Pompa semprot seueur dianggo dina industri kosmétik, sapertos parfum, penyegar hawa, sareng semprotan tabir surya. Kinerja pompa semprot langsung mangaruhan pangalaman pangguna, janten komponén anu penting.
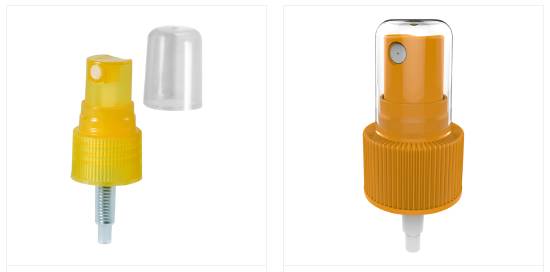
Harti produk
Pompa semprot, ogé katelah apanyemprot, mangrupakeun komponén konci dina wadah kosmetik. Éta ngagunakeun prinsip kasaimbangan atmosfir pikeun ngaluarkeun cairan di jero botol ku mencét ka handap. Aliran cairan anu gancang-gancang nyababkeun hawa caket nozzle ngalih, ningkatkeun kagancangan sareng ngirangan tekananna, nyiptakeun daérah tekanan rendah lokal. Hal ieu ngamungkinkeun hawa sabudeureun nyampur jeung cair, nyieun éfék aerosol.
Prosés Manufaktur
1. Prosés Molding
Bagian snap-on (aluminium semi-snap, aluminium full-snap) sareng benang screw dina pompa semprot biasana didamel tina plastik, sakapeung nganggo lapisan panutup aluminium atanapi aluminium dilapis. Kalolobaan komponén internal tina pompa semprot dijieunna tina plastik kayaning pe, PP, sarta LDPE ngaliwatan suntik molding. manik kaca jeung cinyusu ilaharna outsourced.
2. Perlakuan beungeut
Komponén utama pompa semprot tiasa ngalaman perlakuan permukaan sapertos vakum electroplating, aluminium electroplated, nyemprot, sareng suntikan molding dina sababaraha warna.
3. Ngolah Grafik
Permukaan nozzle semprot sareng kerah tiasa dicitak nganggo grafik sareng téks nganggo téknik sapertos stamping panas sareng percetakan layar sutra. Nanging, pikeun ngajaga kesederhanaan, percetakan umumna dihindari dina nozzle.
Struktur produk
1. Komponén utama
Pompa semprot has diwangun ku nozzle / sirah, diffuser, tube sentral, panutup konci, gasket sealing, inti piston, piston, spring, awak pompa, sarta tabung nyeuseup. Piston nyaéta piston kabuka anu nyambungkeun sareng korsi piston. Nalika rod komprési ngalir ka luhur, awak pompa muka ka luar, sarta nalika eta ngalir ka handap, chamber kerja disegel. Komponén husus bisa rupa-rupa dumasar kana desain pompa, tapi prinsip jeung tujuan tetep sarua: mun éféktif dispense eusi.
2. Rujukan Struktur Produk
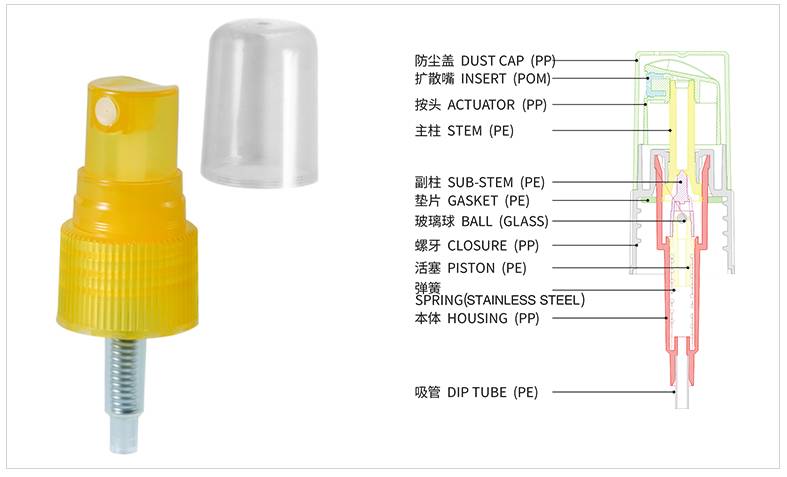
3. Prinsip Dispensing Cai
Prosés knalpot:
Anggap kaayaan awal teu boga cairan dina chamber kerja dasar. Mencét ka handap sirah pompa compresses rod, pindah piston ka handap, compressing spring. Volume kamar kerja nurun, ngaronjatkeun tekanan hawa, sealing klep cai di tungtung luhur tabung nyeuseup urang. Kusabab piston sareng korsi piston henteu disegel lengkep, hawa kaluar tina celah antara aranjeunna.
Prosés nyeuseup cai:
Saatos prosés knalpot, ngaleupaskeun sirah pompa ngamungkinkeun cinyusu dikomprés dilegakeun, ngadorong korsi piston ka luhur, nutup celah antara piston jeung korsi piston, sarta mindahkeun piston jeung rod komprési ka luhur. Ieu ngaronjatkeun volume chamber gawe, ngurangan tekanan hawa, nyieun kaayaan vakum deukeut, ngabalukarkeun klep cai kabuka sarta cairan ditarik kana awak pompa tina wadahna.
Prosés Dispensing Cai:
Prinsipna sami sareng prosés knalpot, tapi kalayan cairan dina awak pompa. Nalika mencét sirah pompa, klep cai ngégél tungtung luhur tabung nyeuseup, nyegah cairan balik deui kana wadahna. Cairan, anu teu tiasa dikomprés, ngalir ngaliwatan celah antara piston sareng korsi piston kana tabung komprési sareng kaluar tina nozzle.
Prinsip atomisasi:
Alatan bubuka nozzle leutik, pencét lemes nyiptakeun laju aliran tinggi. Nalika cairan kaluar tina liang leutik, lajuna ningkat, nyababkeun hawa di sakurilingna langkung gancang sareng ngirangan tekanan, ngabentuk daérah tekanan rendah lokal. Hal ieu ngabalukarkeun hawa sabudeureun campur jeung cairan, nyieun éfék aerosol sarupa aliran hawa-speed tinggi mangaruhan ogé titik-titik cai, megatkeun kana ogé titik-titik leutik.
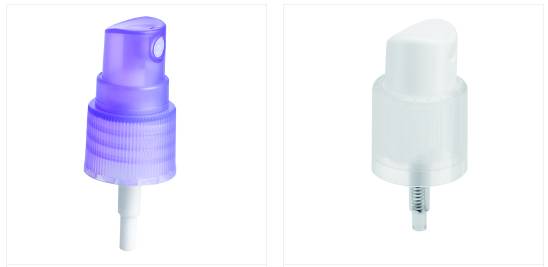
Aplikasi dina Produk Kosmétik
Pompa semprot seueur dianggo dina produk kosmetik sapertos parfum, gel rambut, penyegar hawa, sareng sérum.
Pertimbangan Purchasing
Dispenser digolongkeun kana jinis snap-on sareng screw-on.
Ukuran sirah pompa cocog diaméter botol, kalawan spésifikasi semprot mimitian ti 12.5mm mun 24mm sarta volume ngurangan tina 0.1ml mun 0.2ml per pencét, ilahar dipaké pikeun parfum jeung gels bulu. Panjang tabung tiasa disaluyukeun dumasar kana jangkungna botol.
Ukur dosis semprot tiasa dilakukeun nganggo metode pangukuran tare atanapi pangukuran nilai mutlak, kalayan margin kasalahan dina 0,02g. Ukuran pompa ogé nangtukeun dosis.
Molds pompa semprot seueur sareng mahal.
waktos pos: Jul-12-2024