තිර මුද්රණය වර්ණ වාත්තු නිපදවන්නේ ඇයි? අපි වර්ණ කිහිපයක මිශ්රණය පසෙකට දමා එක් වර්ණයක් පමණක් සලකා බැලුවහොත්, වර්ණ වාත්තු කිරීමට හේතු සාකච්ඡා කිරීම වඩාත් සරල විය හැකිය. මෙම ලිපිය තිර මුද්රණයේ වර්ණ අපගමනයට බලපාන සාධක කිහිපයක් බෙදා ගනී. අන්තර්ගතය යූපින් ඇසුරුම් ද්රව්ය පද්ධතිය මිලදී ගෙන සපයන මිතුරන් විසින් යොමු කිරීම සඳහා වේ:
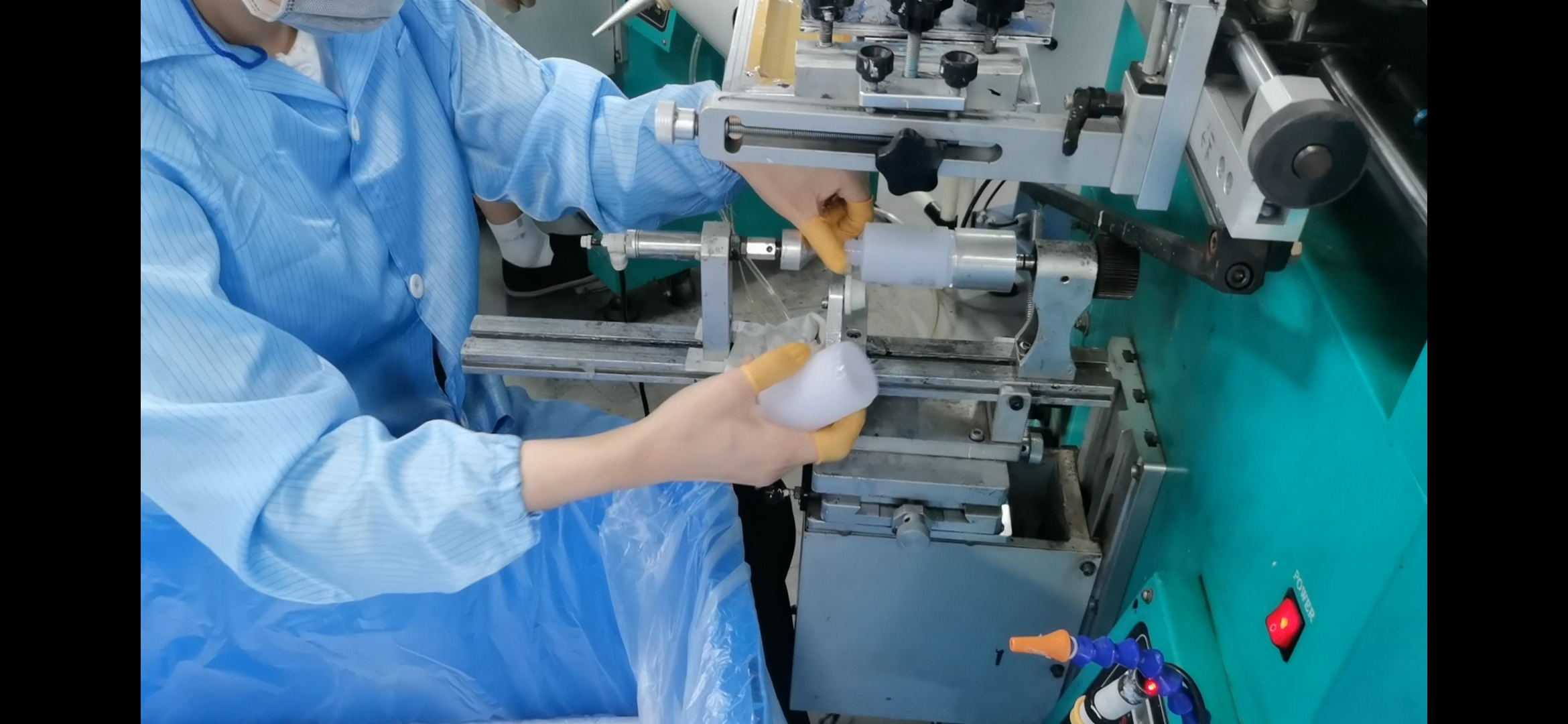
තිර මුද්රණය වර්ණ වාත්තු නිපදවන්නේ ඇයි? අපි වර්ණ කිහිපයක මිශ්රණය පසෙකට දමා එක් වර්ණයක් පමණක් සලකා බැලුවහොත්, වර්ණ වාත්තු කිරීමට හේතු සාකච්ඡා කිරීම වඩාත් සරල විය හැකිය. මෙම ලිපිය තිර මුද්රණයේ වර්ණ අපගමනයට බලපාන සාධක කිහිපයක් බෙදා ගනී. අන්තර්ගතය යූපින් ඇසුරුම් ද්රව්ය පද්ධතිය මිලදී ගෙන සපයන මිතුරන් විසින් යොමු කිරීම සඳහා වේ:
තිර මුද්රණයේදී වර්ණ අපගමනයට හේතු වන වඩාත් පොදු සාධක කිහිපයක් පහත ලැයිස්තුගත කර ඇත: තීන්ත සැකසීම, දැල් තෝරාගැනීම, දැල් ආතතිය, පීඩනය, වියළීම, උපස්ථර ලක්ෂණ, නිරීක්ෂණ තත්ත්වයන් යනාදිය.
01 තීන්ත සකස් කිරීම
තීන්ත මිශ්ර කිරීම භාවිතා කරන තීන්තවල වර්ණකය සම්මත වර්ණකයක් යැයි උපකල්පනය කළහොත්, වර්ණ අපගමනයට විශාලතම හේතුව වන්නේ තීන්ත මිශ්ර කරන තෙල් වැනි ද්රාවක තීන්තවලට එකතු කිරීමයි. හොඳ වර්ණ පාලන උපකරණ සහිත වැඩමුළුවකදී පාලක උපකරණ අනුව තීන්ත මිශ්ර කළ හැකිය. කෙසේ වෙතත්, බොහෝ මුද්රණ සමාගම් සඳහා මෙම පහසුකම් තිබිය නොහැක. ඔවුන් තීන්ත මිශ්ර කිරීමේදී ප්රධාන සේවකයින්ගේ අත්දැකීම් මත පමණක් රඳා පවතී.
සාමාන්යයෙන්, තීන්ත ගැලපුම් තෙල් එකතු කරන්නේ තීන්ත මුද්රණයට වඩාත් යෝග්ය කිරීමටයි. කෙසේ වෙතත්, තීන්තයට ගැලපුම් තෙල් එකතු කළ පසු, තීන්තවල වර්ණක සාන්ද්රණය වෙනස් වන අතර එමඟින් මුද්රණය කිරීමේදී තීන්තවල වර්ණ ලක්ෂණ වෙනස් වේ. මීට අමතරව, තීන්තවල අතිරික්ත ද්රාවණය වියළීමකින් පසු තීන්ත තුනී පටලයක් සාදනු ඇත, එය වර්ණයෙහි දීප්තිය අඩු කරනු ඇත.
තීන්ත දැමීමට පෙර තීන්ත දියකර හැරීමේ ගැටලුවක් ද තිබේ. නිදසුනක් ලෙස, තීන්ත සාප්පුවේ කම්කරුවන් තීන්ත මිශ්ර කිරීමේදී හෝ තනුක කිරීමේදී ඔවුන්ගේ සූත්රය මත පදනම්ව විනිශ්චයන් සිදු කරයි. මෙය නොවැළැක්විය හැකි වර්ණ අපගමනයකට මග පාදයි. දින කිහිපයකට පෙර තීන්ත මිශ්ර කර ඇත්නම්, ඔබ හොඳ තීන්තයකින් මුද්රණය කරන්නේ නම්, මෙම තත්වයෙන් ඇති වන වර්ණ ගැන්වීම වඩාත් පැහැදිලිව පෙනේ. එමනිසා, වර්ණ වාත්තු කිරීම සම්පූර්ණයෙන්ම වළක්වා ගැනීම පාහේ කළ නොහැක්කකි.
02 දැල් තෝරාගැනීම
තීන්ත මාරු කිරීමට බලපාන එකම සාධකය තිරයේ දැල් ප්රමාණය බව ඔබ සිතන්නේ නම්, ඔබට බොහෝ කරදරවලට මුහුණ දීමට සිදුවනු ඇත. දැල් විෂ්කම්භය සහ රැලි ද තීන්ත මාරු කිරීමට බලපායි. සාමාන්යයෙන්, තිරයේ තීන්ත සිදුරුවලට වැඩිපුර තීන්ත සම්බන්ධ වන තරමට, මුද්රණ ක්රියාවලියේදී වැඩි තීන්ත උපස්ථරයට මාරු කරනු ලැබේ.
එක් එක් දැලකින් කොපමණ තීන්ත ප්රමාණයක් මාරු කළ හැකිද යන්න කලින් තක්සේරු කිරීම සඳහා, බොහෝ තිර සැපයුම්කරුවන් එක් එක් දැලෙහි න්යායාත්මක තීන්ත හුවමාරු පරිමාව (TIV) සපයයි. TIV යනු තිරයේ තීන්ත හුවමාරු ප්රමාණයේ ප්රමාණය පෙන්නුම් කරන පරාමිතියකි. නිශ්චිත මුද්රණ තත්ත්වයන් යටතේ එක් එක් දැලකින් කොපමණ තීන්ත ප්රමාණයක් මාරු කරනු ඇත්ද යන්න එය සඳහන් කරයි. එහි ඒකකය යනු ඒකක ප්රදේශයකට තීන්ත පරිමාවයි.
මුද්රණය කිරීමේදී ස්ථාවර නාද සහතික කිරීම සඳහා, තිරයේ දැල් අංකය නොවෙනස්ව තබා ගැනීම ප්රමාණවත් නොවේ, නමුත් තිරයේ විෂ්කම්භය සහ එහි රැළි අඛණ්ඩව පවතින බව සහතික කිරීම. තිරයේ ඕනෑම පරාමිතියක වෙනස්වීම් මුද්රණය කිරීමේදී තීන්ත චිත්රපටයේ ඝණකම වෙනස් වන අතර එහි ප්රතිඵලයක් ලෙස වර්ණ වෙනස් වේ.
03 ශුද්ධ ආතතිය
දැලෙහි ආතතිය ඉතා කුඩා නම්, එය චිත්රපටය පීල් කිරීමට හේතු වේ. දැලෙහි තීන්ත වැඩි නම් මුද්රිත ද්රව්ය අපිරිසිදු වේ.
තිරය සහ උපස්ථරය අතර දුර වැඩි කිරීමෙන් මෙම ගැටළුව විසඳා ගත හැකිය. කෙසේ වෙතත්, තිරය සහ උපස්ථරය අතර දුර වැඩි කිරීම සඳහා පීඩනය වැඩි කිරීම අවශ්ය වේ, එය උපස්ථරයට වැඩි තීන්ත මාරු කිරීමට හේතු වනු ඇත. වර්ණ ඝනත්වය වෙනස් කිරීමට. හොඳම ක්රමය නම් ස්ට්රෙච් නෙට් එකේ ආතතිය ඒකාකාරව තබා ගැනීමයි, එවිට වර්ණයේ අනුකූලතාව සහතික කෙරේ.
04 පීඩන මට්ටම
ස්ථාවර වර්ණ පවත්වා ගැනීම සඳහා නිසි පීඩන සැකසුම් ඉතා වැදගත් වන අතර මුද්රණ ක්රියාවලියේදී ඒකාකාර පීඩන මට්ටම් සහතික කිරීම ඉතා වැදගත් වේ. විශේෂයෙන් ඉහළ ප්රමාණයේ, පුනරාවර්තන මුද්රණ රැකියා වලදී.
පීඩනය සම්බන්ධයෙන් ගත් කල, මුලින්ම සලකා බැලිය යුතු කරුණ වන්නේ මිරිකීමේ දෘඪතාවයි. ස්කීජියේ දෘඪතාව කුඩා වන අතර, එය සම්බන්ධතා අනුපාතය සඳහා හොඳ වේ, නමුත් එය නැමීමේ ප්රතිරෝධය සඳහා හොඳ නොවේ. තද බව වැඩි නම්, මුද්රණය කිරීමේදී තිරයේ ඝර්ෂණය ද විශාල වන අතර එමඟින් මුද්රණ නිරවද්යතාවයට බලපායි. දෙවෙනි එක තමයි squeegee සහ squeegee වේගයේ කෝණය. තීන්ත පිහියෙහි කෝණය තීන්ත මාරු කිරීමේ ප්රමාණයට සැලකිය යුතු බලපෑමක් ඇති කරයි. තීන්ත පිහියේ කෝණය කුඩා වන තරමට තීන්ත මාරු කිරීමේ ප්රමාණය වැඩි වේ. තීන්ත පිහි වේගය ඉතා වේගවත් නම්, එය ප්රමාණවත් තීන්ත පිරවීමක් සහ අසම්පූර්ණ මුද්රණයක් ඇති කරයි, එමඟින් මුද්රණයේ ගුණාත්මක භාවයට බලපායි.
ඔබ මුද්රණ කාර්යයක් සඳහා නිවැරදි පීඩන සැකසුම් ලබාගෙන ඒවා නිවැරදිව වාර්තා කළ පසු, මුද්රණ ක්රියාවලියේදී ඔබ මෙම සැකසුම් නිවැරදිව අනුගමනය කරන තාක් කල්, ඔබට ස්ථාවර වර්ණ සහිත සතුටුදායක මුද්රණ නිෂ්පාදනයක් ලැබෙනු ඇත.
05 වියළි
සමහර විට, මුද්රණය කිරීමෙන් පසු වර්ණය ස්ථාවර ලෙස පෙනේ, නමුත් නිමි භාණ්ඩය සොයාගත් පසු වර්ණය වෙනස් වේ. මෙය බොහෝ විට වියළන උපකරණවල වැරදි සැකසුම් නිසා සිදු වේ. වඩාත්ම පොදු හේතුව වන්නේ වියළන යන්ත්රයේ උෂ්ණත්වය ඉතා ඉහළ මට්ටමක තබා ඇති අතර, කඩදාසි හෝ කාඩ්බෝඩ් මත තීන්ත වර්ණය වෙනස් වේ.
06 උපස්ථර ලක්ෂණ
තිර මුද්රණ ශිල්පීන් බොහෝ විට නොසලකා හරින එක් ගැටළුවක් වන්නේ උපස්ථරයේ මතුපිට ගුණාංගයි. කඩදාසි, කාඩ්බෝඩ්, ප්ලාස්ටික්, ආදිය කාණ්ඩවල නිෂ්පාදනය කරනු ලබන අතර, උසස් තත්ත්වයේ උපස්ථරවලට ස්ථාවර සහ ස්ථාවර මතුපිට ගුණාංග සහතික කළ හැකිය. නමුත් මෙය එසේ නොවේ. උපස්ථරයේ මතුපිට ගුණාංගවල කුඩා වෙනස්කම් මුද්රණය කිරීමේදී වර්ණ අපගමනය ඇති කරයි. මුද්රණ පීඩනය ඒකාකාරී වුවත්, සෑම ක්රියාවලියක්ම නිවැරදිව ක්රියාත්මක වුවද, උපස්ථරයේ මතුපිට ගුණාංගවල නොගැලපීම් මුද්රණයේ විශාල වර්ණ මාරුවීම් ඇති කරයි. වර්ණ ගැන්වීම.
එකම භාණ්ඩය එකම මුද්රණ උපකරණ සමඟ විවිධ උපස්ථර මත මුද්රණය කරන විට, වර්ණය මත උපස්ථරයේ මතුපිට ගුණාංගවල බලපෑම විශේෂයෙන් පැහැදිලිය. පාරිභෝගිකයින්ට කවුළු දැන්වීම් ප්ලාස්ටික් හෝ වෙනත් කාඩ්බෝඩ් මත මුද්රණය කිරීමට අවශ්ය විය හැකිය. සේවාදායකයින්ට එකම කෑල්ල සඳහා ස්ථාවර වර්ණ අවශ්ය විය හැකිය.
එවැනි අවස්ථාවන්හිදී, එකම විසඳුම නිවැරදි වර්ණ මිනුම් සිදු කිරීමයි. වර්ණ ඝනත්වය මැනීම සඳහා වර්ණාවලි ඡායාරූපමානයක් හෝ වර්ණාවලි ඩෙන්සිටෝමීටරයක් භාවිතා කරන්න. වර්ණ මාරුවක් තිබේ නම්, ඩෙන්සිටෝමීටරයට එය පැහැදිලිව පරාවර්තනය කළ හැකි අතර, වෙනත් ක්රියාවලීන් පාලනය කිරීමෙන් ඔබට මෙම වර්ණ මාරුව ජය ගත හැකිය.
07 නිරීක්ෂණ කොන්දේසි
මිනිස් ඇස් වර්ණයෙහි සියුම් වෙනස්කම් වලට ඉතා සංවේදී වන අතර ආලෝක තත්ත්වයන් යටතේ පමණක් වර්ණ වෙන්කර හඳුනාගත හැකිය. මේ නිසා, එකම ආලෝක තත්ත්වයන් යටතේ වර්ණ සංසන්දනය කිරීමට වග බලා ගන්න. එසේ නොමැති නම්, තීන්ත පරිමාව හෝ පීඩනය සකස් කිරීමෙන් වැඩි තීන්ත නිපදවනු ඇත. විශාල වර්ණ ගැන්වීම.
සමස්තයක් ලෙස ගත් කල, ස්ථාවර වර්ණයක් පවත්වා ගැනීමේ යතුර පවතින්නේ තීන්තවල ස්ථාවර ක්රියාකාරිත්වය සහතික කිරීම සඳහා එක් එක් ක්රියාවලියේ ස්ථායී පාලනය තුළ ය. දැල් ප්රමාණය තෝරා ගැනීම, දිගු තිරයේ ආතතිය සහ පීඩනය, උපස්ථරයේ මතුපිට ලක්ෂණ සහ නිරීක්ෂණ තත්වයන් වර්ණ අපගමනය කෙරෙහි යම් බලපෑමක් ඇති කරයි. කෙසේ වෙතත්, නිරවද්ය සැකසුම් වාර්තා සහ එක් එක් ක්රියාවලියේ ස්ථාවර පාලනය ස්ථාවර තිර මුද්රණ වර්ණ සහතික කිරීම සඳහා යතුර වේ.
පසු කාලය: ජනවාරි-08-2024