат; ал жакшы жылуулук каршылык (жылуулук каршылык) бар. деформация температурасы 98°С). Анын продуктусу орточо механикалык күчкө жана аз беттик катуулугуна ээ. Катуу нерселерден оңой чийилип, из калтырат. PS менен салыштырганда, морт болуу оңой эмес.
2. PMMA колдонуу
Аспаптык линзалар, оптикалык буюмдар, электр приборлору, медициналык жабдуулар, тунук моделдер, жасалгалар, күндөн коргоочу линзалар, протездер, билборддор, саат панелдери, унаанын арткы чырактары, алдыңкы айнектер ж.б.
3. PMMA процессинин мүнөздөмөлөрү
PMMA иштетүү талаптары катуу. Ал нымдуулукка жана температурага өтө сезгич. Аны иштетүүдөн мурун толук кургатуу керек. Анын эритме илешкектүүлүгү салыштырмалуу жогору, ошондуктан аны жогорку температурада (219 ~ 240 ℃) жана басымда калыптандыруу керек. Көктүн температурасы 65 ~ 80 ℃ ортосунда болсо жакшыраак. PMMA жылуулук туруктуулугу абдан жакшы эмес. Ал жогорку температурада бузулат же өтө көп убакыт бою жогору температурада калат. Бурама ылдамдыгы өтө жогору болбошу керек (болжол менен 60 rpm), анткени ал коюу PMMA бөлүктөрүндө оңой болот. "Боштук" феномени иштетүү үчүн чоң дарбазаларды жана "материалдык жогорку температура, көктүн жогорку температурасы, жай ылдамдык" инъекция шарттарын талап кылат.
4. Акрил (PMMA) деген эмне?
Акрил (PMMA) тунук, катуу пластмасса, көбүнчө сынбаган терезелер, жарык берүүчү белгилер, жарыктар жана учактын чатырлары сыяктуу буюмдарда айнек ордуна колдонулат. PMMA акрил чайырларынын маанилүү үй-бүлөсүнө кирет. Акрилдин химиялык аты - полиметилметакрилат (PMMA), ал метилметакрилаттан полимерленген синтетикалык чайыр.
Полиметилметакрилат (PMMA) ошондой эле акрил, акрил айнек катары белгилүү жана башкалардын арасында Crylux, Plexiglas, Acrylite, Perclax, Astariglas, Lucite жана Perspex сыяктуу соода аталыштары жана бренддери астында жеткиликтүү. Полиметилметакрилат (PMMA) көбүнчө айнекке жеңил же сынбаган альтернатива катары барак түрүндө колдонулат. PMMA ошондой эле куюу чайыр, сыя жана каптоо катары колдонулат. PMMA инженердик пластикалык материалдар тобунун бир бөлүгү болуп саналат.
5. Акрил кантип жасалат?
Полиметилметакрилат синтетикалык полимерлердин бири болгондуктан, полимерлөө жолу менен жасалат. Биринчиден, метилметакрилат калыпка салынып, процессти тездетүү үчүн катализатор кошулат. Бул полимерлөө процессинин аркасында PMMA барактар, чайырлар, блоктор жана шурулар сыяктуу ар кандай формада түзүлүшү мүмкүн. Акрил клей да PMMA бөлүктөрүн жумшартып, аларды ширетүүгө жардам берет.
PMMA ар кандай жолдор менен манипуляциялоо оңой. Анын касиеттерин жогорулатууга жардам берүү үчүн башка материалдар менен байланыштырылышы мүмкүн. Термоформалоодо ал ысыганда ийкемдүү болуп, муздаганда катып калат. Бул араа же лазер кесүү аркылуу тиешелүү өлчөмдө болушу мүмкүн. Эгерде жылтыратылган болсо, сиз бетиндеги чийиктерди жок кылып, анын бүтүндүгүн сактоого жардам бере аласыз.
6. Акрилдин кандай түрлөрү бар?
Акрил пластиктин эки негизги түрү акрил жана экструдиялык акрил болуп саналат. Куюлган акрилди өндүрүү кымбатыраак, бирок экструдиялык акрилге караганда күчтүүлүгү, бышыктыгы, тунуктугу, термоформалоо диапазону жана туруктуулугу бар. Акрилди куюу эң сонун химиялык туруктуулукту жана туруктуулукту сунуштайт, ошондой эле өндүрүш процессинде түстүү жана калыптандыруу оңой. Акрил куюлган ар кандай жоондукта да бар. Экструдирленген акрил куюлган акрилге караганда үнөмдүү жана куюлган акрилге караганда көбүрөөк ырааттуу, ишке жарамдуу акрилди камсыз кылат (күчтүн төмөндөшүнүн эсебинен). Экструдцияланган акрилди иштетүү жана иштетүү оңой, бул тиркемелерде айнек барактарына эң сонун альтернатива болуп саналат.
7. Эмне үчүн акрил мынчалык көп колдонулат?
Акрил көп колдонулат, анткени ал айнек сыяктуу эле пайдалуу сапаттарга ээ, бирок морттук маселеси жок. Акрил айнек мыкты оптикалык касиеттерге ээ жана катуу абалда айнек сыяктуу сынуу көрсөткүчүнө ээ. Анын сынбай турган касиеттеринен улам дизайнерлер акрилди айнек өтө кооптуу же болбосо иштебей кала турган жерлерде (мисалы, суу астындагы перископтор, учак терезелери ж.б.) колдоно алышат. Мисалы, ок өтпөс айнектин эң кеңири таралган түрү бул катуу акрил деп аталган 1/4 дюймдук калың акрил бөлүгү. Акрил ошондой эле инъекциялык формада жакшы иштейт жана калыпты жасоочу түзө турган дээрлик бардык формада түзүлүшү мүмкүн. Акрил айнектин күчү аны кайра иштетүү жана иштетүү оңойлугу менен айкалышып, аны эң сонун материалга айлантат, бул эмне үчүн ал керектөө жана соода тармактарында кеңири колдонулуп жатканын түшүндүрөт.
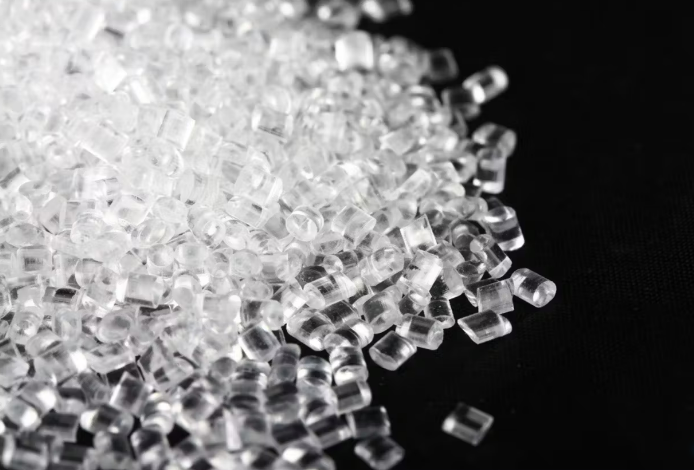
Посттун убактысы: 2023-жылдын 13-декабрына чейин