With the rapid growth of the cosmetic packaging industry, there's an increasing demand for visually appealing packaging. Frosted bottles, known for their elegant appearance, have become a favorite among cosmetic packaging manufacturers and consumers, making them a key material in the market.
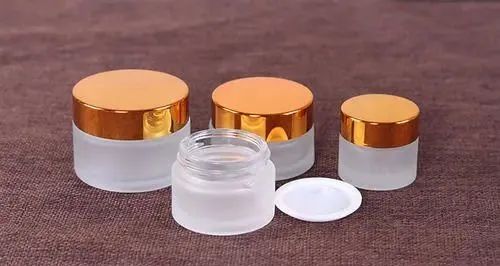
Frosting Process
Frosted glass is essentially etched with acid, similar to chemical etching and polishing. The difference lies in the removal process. While chemical polishing removes insoluble residues to achieve a smooth, transparent surface, frosting leaves these residues on the glass, creating a textured, semi-transparent surface that scatters light and gives a hazy appearance.
1. Frosting Characteristics
Frosting is a chemical etching process where insoluble particles adhere to the glass surface, creating a textured feel. The extent of etching varies, resulting in a rough or smooth finish depending on the crystal size and quantity on the surface.
2. Judging Frosting Quality
Scattering Rate: Higher scattering indicates better frosting.
Total Transmission Rate: Lower transmission rate implies greater frosting as more light is scattered rather than passing through.
Surface Appearance: This includes the size and distribution of etching residues, affecting both the transmission rate and the smoothness of the surface.
3. Frosting Methods and Materials
Methods:
Immersion: Dipping glass into the frosting solution.
Spraying: Spraying the solution onto the glass.
Coating: Applying frosting paste to the glass surface.
Materials:
Frosting Solution: Made from hydrofluoric acid and additives.
Frosting Powder: A mix of fluorides and additives, combined with sulfuric or hydrochloric acid to produce hydrofluoric acid.
Frosting Paste: A mix of fluorides and acids, forming a paste.
Note: Hydrofluoric acid, while effective, is not suitable for mass production due to its volatility and health hazards. Frosting paste and powder are safer and better for different methods.
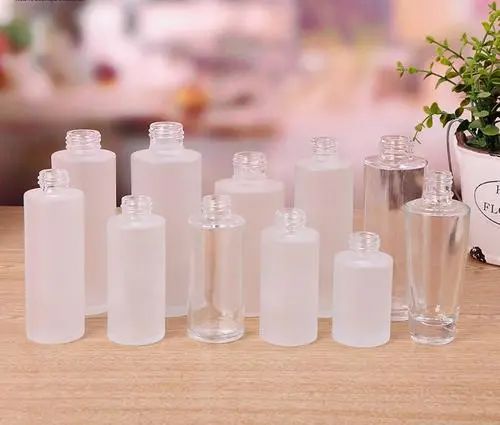
4. Frosted Glass vs. Sandblasted Glass
Sandblasted Glass: Uses high-speed sand to create a rough texture, producing a hazy effect. It's rougher to the touch and more prone to damage compared to frosted glass.
Frosted Glass: Created by chemical etching, resulting in a smooth, matte finish. Often used with silk screen printing for decorative purposes.
Etched Glass: Also known as matte or obscure glass, it diffuses light without being see-through, making it ideal for soft, non-glaring light.
5. Frosting Precautions
Use plastic or corrosion-resistant containers for the solution.
Wear rubber gloves to prevent skin burns.
Clean glass thoroughly before frosting.
Adjust acid quantity based on glass type, adding water before sulfuric acid.
Stir the solution before use and cover when not in use.
Add frosting powder and sulfuric acid as needed during use.
Neutralize waste water with quicklime before disposal.
6. Applications in the Cosmetic Industry
Frosted bottles are popular in cosmetic packaging for their luxurious look. The tiny frosted particles give the bottle a smooth feel and a jade-like shine. The stability of glass prevents chemical reactions between the product and the packaging, ensuring the quality of cosmetics.
Topfeel's newly launched PJ77 glass cream jar is not only perfectly compatible with the frosting process, giving the product a high-end texture, but also conforms to the environmental protection trend with its innovative interchangeable packaging design. Its built-in airless pump system ensures precise and smooth release of the contents with every gentle press, making the experience more elegant and convenient.
Post time: Jul-10-2024