ஸ்கிரீன் பிரிண்டிங் ஏன் வண்ண வார்ப்புகளை உருவாக்குகிறது? பல வண்ணங்களின் கலவையை ஒதுக்கி வைத்துவிட்டு, ஒரே ஒரு நிறத்தை மட்டுமே கருத்தில் கொண்டால், வண்ண வார்ப்புக்கான காரணங்களைப் பற்றி விவாதிப்பது எளிதாக இருக்கும். இந்த கட்டுரை திரை அச்சிடலில் வண்ண விலகலை பாதிக்கும் பல காரணிகளைப் பகிர்ந்து கொள்கிறது. யூபின் பேக்கேஜிங் மெட்டீரியல் சிஸ்டத்தை வாங்கி சப்ளை செய்யும் நண்பர்களின் குறிப்புக்கான உள்ளடக்கம்:
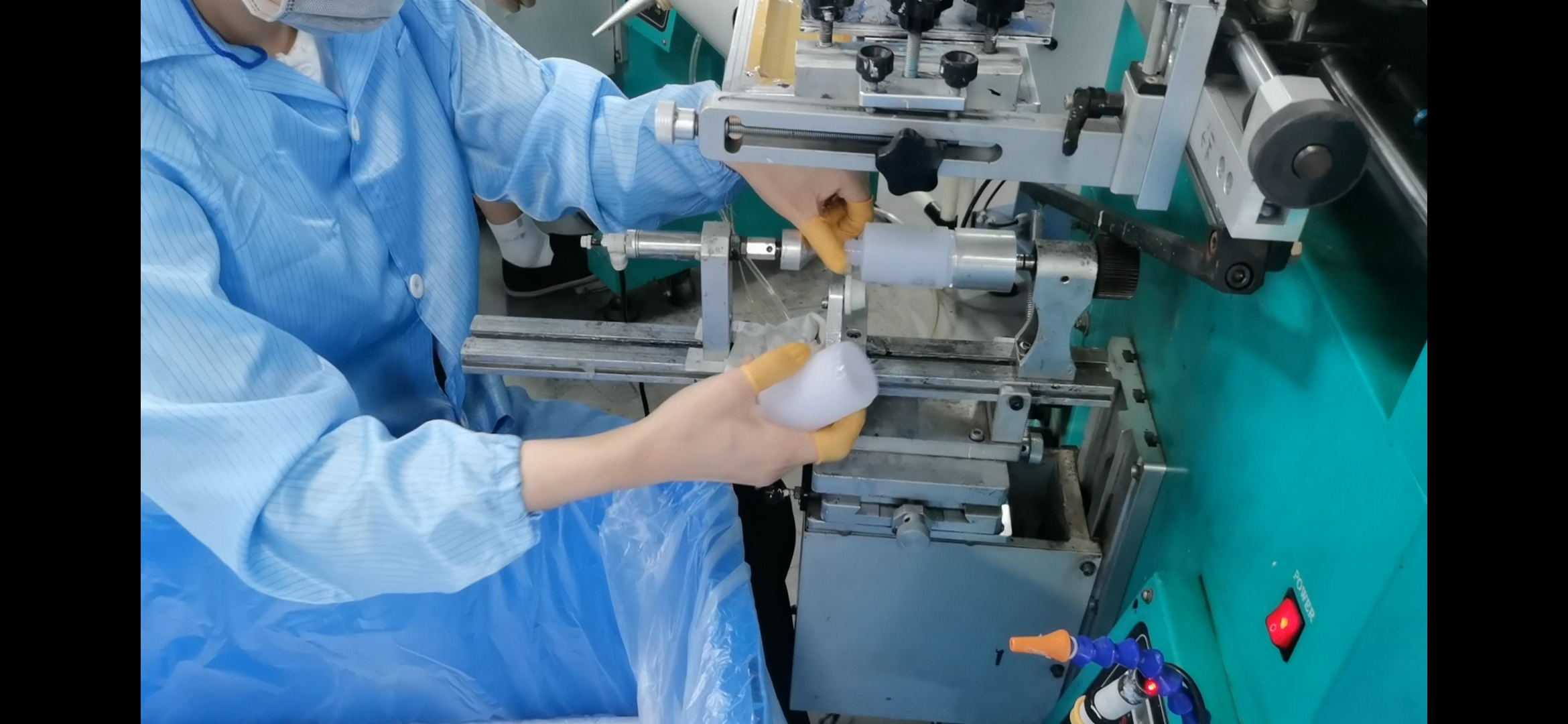
ஸ்கிரீன் பிரிண்டிங் ஏன் வண்ண வார்ப்புகளை உருவாக்குகிறது? பல வண்ணங்களின் கலவையை ஒதுக்கி வைத்துவிட்டு, ஒரே ஒரு நிறத்தை மட்டுமே கருத்தில் கொண்டால், வண்ண வார்ப்புக்கான காரணங்களைப் பற்றி விவாதிப்பது எளிதாக இருக்கும். இந்த கட்டுரை திரை அச்சிடலில் வண்ண விலகலை பாதிக்கும் பல காரணிகளைப் பகிர்ந்து கொள்கிறது. யூபின் பேக்கேஜிங் மெட்டீரியல் சிஸ்டத்தை வாங்கி சப்ளை செய்யும் நண்பர்களின் குறிப்புக்கான உள்ளடக்கம்:
ஸ்கிரீன் பிரிண்டிங்கில் வண்ண விலகலை ஏற்படுத்தும் பொதுவான காரணிகளில் சில கீழே பட்டியலிடப்பட்டுள்ளன: மை தயாரிப்பு, கண்ணி தேர்வு, கண்ணி பதற்றம், அழுத்தம், உலர்த்துதல், அடி மூலக்கூறு பண்புகள், கவனிப்பு நிலைமைகள் போன்றவை.
01 மை தயாரிப்பு
மை கலத்தல் பயன்படுத்தப்படும் மையின் நிறமி ஒரு நிலையான நிறமி என்று கருதி, வண்ண விலகலுக்கு மிகப்பெரிய காரணம் மை கலக்கும் எண்ணெய் போன்ற கரைப்பான்களைச் சேர்ப்பதாகும். நல்ல வண்ணக் கட்டுப்பாட்டு கருவிகளைக் கொண்ட பட்டறையில், கட்டுப்பாட்டு உபகரணங்களுக்கு ஏற்ப மை கலக்கலாம். இருப்பினும், பெரும்பாலான அச்சு நிறுவனங்களுக்கு, இந்த வசதிகள் இருக்க முடியாது. மை கலக்கும் போது அவர்கள் முதன்மை தொழிலாளர்களின் அனுபவத்தை மட்டுமே நம்பியிருக்கிறார்கள்.
பொதுவாக, மையை அச்சிடுவதற்கு ஏற்றவாறு மை-சரிசெய்யும் எண்ணெய் சேர்க்கப்படுகிறது. இருப்பினும், மையில் சரிசெய்யும் எண்ணெய் சேர்க்கப்பட்டவுடன், மையில் உள்ள நிறமிகளின் செறிவு மாறும், இது அச்சிடும் போது மையின் வண்ண பண்புகளில் மாற்றங்களுக்கு வழிவகுக்கும். கூடுதலாக, மை உள்ள அதிகப்படியான கரைப்பான் உலர்த்திய பிறகு மை ஒரு மெல்லிய படத்தை உருவாக்கும், இது நிறத்தின் பிரகாசத்தை குறைக்கும்.
மை இடுவதற்கு முன் மை நீர்த்துப்போகும் பிரச்சனையும் உள்ளது. எடுத்துக்காட்டாக, மை கடையில் உள்ள தொழிலாளர்கள் மை கலக்கும்போது அல்லது நீர்த்துப்போகும்போது அவர்களின் சூத்திரத்தின் அடிப்படையில் தீர்ப்புகளை வழங்குகிறார்கள். இது தவிர்க்க முடியாத வண்ண விலகலுக்கு வழிவகுக்கிறது. சில நாட்களுக்கு முன்பு மை கலந்திருந்தால், நல்ல மை கொண்டு அச்சிட்டால், இந்த சூழ்நிலையால் ஏற்படும் வண்ணம் இன்னும் தெளிவாகத் தெரியும். எனவே, வண்ண வார்ப்புகளை முற்றிலும் தவிர்ப்பது கிட்டத்தட்ட சாத்தியமற்றது.
02 மெஷ் தேர்வு
மை பரிமாற்றத்தை பாதிக்கும் ஒரே காரணியாக திரையின் கண்ணி அளவு மட்டுமே இருப்பதாக நீங்கள் நினைத்தால், நீங்கள் நிறைய பிரச்சனைகளை சந்திக்க நேரிடும். கண்ணி விட்டம் மற்றும் சுருக்கங்கள் மை பரிமாற்றத்தையும் பாதிக்கின்றன. பொதுவாக, திரையின் மை துளைகளில் எவ்வளவு மை இணைக்கப்படுகிறதோ, அவ்வளவு மை அச்சிடும் செயல்பாட்டின் போது அடி மூலக்கூறுக்கு மாற்றப்படும்.
ஒவ்வொரு கண்ணி மூலம் எவ்வளவு மை மாற்ற முடியும் என்பதை முன்கூட்டியே மதிப்பிடுவதற்காக, பல திரை வழங்குநர்கள் ஒவ்வொரு கண்ணியின் தத்துவார்த்த மை பரிமாற்ற அளவை (TIV) வழங்குகிறார்கள். TIV என்பது திரையின் மை பரிமாற்ற அளவின் அளவைக் குறிக்கும் அளவுருவாகும். குறிப்பிட்ட அச்சிடும் நிலைமைகளின் கீழ் ஒவ்வொரு கண்ணி மூலம் எவ்வளவு மை மாற்றப்படும் என்பது ஒரு குறிப்பிட்ட மையின் அளவைக் குறிக்கிறது. அதன் அலகு ஒரு யூனிட் பகுதிக்கு மை அளவு ஆகும்.
அச்சிடுவதில் நிலையான டோன்களை உறுதிப்படுத்த, திரையின் மெஷ் எண்ணை மாற்றாமல் வைத்திருப்பது போதாது, ஆனால் திரையின் விட்டம் மற்றும் அதன் அலை அலையானது மாறாமல் இருப்பதை உறுதி செய்ய வேண்டும். திரையின் எந்த அளவுருவிலும் ஏற்படும் மாற்றங்கள் அச்சிடும்போது மை படத்தின் தடிமன் மாற்றங்களை ஏற்படுத்தும், இதன் விளைவாக வண்ண மாற்றங்கள் ஏற்படும்.
03 நிகர பதற்றம்
வலையின் பதற்றம் மிகவும் சிறியதாக இருந்தால், அது படத்தை உரிக்கச் செய்யும். கண்ணியில் அதிக மை தங்கிவிட்டால், அச்சிடப்பட்ட பொருட்கள் அழுக்காகிவிடும்.
திரைக்கும் அடி மூலக்கூறுக்கும் இடையிலான தூரத்தை அதிகரிப்பதன் மூலம் இந்த சிக்கலை தீர்க்க முடியும். இருப்பினும், திரைக்கும் அடி மூலக்கூறுக்கும் இடையே உள்ள தூரத்தை அதிகரிக்க அழுத்தம் அதிகரிக்க வேண்டும், இது அடி மூலக்கூறுக்கு அதிக மை மாற்றத்தை ஏற்படுத்தும். நிறத்தின் அடர்த்தியை மாற்ற. வண்ணத்தின் நிலைத்தன்மையை உறுதிசெய்ய, நீட்சி வலையின் பதற்றத்தை ஒரே சீராக வைத்திருப்பதே சிறந்த வழி.
04 அழுத்தம் நிலை
சீரான நிறத்தை பராமரிக்க சரியான அழுத்த அமைப்புகள் முக்கியம், மேலும் அச்சிடும் செயல்பாட்டின் போது சீரான அழுத்த நிலைகளை உறுதி செய்வது மிகவும் முக்கியமானது. குறிப்பாக அதிக அளவு, மீண்டும் மீண்டும் அச்சிடுதல் வேலைகளில்.
அழுத்தத்தைப் பொறுத்தவரை, முதலில் கருத்தில் கொள்ள வேண்டியது ஸ்க்யூஜியின் கடினத்தன்மை. ஸ்கீஜியின் கடினத்தன்மை சிறியது, இது தொடர்பு விகிதத்திற்கு நல்லது, ஆனால் வளைக்கும் எதிர்ப்பிற்கு இது நல்லதல்ல. கடினத்தன்மை அதிகமாக இருந்தால், அச்சிடும் போது திரையில் உராய்வு அதிகமாக இருக்கும், இதனால் அச்சிடும் துல்லியம் பாதிக்கப்படும். இரண்டாவது squeegee மற்றும் squeegee வேகம் கோணம். மை கத்தியின் கோணம் மை பரிமாற்றத்தின் அளவு மீது குறிப்பிடத்தக்க தாக்கத்தை ஏற்படுத்துகிறது. மை கத்தியின் சிறிய கோணம், மை பரிமாற்றத்தின் அளவு அதிகமாகும். மை கத்தி வேகம் மிக வேகமாக இருந்தால், அது போதுமான மை நிரப்புதல் மற்றும் முழுமையற்ற அச்சிடலை ஏற்படுத்தும், இதனால் அச்சின் தரம் பாதிக்கப்படும்.
அச்சுப் பணிக்கான சரியான அழுத்த அமைப்புகளைப் பெற்று, அவற்றைத் துல்லியமாகப் பதிவுசெய்த பிறகு, அச்சிடும் செயல்பாட்டின் போது இந்த அமைப்புகளைச் சரியாகப் பின்பற்றும் வரை, நிலையான வண்ணங்களுடன் திருப்திகரமான அச்சுத் தயாரிப்பைப் பெறுவீர்கள்.
05 உலர்
சில நேரங்களில், அச்சிடும் பிறகு நிறம் சீராகத் தெரிகிறது, ஆனால் முடிக்கப்பட்ட தயாரிப்பு கண்டுபிடிக்கப்பட்ட பிறகு நிறம் மாறுகிறது. உலர்த்தும் கருவிகளின் தவறான அமைப்புகளால் இது பெரும்பாலும் ஏற்படுகிறது. மிகவும் பொதுவான காரணம் என்னவென்றால், உலர்த்தியின் வெப்பநிலை மிக அதிகமாக அமைக்கப்பட்டுள்ளது, இதனால் காகிதம் அல்லது அட்டைப் பெட்டியில் மை நிறம் மாறுகிறது.
06 அடி மூலக்கூறு பண்புகள்
ஸ்கிரீன் பிரிண்டிங் மாஸ்டர்கள் பெரும்பாலும் கவனிக்காத ஒரு பிரச்சினை அடி மூலக்கூறின் மேற்பரப்பு பண்புகள் ஆகும். காகிதம், அட்டை, பிளாஸ்டிக், முதலியன அனைத்தும் தொகுதிகளாக உற்பத்தி செய்யப்படுகின்றன, மேலும் உயர்தர அடி மூலக்கூறுகள் நிலையான மற்றும் நிலையான மேற்பரப்பு பண்புகளை உறுதி செய்ய முடியும். ஆனால் இது அப்படியல்ல. அடி மூலக்கூறின் மேற்பரப்பு பண்புகளில் சிறிய மாற்றங்கள் அச்சிடுவதில் வண்ண விலகல்களை ஏற்படுத்தும். அச்சிடும் அழுத்தம் சீரானதாக இருந்தாலும், ஒவ்வொரு செயல்முறையும் சரியாகச் செயல்பட்டாலும் கூட, அடி மூலக்கூறின் மேற்பரப்பு பண்புகளில் உள்ள முரண்பாடுகள் அச்சிடலில் பெரிய வண்ண மாற்றங்களை ஏற்படுத்தும். வண்ண வார்ப்பு.
ஒரே தயாரிப்பு வெவ்வேறு அடி மூலக்கூறுகளில் ஒரே அச்சிடும் உபகரணங்களுடன் அச்சிடப்பட்டால், வண்ணத்தில் அடி மூலக்கூறின் மேற்பரப்பு பண்புகளின் செல்வாக்கு குறிப்பாக வெளிப்படையானது. வாடிக்கையாளர்கள் சாளர விளம்பரங்களை பிளாஸ்டிக் அல்லது பிற அட்டைப் பெட்டியில் அச்சிட வேண்டும். வாடிக்கையாளர்களுக்கு ஒரே மாதிரியான நிறங்கள் தேவைப்படலாம்.
இதுபோன்ற சூழ்நிலைகளில், துல்லியமான வண்ண அளவீடுகளைச் செய்வதுதான் ஒரே தீர்வு. வண்ண அடர்த்தியை அளவிட ஸ்பெக்ட்ரோஃபோட்டோமீட்டர் அல்லது ஸ்பெக்ட்ரல் டென்சிடோமீட்டரைப் பயன்படுத்தவும். ஒரு வண்ண மாற்றம் இருந்தால், டென்சிடோமீட்டர் அதை தெளிவாக பிரதிபலிக்க முடியும், மற்ற செயல்முறைகளை கட்டுப்படுத்துவதன் மூலம் இந்த வண்ண மாற்றத்தை நீங்கள் சமாளிக்க முடியும்.
07 கண்காணிப்பு நிபந்தனைகள்
மனித கண்கள் நிறத்தில் உள்ள நுட்பமான மாற்றங்களுக்கு மிகவும் உணர்திறன் கொண்டவை, மேலும் ஒளியின் நிலைகளில் மட்டுமே வண்ணங்களை வேறுபடுத்த முடியும். இதன் காரணமாக, அதே லைட்டிங் நிலைமைகளின் கீழ் வண்ணங்களை ஒப்பிட்டுப் பார்க்கவும். இல்லையெனில், மை அளவு அல்லது அழுத்தத்தை சரிசெய்வது அதிக மையை உருவாக்கும். பெரிய வண்ண வார்ப்பு.
மொத்தத்தில், நிலையான நிறத்தை பராமரிப்பதற்கான திறவுகோல், மையின் நிலையான செயல்திறனை உறுதிப்படுத்த ஒவ்வொரு செயல்முறையின் நிலையான கட்டுப்பாட்டில் உள்ளது. கண்ணி அளவு, பதற்றம் மற்றும் நீட்டிக்கப்பட்ட திரையின் அழுத்தம், அடி மூலக்கூறின் மேற்பரப்பு பண்புகள் மற்றும் கவனிப்பு நிலைமைகள் அனைத்தும் வண்ண விலகலில் ஒரு குறிப்பிட்ட தாக்கத்தை ஏற்படுத்துகின்றன. இருப்பினும், துல்லியமான அமைப்பு பதிவுகள் மற்றும் ஒவ்வொரு செயல்முறையின் நிலையான கட்டுப்பாடும் நிலையான திரை அச்சிடுதல் வண்ணங்களை உறுதி செய்வதற்கான விசைகள் ஆகும்.
இடுகை நேரம்: ஜன-08-2024