Published on September 27, 2024 by Yidan Zhong
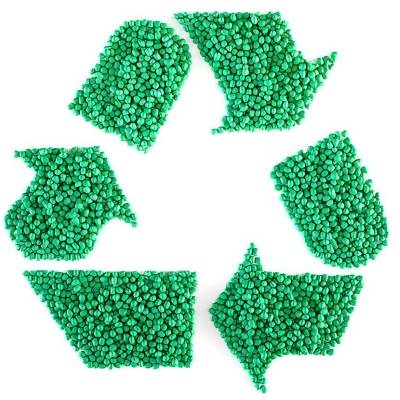
What are plastic additives?
Plastic additives are natural or synthetic inorganic or organic compounds that alter the characteristics of pure plastic or add new properties. Manufacturers mix resin with additive masterbatches in specific proportions based on the product's requirements, then produce various materials. After processing through casting, compression, molding, etc., the initial mixture takes the desired shape.
Mixing different additives with plastic granules can impart various properties to plastics, such as increased toughness, better insulation, and a glossy finish. Adding additives to plastics not only makes plastic objects lighter but also improves their color, making the product more reliable for users. This is why 90% of plastic products globally use additives, as pure plastic generally lacks toughness, durability, and strength. Additives must be combined to make plastic last under harsh environmental conditions.
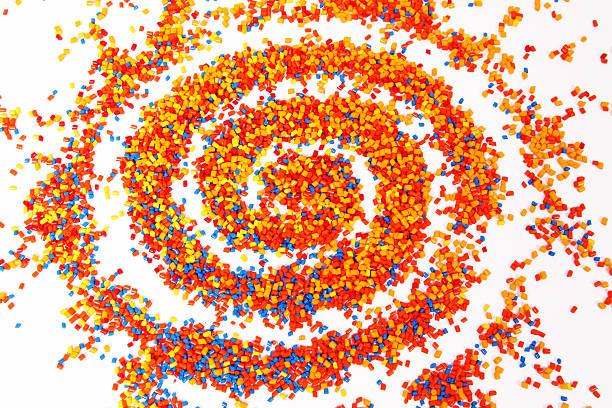
What are the most common plastic additives today?
1. Anti-blocking additives (anti-adhesive)
Adhesion can negatively impact film processing and applications, sometimes rendering the film unusable. Anti-blocking additives roughen the film surface to create a stretching effect, reducing contact between films and preventing them from sticking together.
Anti-blocking agents must be highly effective, with reliable quality and stability, having little or no impact on film performance, especially in LLDPE and LDPE films. Anti-blocking agents are often used alongside slip agents to create an optimal processing environment for films.
Common ingredients of anti-blocking additives include synthetic silica (SiO2) such as fumed silica, gel silica, and zeolite, or natural and mineral SiO2 like clay, diatomaceous earth, quartz, and talc. Synthetic materials have the advantage of not being crystalline (avoiding chalky dust), while natural materials require special treatment to reduce dust.
2. Clarifying agents
During processing, factors like fillers or recycled plastic can reduce product transparency. Clarifying agents offer a solution, increasing product gloss while reducing manufacturing costs.
Clarifying agents can improve clarity at a low rate while offering potential gains through reduced cycle time and energy savings. They do not negatively impact welding, adhesion, or other processing performances.
3. Plastic fillers
Plastic filler masterbatch, typically based on calcium carbonate (CaCO3), is used in the plastic industry to modify the characteristics of resins or polymer resins, reducing product costs.
The mixture of stone powder, additives, and primary resin is melted into liquid resin and cooled into granules, which are then mixed with raw plastic for processes like blow molding, spinning, and injection molding to produce plastic products.
In the processing of PP plastic, factors like shrinkage and warping often affect product quality. Hardening agents help accelerate product molding, reduce warping, and improve transparency. They also shorten press cycles, enhancing production efficiency.
4. UV stabilizers (UV additives)
Ultraviolet light can break the bonds in polymers, causing photochemical degradation and leading to chalking, discoloration, and physical property loss. UV stabilizers like hindered amine light stabilizers (HALS) neutralize free radicals responsible for degradation, thus extending the product's lifespan.
5. Anti-static additives
During processing, plastic granules generate static electricity, attracting dust to the surface. Anti-static additives reduce the film's surface charge, improving safety and reducing dust accumulation.
Types:
Non-durable anti-statics: surface agents, organic salts, ethylene glycol, polyethylene glycol
Durable anti-statics: polyhydroxy polyamines (PHPA), polyalkyl copolymers
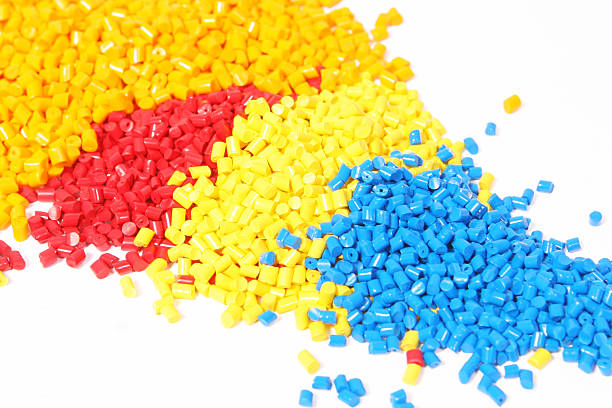
6. Anti-caking additives
Films often stick together due to adhesive forces, opposite charges, or vacuum forces, making it hard to separate them. Anti-caking additives roughen the film surface to allow air to prevent clumping. Some special cases involve anti-static elements to prevent charge buildup.
7. Flame retardant additives
Plastics are highly flammable due to their carbon-chain molecular structure. Flame retardants improve fire resistance through mechanisms like forming protective layers or quenching free radicals.
Common flame retardants:
Halogenated flame retardants
DOPO derivatives
Inorganic: aluminum hydroxide (Al(OH)3), magnesium hydroxide (Mg(OH)2), red phosphorus
Organic: phosphates
8. Anti-fog additives
Anti-fogging agents prevent water from condensing on the surface of plastic films in the form of droplets, which is commonly observed in food packaging stored in refrigerators or greenhouses. These agents maintain clarity and prevent fogging.
Common anti-fog agents:
PLA (polylactic acid)
Lanxess AF DP1-1701
9. Optical brighteners
Optical brighteners, also known as fluorescent whiteners, are commonly used to absorb UV light and emit visible light, enhancing the appearance of plastic products. This helps reduce discoloration, especially in recycled plastics, making colors brighter and more vibrant.
Common optical brighteners: OB-1, OB, KCB, FP (127), KSN, KB.
10. Biodegradation supporting additives
Plastics take a long time to decompose, creating environmental challenges. Biodegradation additives, like Reverte, help speed up plastic degradation under environmental influences like oxygen, sunlight, and temperature.
These additives help transform non-biodegradable plastics into biodegradable materials, similar to natural entities like leaves or plants, contributing to environmental sustainability.
Post time: Sep-27-2024