АБС, обично познат као акрилонитрил бутадиен стирен, настаје кополимеризацијом три мономера акрилонитрил-бутадиен-стирена. Због различитих пропорција три мономера, могу постојати различита својства и температура топљења, перформансе мобилности АБС-а, мешање са другом пластиком или адитивима, може проширити употребу и перформансе АБС-а.
Флуидност АБС-а је између ПС и ПЦ, а његова флуидност је повезана са температуром и притиском убризгавања, а утицај притиска убризгавања је нешто већи. Због тога се у калуповању често користи већи притисак убризгавања како би се смањио вискозитет растопа и побољшало пуњење калупа. перформансе.
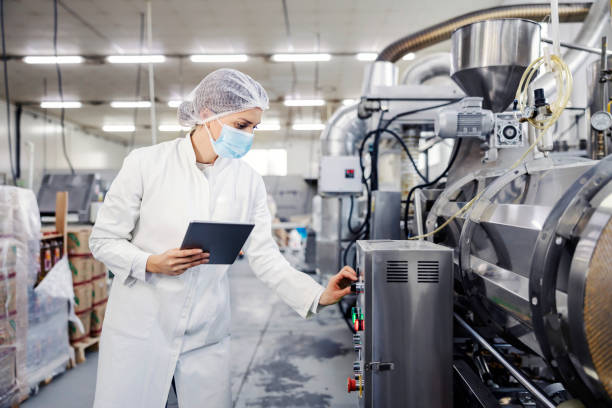
1. Прерада пластике
Стопа апсорпције воде АБС-а је око 0,2% -0,8%. За АБС опште класе, треба га пећи у рерни на 80-85°Ц 2-4 сата или у посуди за сушење на 80°Ц 1-2 сата пре обраде. За АБС отпорне на топлоту које садрже ПЦ компоненте, температуру сушења треба на одговарајући начин повећати на 100°Ц, а специфично време сушења може се одредити екструзијом ваздуха.
Удео рециклираних материјала не може бити већи од 30%, а АБС за галванизацију не може користити рециклиране материјале.
2. Избор машине за бризгање
Може се изабрати Рамадина стандардна машина за бризгање (однос дужине завртња и пречника 20:1, степен компресије већи од 2, притисак бризгања већи од 1500 бара). Ако се користи мастербатцх у боји или је изглед производа висок, може се изабрати вијак мањег пречника. Сила стезања се одређује према 4700-6200т/м2, што зависи од квалитета пластике и захтева производа.
3. Дизајн калупа и капија
Температура калупа се може подесити на 60-65°Ц. Пречник клизача 6-8 мм. Ширина капије је око 3 мм, дебљина је иста као и код производа, а дужина капије треба да буде мања од 1 мм. Отвор за вентилацију је широк 4-6 мм и дебљине 0,025-0,05 мм.
4. Температура топљења
Може се тачно одредити методом убризгавања ваздуха. Различити разреди имају различиту температуру топљења, препоручена подешавања су следећа:
Степен удара: 220°Ц-260°Ц, пожељно 250°Ц
Степен галванизације: 250°Ц-275°Ц, пожељно 270°Ц
Отпорност на топлоту: 240°Ц-280°Ц, пожељно 265°Ц-270°Ц
Отпорност на ватру: 200°Ц-240°Ц, пожељно 220°Ц-230°Ц
Провидност: 230°Ц-260°Ц, пожељно 245°Ц
Степен ојачан стакленим влакнима: 230℃-270℃
За производе са високим захтевима за површину, користите вишу температуру топљења и температуру калупа.
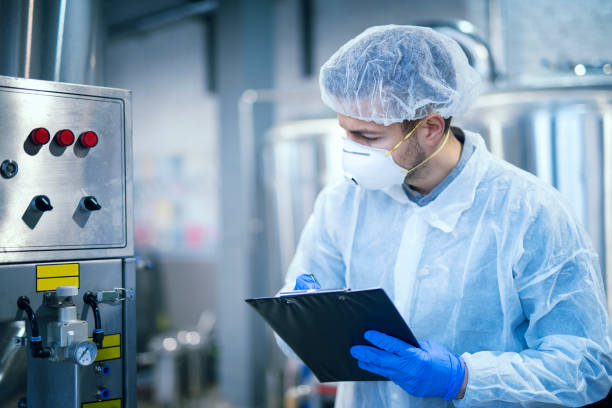
5. Брзина убризгавања
Мала брзина се користи за отпорност на ватру, а велика брзина се користи за отпорност на топлоту. Ако су површински захтеви производа високи, треба користити контролу брзине убризгавања велике брзине и вишестепено бризгање.
6. Повратни притисак
Генерално, што је мањи повратни притисак, то боље. Уобичајени противпритисак је 5 бара, а материјалу за бојење је потребан већи повратни притисак да би се мешање боја уједначило.
7. Време боравка
На температури од 265°Ц, време задржавања АБС-а у цилиндру за топљење не би требало да прелази највише 5-6 минута. Време успорења пламена је краће. Ако је потребно зауставити машину, потребно је прво спустити подешену температуру на 100°Ц, а затим очистити растопљени пластични цилиндар АБС-ом опште намене. Очишћену мешавину треба ставити у хладну воду како би се спречило даље распадање. Ако треба да пређете са друге пластике на АБС, прво морате очистити цилиндар од растопљене пластике са ПС, ПММА или ПЕ. Неки АБС производи немају проблема када су тек пуштени из калупа, али ће променити боју након одређеног временског периода, што може бити узроковано прегревањем или предуго задржавањем пластике у цилиндру за топљење.
8. Накнадна обрада производа
Генерално, АБС производи не захтевају накнадну обраду, само производи за галванизацију треба да се пеку (70-80°Ц, 2-4 сата) да би се пасивизирали површински трагови, а производи који треба да буду галванизовани не могу да користе средство за одвајање , а производи се морају упаковати одмах након изношења .
9. Ствари којима је потребна посебна пажња приликом обликовања
Постоји неколико разреда АБС-а (посебно отпорног на ватру), чија талина има јаку адхезију на површини вијка након пластификације и распада се након дужег времена. Када дође до горе наведене ситуације потребно је извући део за хомогенизацију шрафа и компресор за брисање, а вијак редовно чистити ПС итд.
Време поста: 09.08.2023