किन स्क्रिन प्रिन्टिङले रङ कास्टहरू उत्पादन गर्छ? यदि हामीले धेरै रङहरूको मिश्रणलाई एकै ठाउँमा राख्यौं र केवल एक रङलाई विचार गर्छौं भने, रङ कास्टको कारणहरू छलफल गर्न सजिलो हुन सक्छ। यो लेखले स्क्रिन प्रिन्टिङमा रंग विचलनलाई असर गर्ने धेरै कारकहरू साझा गर्दछ। सामग्री Youpin प्याकेजिङ सामग्री प्रणाली खरिद र आपूर्ति गर्ने साथीहरू द्वारा सन्दर्भको लागि हो:
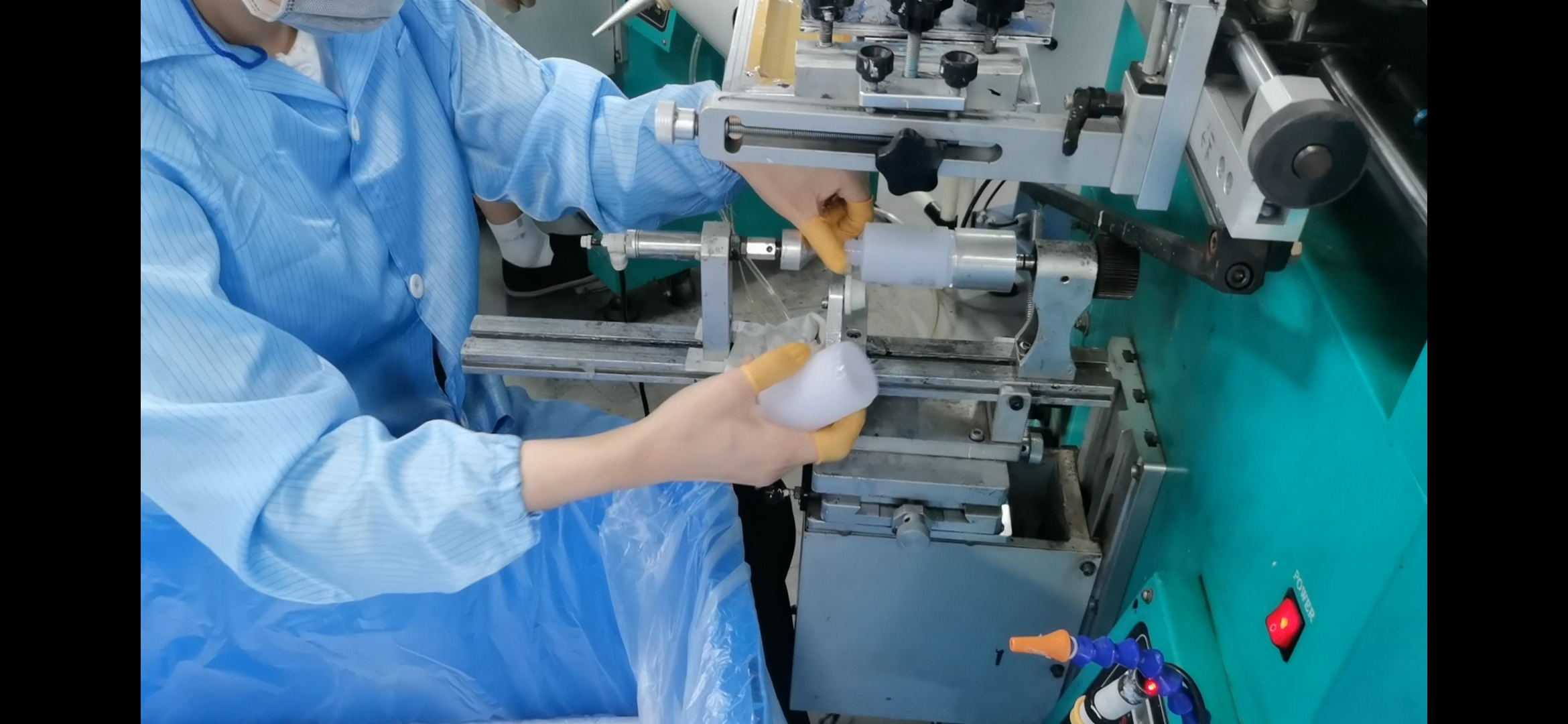
किन स्क्रिन प्रिन्टिङले रङ कास्टहरू उत्पादन गर्छ? यदि हामीले धेरै रङहरूको मिश्रणलाई एकै ठाउँमा राख्यौं र केवल एक रङलाई विचार गर्छौं भने, रङ कास्टको कारणहरू छलफल गर्न सजिलो हुन सक्छ। यो लेखले स्क्रिन प्रिन्टिङमा रंग विचलनलाई असर गर्ने धेरै कारकहरू साझा गर्दछ। सामग्री Youpin प्याकेजिङ सामग्री प्रणाली खरिद र आपूर्ति गर्ने साथीहरू द्वारा सन्दर्भको लागि हो:
तल सूचीबद्ध केहि सबैभन्दा सामान्य कारकहरू छन् जसले स्क्रिन प्रिन्टिङमा रंग विचलन निम्त्याउँछ: मसीको तयारी, जाल चयन, जाल तनाव, दबाब, सुकाउने, सब्सट्रेट विशेषताहरू, अवलोकन अवस्थाहरू, आदि।
01 मसी तयारी
मसीको मिश्रण प्रयोग गरिएको मसीको पिगमेन्ट मानक पिग्मेन्ट हो भनी मानेर, रङ विचलनको सबैभन्दा ठूलो कारण मसीमा मसी मिसाउने तेल जस्ता घोलकहरू थप्नु हो। राम्रो रंग नियन्त्रण उपकरण संग एक कार्यशाला मा, मसी नियन्त्रण उपकरण अनुसार मिलाउन सकिन्छ। तर, अधिकांश प्रिन्टिङ कम्पनीहरूका लागि यी सुविधाहरू हुनु असम्भव छ। तिनीहरू मसी मिसाउँदा मास्टर कार्यकर्ताहरूको अनुभवमा मात्र भर पर्छन्।
सामान्यतया, मसीलाई मुद्रणको लागि थप उपयुक्त बनाउन मसी समायोजन गर्ने तेल थपिन्छ। यद्यपि, एक पटक समायोजन गर्ने तेल मसीमा थपिएपछि, मसीमा रंगद्रव्यहरूको एकाग्रता परिवर्तन हुनेछ, जसले मुद्रणको समयमा मसीको रंग विशेषताहरूमा परिवर्तन ल्याउनेछ। थप रूपमा, मसीमा थप विलायक सुके पछि मसीको पातलो फिल्म बनाउँदछ, जसले रंगको चमक कम गर्दछ।
मसी लगाउनुअघि मसी पातलो हुने समस्या पनि छ । उदाहरणका लागि, मसी पसलमा कामदारहरूले मसी मिलाउँदा वा पातलो गर्दा तिनीहरूको सूत्रको आधारमा निर्णय गर्छन्। यसले अपरिहार्य रंग विचलन निम्त्याउँछ। यदि मसी केहि दिन पहिले मिसाइएको छ भने, यदि तपाइँ राम्रो मसीले छाप्नुहुन्छ भने, यो अवस्थाको कारण रंग कास्ट अधिक स्पष्ट हुनेछ। त्यसकारण, रंग कास्टलाई पूर्ण रूपमा बेवास्ता गर्न लगभग असम्भव छ।
02 मेष चयन
यदि तपाइँ सोच्नुहुन्छ कि स्क्रिनको जाल आकार एक मात्र कारक हो जसले मसी स्थानान्तरणलाई असर गर्छ, तपाइँले धेरै समस्याको सामना गर्नुहुनेछ। जाल व्यास र झुर्रियाँले पनि मसी स्थानान्तरणलाई असर गर्छ। सामान्यतया, स्क्रिनको मसी प्वालहरूमा जति धेरै मसी जोडिन्छ, मुद्रण प्रक्रियाको क्रममा सब्सट्रेटमा बढी मसी स्थानान्तरण हुनेछ।
प्रत्येक जालबाट कति मसी स्थानान्तरण गर्न सकिन्छ भनेर अग्रिम अनुमान गर्न, धेरै स्क्रिन आपूर्तिकर्ताहरूले प्रत्येक जालको सैद्धान्तिक मसी स्थानान्तरण भोल्युम (TIV) प्रदान गर्छन्। TIV एक प्यारामिटर हो जसले स्क्रिनको मसी स्थानान्तरण रकमको आकारलाई संकेत गर्दछ। यसले निश्चित प्रिन्टिङ सर्तहरूमा प्रत्येक जालले कति मसी स्थानान्तरण गर्नेछ भनेर निश्चित रूपमा हस्तान्तरण गरिएको मसीको मात्रालाई जनाउँछ। यसको एकाइ प्रति एकाइ क्षेत्र मसी को मात्रा हो।
प्रिन्टिङमा लगातार टोनहरू सुनिश्चित गर्न, स्क्रिनको जाल नम्बर अपरिवर्तित राख्न पर्याप्त छैन, तर स्क्रिनको व्यास र यसको लहरीपन स्थिर रहन्छ भनेर पनि सुनिश्चित गर्न। स्क्रिनको कुनै पनि प्यारामिटरमा परिवर्तनले मुद्रणको समयमा मसी फिलिमको मोटाईमा परिवर्तन ल्याउनेछ, जसको परिणामस्वरूप रंग परिवर्तन हुन्छ।
03 नेट तनाव
यदि नेटको तनाव धेरै सानो छ भने, यसले फिल्मलाई पिल गर्नको कारण बनाउँछ। यदि जालमा धेरै मसी रह्यो भने, छापिएको पदार्थ फोहोर हुनेछ।
यो समस्या स्क्रिन र सब्सट्रेट बीचको दूरी बढाएर हल गर्न सकिन्छ। यद्यपि, स्क्रिन र सब्सट्रेट बीचको दूरी बढाउनको लागि दबाब बढाउन आवश्यक छ, जसले सब्सट्रेटमा स्थानान्तरण गर्न थप मसी निम्त्याउँछ। रङको घनत्व परिवर्तन गर्न। सबै भन्दा राम्रो तरिका स्ट्रेच नेट एकसमानको तनाव राख्नु हो, ताकि रंगको स्थिरता सुनिश्चित गर्न।
04 दबाव स्तर
उचित दबाब सेटिङहरू एकरूप रंग कायम राख्न महत्त्वपूर्ण छन्, र मुद्रण प्रक्रियाको समयमा समान दबाव स्तरहरू सुनिश्चित गर्न महत्त्वपूर्ण छ। विशेष गरी उच्च मात्रा, दोहोरिने मुद्रण कार्यहरूमा।
जब यो दबाब को लागी आउँछ, विचार गर्न को लागी पहिलो कुरा squeegee को कठोरता हो। squeegee को कठोरता सानो छ, जो सम्पर्क दर को लागी राम्रो छ, तर यो झुकाउने प्रतिरोध को लागी राम्रो छैन। यदि कठोरता धेरै उच्च छ भने, मुद्रणको समयमा स्क्रिनमा घर्षण पनि ठूलो हुनेछ, यसैले मुद्रण शुद्धतालाई असर गर्छ। दोस्रो squeegee र squeegee गति को कोण हो। मसी चक्कु को कोण मसी स्थानान्तरण को मात्रा मा एक महत्वपूर्ण प्रभाव छ। मसी चक्कुको कोण जति सानो हुन्छ, मसी स्थानान्तरणको ठूलो मात्रा। यदि मसी चक्कुको गति धेरै छिटो छ भने, यसले अपर्याप्त मसी भर्ने र अपूर्ण छाप निम्त्याउनेछ, यसैले प्रिन्टको गुणस्तरलाई असर गर्छ।
एकचोटि तपाईंले मुद्रण कार्यको लागि सही दबाब सेटिङ्हरू प्राप्त गर्नुभयो र तिनीहरूलाई सही रूपमा रेकर्ड गर्नुभयो, जबसम्म तपाईंले मुद्रण प्रक्रियाको क्रममा यी सेटिङहरू सही रूपमा पालना गर्नुहुन्छ, तपाईंले सुसंगत रङहरूसँग सन्तोषजनक मुद्रण उत्पादन पाउनुहुनेछ।
05 सुक्खा
कहिलेकाहीँ, रंग मुद्रण पछि एकरूप देखिन्छ, तर समाप्त उत्पादन फेला परेपछि रङ परिवर्तन हुन्छ। यो अक्सर सुकाउने उपकरण को गलत सेटिंग्स को कारण हो। सबैभन्दा सामान्य कारण यो हो कि ड्रायरको तापमान धेरै उच्च सेट गरिएको छ, कागज वा कार्डबोर्डमा मसीको रंग परिवर्तन गर्नको लागि।
06 सब्सट्रेट विशेषताहरू
एउटा मुद्दा जुन स्क्रिन प्रिन्टिङ मास्टरहरूले प्रायः बेवास्ता गर्छन् सब्सट्रेटको सतह गुणहरू। कागज, गत्ता, प्लास्टिक, आदि सबै ब्याचहरूमा उत्पादन गरिन्छ, र उच्च-गुणस्तर सब्सट्रेटहरूले स्थिर र लगातार सतह गुणहरू सुनिश्चित गर्न सक्छन्। तर यो अवस्था छैन। सब्सट्रेटको सतह गुणहरूमा साना परिवर्तनहरूले मुद्रणमा रंग विचलन निम्त्याउँछ। यदि प्रिन्टिङ प्रेसर एकसमान छ र प्रत्येक प्रक्रिया सही रूपमा सञ्चालन गरिएको छ भने पनि, सब्सट्रेटको सतह गुणहरूमा विसंगतिहरूले मुद्रणमा ठूलो रङ परिवर्तनहरू निम्त्याउँछ। रङ कास्ट।
जब एउटै उत्पादन एउटै प्रिन्टिंग उपकरणको साथ विभिन्न सब्सट्रेटहरूमा छापिन्छ, रङमा सब्सट्रेटको सतह गुणहरूको प्रभाव विशेष गरी स्पष्ट हुन्छ। ग्राहकहरूलाई विन्डो विज्ञापनहरू प्लास्टिक वा अन्य कार्डबोर्डमा छाप्न आवश्यक पर्दछ। र ग्राहकहरूलाई एउटै टुक्राको लागि लगातार रङहरू आवश्यक पर्दछ।
यस्तो अवस्थामा, एकमात्र समाधान सही रंग मापन गर्न हो। रङको घनत्व नाप्न स्पेक्ट्रोफोटोमिटर वा स्पेक्ट्रल डेन्सिटोमिटर प्रयोग गर्नुहोस्। यदि त्यहाँ रंग परिवर्तन छ भने, डेन्सिटोमिटरले यसलाई स्पष्ट रूपमा प्रतिबिम्बित गर्न सक्छ, र तपाइँ अन्य प्रक्रियाहरू नियन्त्रण गरेर यो रङ परिवर्तनलाई जित्न सक्नुहुन्छ।
07 अवलोकन अवस्था
मानव आँखा रङमा सूक्ष्म परिवर्तनहरूप्रति धेरै संवेदनशील हुन्छन्, र प्रकाश अवस्थाहरूमा मात्र रङहरू छुट्याउन सक्छन्। यसको कारणले, एउटै प्रकाश अवस्था अन्तर्गत रंगहरू तुलना गर्न निश्चित गर्नुहोस्। अन्यथा, मसी भोल्युम वा दबाब समायोजनले थप मसी उत्पादन गर्नेछ। ठूलो रंग कास्ट।
सबैमा, मसीको स्थिर प्रदर्शन सुनिश्चित गर्न प्रत्येक प्रक्रियाको स्थिर नियन्त्रणमा लगातार रंग कायम राख्ने कुञ्जी निहित छ। जालको आकारको चयन, तनाव र स्ट्रेच स्क्रिनको दबाब, सब्सट्रेटको सतह विशेषताहरू र अवलोकन अवस्थाहरू सबैले रंग विचलनमा निश्चित प्रभाव पार्छ। यद्यपि, सटीक सेटिङ रेकर्डहरू र प्रत्येक प्रक्रियाको स्थिर नियन्त्रण लगातार स्क्रिन प्रिन्टिङ रङहरू सुनिश्चित गर्न कुञ्जीहरू हुन्।
पोस्ट समय: जनवरी-08-2024