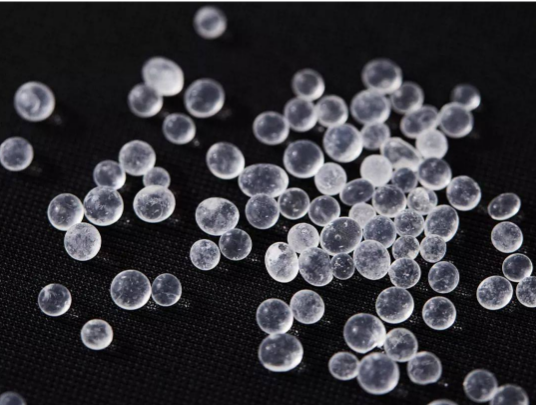
01
Lukier
Matowe tworzywa sztuczne to zazwyczaj folie lub arkusze z tworzyw sztucznych, które podczas kalandrowania mają na rolce różne wzory, odzwierciedlające przezroczystość materiału poprzez różne wzory.
02
Polerowanie
Polerowanie to metoda przetwarzania, która wykorzystuje działanie mechaniczne, chemiczne lub elektrochemiczne w celu zmniejszenia chropowatości powierzchni przedmiotu obrabianego w celu uzyskania jasnej, płaskiej powierzchni.
03
Rozpylający
Natryskiwanie stosuje się głównie do powlekania metalowego sprzętu lub części warstwą tworzywa sztucznego w celu zapewnienia ochrony przed korozją, odporności na zużycie i izolacji elektrycznej. Proces natryskiwania: wyżarzanie → odtłuszczanie → eliminacja elektryczności statycznej i odpylanie → natryskiwanie → suszenie.
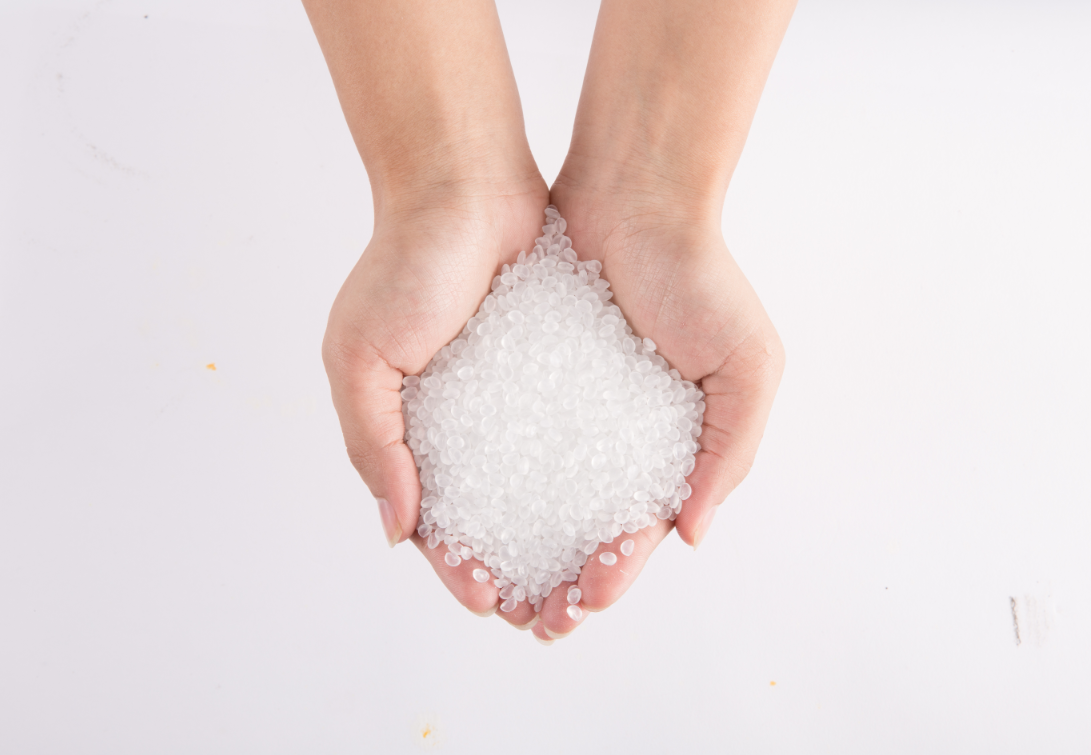
04
Druk
Drukowanie części z tworzyw sztucznych to proces drukowania pożądanego wzoru na powierzchni części z tworzywa sztucznego i można go podzielić na sitodruk, druk powierzchniowy (tampodruk), tłoczenie na gorąco, druk zanurzeniowy (druk transferowy) i druk wytrawiany.
Sitodruk
Sitodruk polega na tym, że farba wylewana jest na sito bez użycia siły zewnętrznej, farba nie wycieknie przez siatkę na podłoże, natomiast gdy rakla przesunie farbę po farbie pod określonym naciskiem i kątem nachylenia, farba zostanie przeniesiona na podłoże poniżej przez ekran, aby uzyskać reprodukcję obrazu.
Tampodruk
Podstawowa zasada tampodruku polega na tym, że w maszynie tampodrukowej atrament jest najpierw umieszczany na stalowej płycie z wygrawerowanym tekstem lub wzorem, który następnie jest kopiowany przez atrament na gumę, która następnie przenosi tekst lub wzór na powierzchnię produktu z tworzywa sztucznego, najlepiej poprzez obróbkę cieplną lub napromieniowanie UV w celu utwardzenia atramentu.
Cechowanie
Proces tłoczenia na gorąco wykorzystuje zasadę przenoszenia ciśnienia cieplnego w celu przeniesienia warstwy elektroaluminium na powierzchnię podłoża, tworząc specjalny efekt metaliczny. Zwykle tłoczenie na gorąco odnosi się do procesu przenoszenia ciepła polegającego na przenoszeniu elektroaluminiowej folii do tłoczenia na gorąco (papieru do tłoczenia na gorąco) na powierzchnię podłoża w określonej temperaturze i ciśnieniu, ponieważ głównym materiałem do tłoczenia na gorąco jest folia elektroaluminiowa , dlatego tłoczenie na gorąco jest również znane jako tłoczenie elektroaluminiowe.
05
IMD – dekoracja w formie
IMD to stosunkowo nowy zautomatyzowany proces produkcyjny, który oszczędza czas i koszty poprzez redukcję etapów produkcji i usuwania komponentów w porównaniu z tradycyjnymi procesami, poprzez drukowanie na powierzchni folii, formowanie pod wysokim ciśnieniem, wykrawanie i ostatecznie łączenie z tworzywem sztucznym bez konieczności stosowania dodatkowych procedur roboczych i czasu pracy, umożliwiając w ten sposób szybką produkcję. Rezultatem jest szybki proces produkcyjny, który oszczędza czas i koszty, a dodatkową korzyścią jest lepsza jakość, większa złożoność obrazu i trwałość produktu.
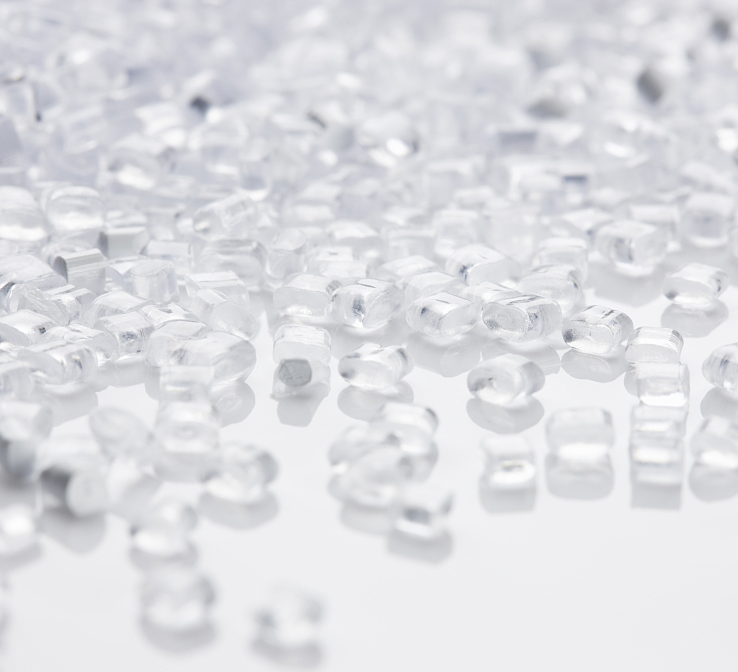
06
Galwanotechnika
Galwanizacja to proces nakładania cienkiej warstwy innych metali lub stopów na powierzchnię niektórych metali na zasadzie elektrolizy, tj. za pomocą elektrolizy w celu przymocowania metalowej folii do powierzchni metalu lub innego materiału w celu zapobiegania utlenianiu (np. rdzy) , poprawić odporność na zużycie, przewodność elektryczną, współczynnik odbicia, odporność na korozję (większość metali używanych do galwanizacji jest odporna na korozję) oraz poprawić estetykę.
07
Teksturowanie formy
Polega na wytrawieniu wnętrza plastikowej formy środkami chemicznymi, takimi jak stężony kwas siarkowy, w celu utworzenia wzorów w postaci wężowania, trawienia i orania. Po uformowaniu tworzywa sztucznego powierzchnia otrzymuje odpowiedni wzór.
Czas publikacji: 30 czerwca 2023 r