എന്തുകൊണ്ടാണ് സ്ക്രീൻ പ്രിൻ്റിംഗ് കളർ കാസ്റ്റുകൾ ഉണ്ടാക്കുന്നത്? ഞങ്ങൾ പല നിറങ്ങളുടെ മിശ്രിതം മാറ്റിവെച്ച് ഒരു നിറം മാത്രം പരിഗണിക്കുകയാണെങ്കിൽ, കളർ കാസ്റ്റിൻ്റെ കാരണങ്ങൾ ചർച്ച ചെയ്യുന്നത് എളുപ്പമായിരിക്കും. സ്ക്രീൻ പ്രിൻ്റിംഗിലെ വർണ്ണ വ്യതിയാനത്തെ ബാധിക്കുന്ന നിരവധി ഘടകങ്ങൾ ഈ ലേഖനം പങ്കിടുന്നു. Youpin പാക്കേജിംഗ് മെറ്റീരിയൽ സിസ്റ്റം വാങ്ങുകയും വിതരണം ചെയ്യുകയും ചെയ്യുന്ന സുഹൃത്തുക്കളുടെ റഫറൻസിനാണ് ഉള്ളടക്കം:
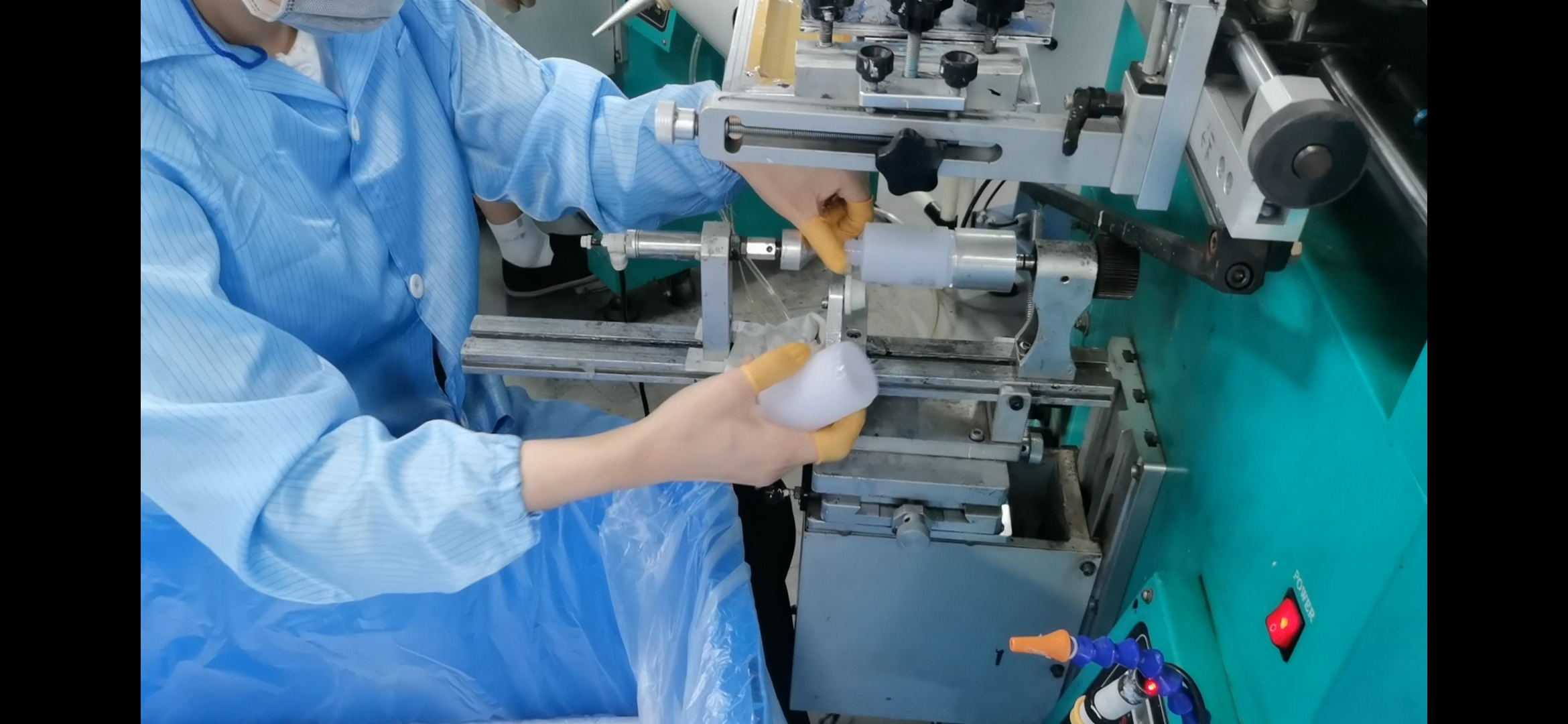
എന്തുകൊണ്ടാണ് സ്ക്രീൻ പ്രിൻ്റിംഗ് കളർ കാസ്റ്റുകൾ ഉണ്ടാക്കുന്നത്? ഞങ്ങൾ പല നിറങ്ങളുടെ മിശ്രിതം മാറ്റിവെച്ച് ഒരു നിറം മാത്രം പരിഗണിക്കുകയാണെങ്കിൽ, കളർ കാസ്റ്റിൻ്റെ കാരണങ്ങൾ ചർച്ച ചെയ്യുന്നത് എളുപ്പമായിരിക്കും. സ്ക്രീൻ പ്രിൻ്റിംഗിലെ വർണ്ണ വ്യതിയാനത്തെ ബാധിക്കുന്ന നിരവധി ഘടകങ്ങൾ ഈ ലേഖനം പങ്കിടുന്നു. Youpin പാക്കേജിംഗ് മെറ്റീരിയൽ സിസ്റ്റം വാങ്ങുകയും വിതരണം ചെയ്യുകയും ചെയ്യുന്ന സുഹൃത്തുക്കളുടെ റഫറൻസിനാണ് ഉള്ളടക്കം:
സ്ക്രീൻ പ്രിൻ്റിംഗിൽ വർണ്ണ വ്യതിയാനത്തിന് കാരണമാകുന്ന ഏറ്റവും സാധാരണമായ ചില ഘടകങ്ങൾ ചുവടെ പട്ടികപ്പെടുത്തിയിരിക്കുന്നു: മഷി തയ്യാറാക്കൽ, മെഷ് തിരഞ്ഞെടുക്കൽ, മെഷ് ടെൻഷൻ, മർദ്ദം, ഉണക്കൽ, അടിവസ്ത്ര സവിശേഷതകൾ, നിരീക്ഷണ സാഹചര്യങ്ങൾ മുതലായവ.
01 മഷി തയ്യാറാക്കൽ
മഷി മിശ്രിതം ഉപയോഗിക്കുന്ന മഷിയുടെ പിഗ്മെൻ്റ് ഒരു സാധാരണ പിഗ്മെൻ്റ് ആണെന്ന് കരുതിയാൽ, നിറവ്യത്യാസത്തിൻ്റെ ഏറ്റവും വലിയ കാരണം മഷി കലർത്തുന്ന എണ്ണ പോലുള്ള ലായകങ്ങൾ മഷിയിൽ ചേർക്കുന്നതാണ്. നല്ല കളർ കൺട്രോൾ ഉപകരണങ്ങളുള്ള ഒരു വർക്ക് ഷോപ്പിൽ, നിയന്ത്രണ ഉപകരണങ്ങൾ അനുസരിച്ച് മഷി കലർത്താം. എന്നിരുന്നാലും, മിക്ക പ്രിൻ്റിംഗ് കമ്പനികൾക്കും ഈ സൗകര്യങ്ങൾ ഉണ്ടാകുന്നത് അസാധ്യമാണ്. മഷി കലർത്തുമ്പോൾ അവർ യജമാന തൊഴിലാളികളുടെ അനുഭവത്തെ മാത്രം ആശ്രയിക്കുന്നു.
സാധാരണയായി, അച്ചടിക്കുന്നതിന് മഷി കൂടുതൽ അനുയോജ്യമാക്കുന്നതിന് മഷി ക്രമീകരിക്കുന്ന എണ്ണ ചേർക്കുന്നു. എന്നിരുന്നാലും, അഡ്ജസ്റ്റ് ചെയ്യുന്ന എണ്ണ മഷിയിൽ ചേർത്തുകഴിഞ്ഞാൽ, മഷിയിലെ പിഗ്മെൻ്റുകളുടെ സാന്ദ്രത മാറും, ഇത് പ്രിൻ്റിംഗ് സമയത്ത് മഷിയുടെ വർണ്ണ സവിശേഷതകളിൽ മാറ്റങ്ങൾ വരുത്തും. കൂടാതെ, മഷിയിലെ അധിക ലായകങ്ങൾ ഉണങ്ങിയതിനുശേഷം മഷിയുടെ നേർത്ത ഫിലിം ഉണ്ടാക്കും, ഇത് നിറത്തിൻ്റെ തെളിച്ചം കുറയ്ക്കും.
മഷിയിടുന്നതിന് മുമ്പ് മഷി നേർപ്പിച്ച പ്രശ്നവുമുണ്ട്. ഉദാഹരണത്തിന്, മഷി കടയിലെ തൊഴിലാളികൾ മഷി കലർത്തുമ്പോഴോ നേർപ്പിക്കുമ്പോഴോ അവരുടെ ഫോർമുലയെ അടിസ്ഥാനമാക്കി വിലയിരുത്തലുകൾ നടത്തുന്നു. ഇത് അനിവാര്യമായ വർണ്ണ വ്യതിയാനത്തിലേക്ക് നയിക്കുന്നു. കുറച്ച് ദിവസം മുമ്പ് മഷി കലർന്നതാണെങ്കിൽ, നിങ്ങൾ നല്ല മഷി ഉപയോഗിച്ച് പ്രിൻ്റ് ചെയ്താൽ, ഈ സാഹചര്യം മൂലമുണ്ടാകുന്ന നിറം കൂടുതൽ വ്യക്തമാകും. അതിനാൽ, കളർ കാസ്റ്റ് പൂർണ്ണമായും ഒഴിവാക്കുന്നത് മിക്കവാറും അസാധ്യമാണ്.
02 മെഷ് തിരഞ്ഞെടുക്കൽ
സ്ക്രീനിൻ്റെ മെഷ് വലുപ്പം മാത്രമാണ് മഷി കൈമാറ്റത്തെ ബാധിക്കുന്ന ഘടകം എന്ന് നിങ്ങൾ കരുതുന്നുവെങ്കിൽ, നിങ്ങൾക്ക് വളരെയധികം പ്രശ്നങ്ങൾ നേരിടേണ്ടിവരും. മെഷ് വ്യാസവും ചുളിവുകളും മഷി കൈമാറ്റത്തെ ബാധിക്കുന്നു. സാധാരണയായി, സ്ക്രീനിലെ മഷി ദ്വാരങ്ങളിൽ കൂടുതൽ മഷി ഘടിപ്പിച്ചാൽ, പ്രിൻ്റിംഗ് പ്രക്രിയയിൽ കൂടുതൽ മഷി അടിവസ്ത്രത്തിലേക്ക് മാറ്റപ്പെടും.
ഓരോ മെഷിനും എത്ര മഷി കൈമാറ്റം ചെയ്യാമെന്ന് മുൻകൂട്ടി കണക്കാക്കാൻ, പല സ്ക്രീൻ വിതരണക്കാരും ഓരോ മെഷിൻ്റെയും സൈദ്ധാന്തിക മഷി ട്രാൻസ്ഫർ വോളിയം (TIV) നൽകുന്നു. സ്ക്രീനിൻ്റെ മഷി ട്രാൻസ്ഫർ തുകയുടെ വലിപ്പം സൂചിപ്പിക്കുന്ന ഒരു പരാമീറ്ററാണ് TIV. നിർദ്ദിഷ്ട പ്രിൻ്റിംഗ് സാഹചര്യങ്ങളിൽ ഓരോ മെഷും എത്രമാത്രം മഷി കൈമാറ്റം ചെയ്യപ്പെടും എന്നത് ഒരു നിശ്ചിത രൂപത്തിൽ കൈമാറ്റം ചെയ്യപ്പെടുന്ന മഷിയുടെ അളവിനെ സൂചിപ്പിക്കുന്നു. ഒരു യൂണിറ്റ് ഏരിയയിലെ മഷിയുടെ അളവാണ് ഇതിൻ്റെ യൂണിറ്റ്.
പ്രിൻ്റിംഗിൽ സ്ഥിരതയുള്ള ടോണുകൾ ഉറപ്പാക്കാൻ, സ്ക്രീനിൻ്റെ മെഷ് നമ്പർ മാറ്റമില്ലാതെ നിലനിർത്താൻ പര്യാപ്തമല്ല, മാത്രമല്ല സ്ക്രീനിൻ്റെ വ്യാസവും അതിൻ്റെ തരംഗവും സ്ഥിരമായി തുടരുന്നുവെന്ന് ഉറപ്പാക്കുകയും വേണം. സ്ക്രീനിലെ ഏതെങ്കിലും പാരാമീറ്ററിലെ മാറ്റങ്ങൾ പ്രിൻ്റിംഗ് സമയത്ത് മഷി ഫിലിമിൻ്റെ കനം മാറുന്നതിന് കാരണമാകും, അതിൻ്റെ ഫലമായി നിറം മാറും.
03 നെറ്റ് ടെൻഷൻ
നെറ്റിൻ്റെ പിരിമുറുക്കം തീരെ കുറവാണെങ്കിൽ, അത് ഫിലിം പൊളിക്കാൻ ഇടയാക്കും. മെഷിൽ വളരെയധികം മഷി തങ്ങിനിൽക്കുകയാണെങ്കിൽ, അച്ചടിച്ച വസ്തുക്കൾ വൃത്തികെട്ടതായിത്തീരും.
സ്ക്രീനും സബ്സ്ട്രേറ്റും തമ്മിലുള്ള ദൂരം വർദ്ധിപ്പിച്ച് ഈ പ്രശ്നം പരിഹരിക്കാൻ കഴിയും. എന്നിരുന്നാലും, സ്ക്രീനും സബ്സ്ട്രേറ്റും തമ്മിലുള്ള ദൂരം വർദ്ധിപ്പിക്കുന്നതിന് മർദ്ദം വർദ്ധിപ്പിക്കേണ്ടതുണ്ട്, ഇത് കൂടുതൽ മഷി അടിവസ്ത്രത്തിലേക്ക് മാറ്റാൻ ഇടയാക്കും. നിറത്തിൻ്റെ സാന്ദ്രത മാറ്റാൻ. സ്ട്രെച്ച് നെറ്റിൻ്റെ പിരിമുറുക്കം ഏകീകൃതമായി നിലനിർത്തുക എന്നതാണ് ഏറ്റവും നല്ല മാർഗം, അങ്ങനെ നിറത്തിൻ്റെ സ്ഥിരത ഉറപ്പാക്കുക.
04 സമ്മർദ്ദ നില
സ്ഥിരമായ നിറം നിലനിർത്തുന്നതിന് ശരിയായ മർദ്ദം ക്രമീകരണം നിർണായകമാണ്, കൂടാതെ പ്രിൻ്റിംഗ് പ്രക്രിയയിൽ ഏകീകൃത മർദ്ദം ഉറപ്പാക്കുന്നത് നിർണായകമാണ്. പ്രത്യേകിച്ചും ഉയർന്ന അളവിലുള്ള, ആവർത്തിച്ചുള്ള പ്രിൻ്റിംഗ് ജോലികളിൽ.
സമ്മർദത്തിൻ്റെ കാര്യം വരുമ്പോൾ, ആദ്യം പരിഗണിക്കേണ്ടത് സ്ക്വീജിയുടെ കാഠിന്യമാണ്. സ്ക്വീജിയുടെ കാഠിന്യം ചെറുതാണ്, ഇത് കോൺടാക്റ്റ് നിരക്കിന് നല്ലതാണ്, പക്ഷേ ഇത് വളയുന്ന പ്രതിരോധത്തിന് നല്ലതല്ല. കാഠിന്യം വളരെ കൂടുതലാണെങ്കിൽ, പ്രിൻ്റിംഗ് സമയത്ത് സ്ക്രീനിലെ ഘർഷണവും വലുതായിരിക്കും, അങ്ങനെ പ്രിൻ്റിംഗ് കൃത്യതയെ ബാധിക്കും. രണ്ടാമത്തേത് സ്ക്വീജിയുടെ കോണും സ്ക്വീജി വേഗതയുമാണ്. മഷി കത്തിയുടെ ആംഗിൾ മഷി കൈമാറ്റത്തിൻ്റെ അളവിൽ കാര്യമായ സ്വാധീനം ചെലുത്തുന്നു. മഷി കത്തിയുടെ ആംഗിൾ ചെറുതാണെങ്കിൽ, മഷി കൈമാറ്റത്തിൻ്റെ അളവ് വർദ്ധിക്കും. മഷി കത്തിയുടെ വേഗത വളരെ വേഗത്തിലാണെങ്കിൽ, അത് മതിയായ മഷി നിറയ്ക്കുന്നതിനും അപൂർണ്ണമായ മുദ്ര പതിപ്പിക്കുന്നതിനും കാരണമാകും, അങ്ങനെ പ്രിൻ്റിൻ്റെ ഗുണനിലവാരത്തെ ബാധിക്കും.
ഒരു പ്രിൻ്റ് ജോലിക്കുള്ള ശരിയായ പ്രഷർ ക്രമീകരണങ്ങൾ നിങ്ങൾ നേടിയ ശേഷം അവ കൃത്യമായി രേഖപ്പെടുത്തിക്കഴിഞ്ഞാൽ, പ്രിൻ്റിംഗ് പ്രക്രിയയിൽ നിങ്ങൾ ഈ ക്രമീകരണങ്ങൾ കൃത്യമായി പിന്തുടരുന്നിടത്തോളം, സ്ഥിരമായ നിറങ്ങളുള്ള തൃപ്തികരമായ പ്രിൻ്റ് ഉൽപ്പന്നം നിങ്ങൾക്ക് ലഭിക്കും.
05 വരണ്ട
ചിലപ്പോൾ, പ്രിൻ്റ് ചെയ്തതിന് ശേഷം നിറം സ്ഥിരമായി കാണപ്പെടുന്നു, പക്ഷേ പൂർത്തിയായ ഉൽപ്പന്നം കണ്ടെത്തിയതിന് ശേഷം നിറം മാറുന്നു. ഉണക്കൽ ഉപകരണങ്ങളുടെ തെറ്റായ ക്രമീകരണം മൂലമാണ് ഇത് പലപ്പോഴും സംഭവിക്കുന്നത്. ഏറ്റവും സാധാരണമായ കാരണം, ഡ്രയർ താപനില വളരെ ഉയർന്നതാണ്, ഇത് പേപ്പറിലോ കാർഡ്ബോർഡിലോ മഷി നിറം മാറുന്നതിന് കാരണമാകുന്നു.
06 സബ്സ്ട്രേറ്റ് സവിശേഷതകൾ
സ്ക്രീൻ പ്രിൻ്റിംഗ് മാസ്റ്റർമാർ പലപ്പോഴും അവഗണിക്കുന്ന ഒരു പ്രശ്നം അടിവസ്ത്രത്തിൻ്റെ ഉപരിതല ഗുണങ്ങളാണ്. പേപ്പർ, കാർഡ്ബോർഡ്, പ്ലാസ്റ്റിക് തുടങ്ങിയവയെല്ലാം ബാച്ചുകളിൽ ഉൽപ്പാദിപ്പിക്കപ്പെടുന്നു, ഉയർന്ന നിലവാരമുള്ള അടിവസ്ത്രങ്ങൾക്ക് സുസ്ഥിരവും സുസ്ഥിരവുമായ ഉപരിതല ഗുണങ്ങൾ ഉറപ്പാക്കാൻ കഴിയും. എന്നാൽ ഇത് അങ്ങനെയല്ല. അടിവസ്ത്രത്തിൻ്റെ ഉപരിതല ഗുണങ്ങളിൽ ചെറിയ മാറ്റങ്ങൾ അച്ചടിയിൽ നിറവ്യത്യാസത്തിന് കാരണമാകും. പ്രിൻ്റിംഗ് മർദ്ദം ഏകതാനമാണെങ്കിലും ഓരോ പ്രക്രിയയും ശരിയായി പ്രവർത്തിക്കുന്നുണ്ടെങ്കിലും, അടിവസ്ത്രത്തിൻ്റെ ഉപരിതല ഗുണങ്ങളിലെ പൊരുത്തക്കേടുകൾ അച്ചടിയിൽ വലിയ വർണ്ണ ഷിഫ്റ്റുകൾക്ക് കാരണമാകും. കളർ കാസ്റ്റ്.
ഒരേ ഉൽപ്പന്നം ഒരേ പ്രിൻ്റിംഗ് ഉപകരണങ്ങൾ ഉപയോഗിച്ച് വ്യത്യസ്ത സബ്സ്ട്രേറ്റുകളിൽ അച്ചടിക്കുമ്പോൾ, അടിവസ്ത്രത്തിൻ്റെ ഉപരിതല ഗുണങ്ങളുടെ സ്വാധീനം വർണ്ണത്തിൽ പ്രത്യേകിച്ചും വ്യക്തമാണ്. ഉപഭോക്താക്കൾക്ക് വിൻഡോ പരസ്യങ്ങൾ പ്ലാസ്റ്റിക് അല്ലെങ്കിൽ മറ്റ് കാർഡ്ബോർഡിൽ പ്രിൻ്റ് ചെയ്യേണ്ടതായി വന്നേക്കാം. ക്ലയൻ്റുകൾക്ക് ഒരേ ഭാഗത്തിന് സ്ഥിരമായ നിറങ്ങൾ ആവശ്യമായി വന്നേക്കാം.
ഇത്തരം സന്ദർഭങ്ങളിൽ, കൃത്യമായ വർണ്ണ അളവുകൾ ഉണ്ടാക്കുക എന്നതാണ് ഏക പരിഹാരം. വർണ്ണ സാന്ദ്രത അളക്കാൻ ഒരു സ്പെക്ട്രോഫോട്ടോമീറ്റർ അല്ലെങ്കിൽ സ്പെക്ട്രൽ ഡെൻസിറ്റോമീറ്റർ ഉപയോഗിക്കുക. ഒരു കളർ ഷിഫ്റ്റ് ഉണ്ടെങ്കിൽ, ഡെൻസിറ്റോമീറ്ററിന് അത് വ്യക്തമായി പ്രതിഫലിപ്പിക്കാൻ കഴിയും, മറ്റ് പ്രക്രിയകൾ നിയന്ത്രിക്കുന്നതിലൂടെ നിങ്ങൾക്ക് ഈ വർണ്ണ ഷിഫ്റ്റിനെ മറികടക്കാൻ കഴിയും.
07 നിരീക്ഷണ വ്യവസ്ഥകൾ
മനുഷ്യൻ്റെ കണ്ണുകൾ നിറത്തിലെ സൂക്ഷ്മമായ മാറ്റങ്ങളോട് വളരെ സെൻസിറ്റീവ് ആണ്, കൂടാതെ പ്രകാശ സാഹചര്യങ്ങളിൽ മാത്രമേ നിറങ്ങൾ വേർതിരിച്ചറിയാൻ കഴിയൂ. ഇക്കാരണത്താൽ, ഒരേ ലൈറ്റിംഗ് സാഹചര്യങ്ങളിൽ നിറങ്ങൾ താരതമ്യം ചെയ്യുന്നത് ഉറപ്പാക്കുക. അല്ലെങ്കിൽ, മഷിയുടെ അളവ് അല്ലെങ്കിൽ മർദ്ദം ക്രമീകരിക്കുന്നത് കൂടുതൽ മഷി ഉണ്ടാക്കും. വലിയ കളർ കാസ്റ്റ്.
മൊത്തത്തിൽ, സ്ഥിരതയുള്ള നിറം നിലനിർത്തുന്നതിനുള്ള താക്കോൽ മഷിയുടെ സ്ഥിരതയുള്ള പ്രകടനം ഉറപ്പാക്കുന്നതിന് ഓരോ പ്രക്രിയയുടെയും സ്ഥിരമായ നിയന്ത്രണത്തിലാണ്. മെഷ് വലുപ്പം, സ്ട്രെച്ച് സ്ക്രീനിൻ്റെ പിരിമുറുക്കം, മർദ്ദം എന്നിവയുടെ തിരഞ്ഞെടുപ്പ്, അടിവസ്ത്രത്തിൻ്റെ ഉപരിതല സവിശേഷതകൾ, നിരീക്ഷണ സാഹചര്യങ്ങൾ എന്നിവയെല്ലാം വർണ്ണ വ്യതിയാനത്തിൽ ഒരു നിശ്ചിത സ്വാധീനം ചെലുത്തുന്നു. എന്നിരുന്നാലും, കൃത്യമായ ക്രമീകരണ റെക്കോർഡുകളും ഓരോ പ്രക്രിയയുടെയും സ്ഥിരമായ നിയന്ത്രണവും സ്ഥിരമായ സ്ക്രീൻ പ്രിൻ്റിംഗ് നിറങ്ങൾ ഉറപ്പാക്കുന്നതിനുള്ള താക്കോലാണ്.
പോസ്റ്റ് സമയം: ജനുവരി-08-2024