స్క్రీన్ ప్రింటింగ్ కలర్ కాస్ట్లను ఎందుకు ఉత్పత్తి చేస్తుంది? మేము అనేక రంగుల మిశ్రమాన్ని పక్కన పెట్టి, ఒక రంగును మాత్రమే పరిగణించినట్లయితే, రంగు తారాగణం యొక్క కారణాలను చర్చించడం సులభం కావచ్చు. ఈ కథనం స్క్రీన్ ప్రింటింగ్లో రంగు విచలనాన్ని ప్రభావితం చేసే అనేక అంశాలను పంచుకుంటుంది. Youpin ప్యాకేజింగ్ మెటీరియల్ సిస్టమ్ను కొనుగోలు చేసి సరఫరా చేసే స్నేహితుల సూచన కోసం కంటెంట్:
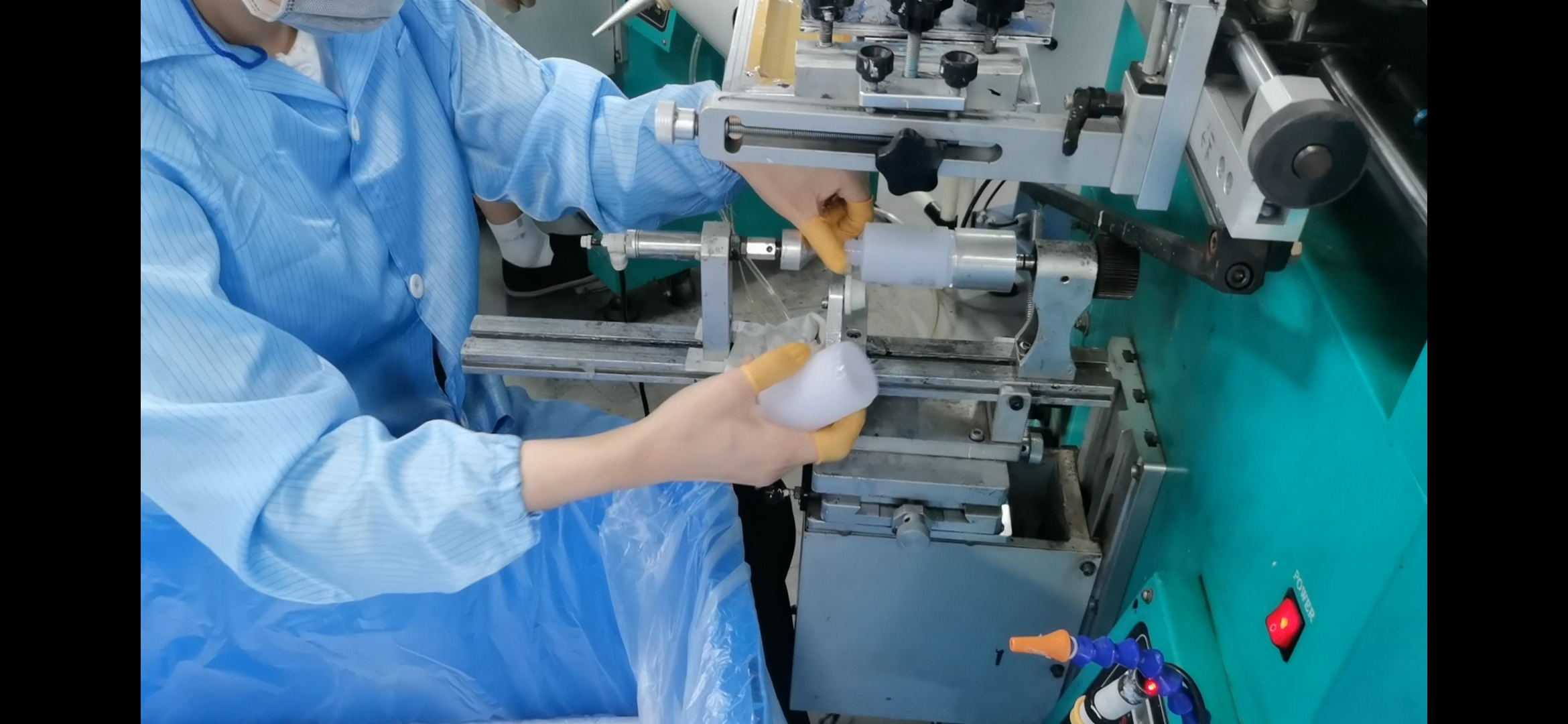
స్క్రీన్ ప్రింటింగ్ కలర్ కాస్ట్లను ఎందుకు ఉత్పత్తి చేస్తుంది? మేము అనేక రంగుల మిశ్రమాన్ని పక్కన పెట్టి, ఒక రంగును మాత్రమే పరిగణించినట్లయితే, రంగు తారాగణం యొక్క కారణాలను చర్చించడం సులభం కావచ్చు. ఈ కథనం స్క్రీన్ ప్రింటింగ్లో రంగు విచలనాన్ని ప్రభావితం చేసే అనేక అంశాలను పంచుకుంటుంది. Youpin ప్యాకేజింగ్ మెటీరియల్ సిస్టమ్ను కొనుగోలు చేసి సరఫరా చేసే స్నేహితుల సూచన కోసం కంటెంట్:
స్క్రీన్ ప్రింటింగ్లో రంగు విచలనానికి కారణమయ్యే కొన్ని సాధారణ కారకాలు క్రింద జాబితా చేయబడ్డాయి: సిరా తయారీ, మెష్ ఎంపిక, మెష్ టెన్షన్, ఒత్తిడి, ఎండబెట్టడం, ఉపరితల లక్షణాలు, పరిశీలన పరిస్థితులు మొదలైనవి.
01 ఇంక్ తయారీ
ఇంక్ బ్లెండింగ్ ఉపయోగించిన సిరా యొక్క వర్ణద్రవ్యం ఒక ప్రామాణిక వర్ణద్రవ్యం అని ఊహిస్తే, రంగు విచలనానికి అతిపెద్ద కారణం ఇంక్ మిక్సింగ్ ఆయిల్ వంటి ద్రావణాలను సిరాకు కలపడం. మంచి రంగు నియంత్రణ పరికరాలతో కూడిన వర్క్షాప్లో, నియంత్రణ పరికరాల ప్రకారం సిరా కలపవచ్చు. అయితే, చాలా ప్రింటింగ్ కంపెనీలకు ఈ సౌకర్యాలు ఉండటం అసాధ్యం. సిరా మిక్సింగ్ చేసేటప్పుడు వారు మాస్టర్ వర్కర్ల అనుభవంపై మాత్రమే ఆధారపడతారు.
సాధారణంగా, ఇంక్ని ప్రింటింగ్కు మరింత అనుకూలంగా చేయడానికి ఇంక్-సర్దుబాటు నూనె జోడించబడుతుంది. అయితే, సిరాకు సర్దుబాటు చేసే నూనెను జోడించిన తర్వాత, సిరాలోని వర్ణద్రవ్యం యొక్క గాఢత మారుతుంది, ఇది ప్రింటింగ్ సమయంలో సిరా యొక్క రంగు లక్షణాలలో మార్పులకు దారి తీస్తుంది. అదనంగా, సిరాలోని అదనపు ద్రావకం ఎండబెట్టడం తర్వాత సిరా యొక్క పలుచని పొరను ఏర్పరుస్తుంది, ఇది రంగు యొక్క ప్రకాశాన్ని తగ్గిస్తుంది.
సిరా వేయడానికి ముందు ఇంక్ పలచబడిన సమస్య కూడా ఉంది. ఉదాహరణకు, ఇంక్ షాప్లోని కార్మికులు సిరాను కలపడం లేదా పలుచన చేసేటప్పుడు వారి ఫార్ములా ఆధారంగా తీర్పులు ఇస్తారు. ఇది అనివార్యమైన రంగు విచలనానికి దారితీస్తుంది. కొద్దిరోజుల క్రితం సిరా కలిపితే, మంచి ఇంక్తో ప్రింట్ చేస్తే, ఈ పరిస్థితి వల్ల కలిగే రంగు మరింత స్పష్టంగా కనిపిస్తుంది. అందువల్ల, రంగు తారాగణాన్ని పూర్తిగా నివారించడం దాదాపు అసాధ్యం.
02 మెష్ ఎంపిక
స్క్రీన్ మెష్ పరిమాణం మాత్రమే ఇంక్ బదిలీని ప్రభావితం చేసే అంశం అని మీరు అనుకుంటే, మీరు చాలా ఇబ్బందులను ఎదుర్కొంటారు. మెష్ వ్యాసం మరియు ముడతలు కూడా సిరా బదిలీని ప్రభావితం చేస్తాయి. సాధారణంగా, స్క్రీన్ యొక్క ఇంక్ హోల్స్కు ఎక్కువ ఇంక్ జోడించబడితే, ప్రింటింగ్ ప్రక్రియలో ఎక్కువ ఇంక్ సబ్స్ట్రేట్కి బదిలీ చేయబడుతుంది.
ప్రతి మెష్ ద్వారా ఎంత సిరా బదిలీ చేయబడుతుందో ముందుగానే అంచనా వేయడానికి, చాలా మంది స్క్రీన్ సరఫరాదారులు ప్రతి మెష్ యొక్క సైద్ధాంతిక సిరా బదిలీ వాల్యూమ్ (TIV)ని అందిస్తారు. TIV అనేది స్క్రీన్ యొక్క ఇంక్ బదిలీ మొత్తం పరిమాణాన్ని సూచించే పరామితి. నిర్దిష్ట ప్రింటింగ్ పరిస్థితుల్లో ప్రతి మెష్ ద్వారా ఎంత ఇంక్ బదిలీ చేయబడుతుందో నిర్దిష్టంగా బదిలీ చేయబడిన ఇంక్ మొత్తాన్ని ఇది సూచిస్తుంది. దీని యూనిట్ యూనిట్ ప్రాంతానికి సిరా పరిమాణం.
ప్రింటింగ్లో స్థిరమైన టోన్లను నిర్ధారించడానికి, స్క్రీన్ యొక్క మెష్ సంఖ్యను మార్చకుండా ఉంచడం సరిపోదు, కానీ స్క్రీన్ యొక్క వ్యాసం మరియు దాని అలలు స్థిరంగా ఉండేలా చూసుకోవాలి. స్క్రీన్ యొక్క ఏదైనా పరామితిలో మార్పులు ప్రింటింగ్ సమయంలో ఇంక్ ఫిల్మ్ యొక్క మందంలో మార్పులకు దారితీస్తాయి, ఫలితంగా రంగు మార్పులు వస్తాయి.
03 నెట్ టెన్షన్
నెట్ యొక్క టెన్షన్ చాలా తక్కువగా ఉంటే, అది ఫిల్మ్ను పీల్ చేస్తుంది. మెష్లో ఎక్కువ సిరా ఉంటే, ముద్రించిన పదార్థం మురికిగా మారుతుంది.
స్క్రీన్ మరియు సబ్స్ట్రేట్ మధ్య దూరాన్ని పెంచడం ద్వారా ఈ సమస్యను పరిష్కరించవచ్చు. అయినప్పటికీ, స్క్రీన్ మరియు సబ్స్ట్రేట్ మధ్య దూరాన్ని పెంచడానికి ఒత్తిడిని పెంచడం అవసరం, ఇది మరింత సిరాను సబ్స్ట్రేట్కు బదిలీ చేయడానికి కారణమవుతుంది. రంగు యొక్క సాంద్రతను మార్చడానికి. స్ట్రెచ్ నెట్ యొక్క ఉద్రిక్తతను ఏకరీతిగా ఉంచడం ఉత్తమ మార్గం, తద్వారా రంగు యొక్క స్థిరత్వాన్ని నిర్ధారించడం.
04 ఒత్తిడి స్థాయి
స్థిరమైన రంగును నిర్వహించడానికి సరైన ఒత్తిడి సెట్టింగ్లు కీలకం, మరియు ప్రింటింగ్ ప్రక్రియలో ఏకరీతి ఒత్తిడి స్థాయిలను నిర్ధారించడం చాలా కీలకం. ముఖ్యంగా అధిక-వాల్యూమ్, పునరావృత ప్రింటింగ్ జాబ్లలో.
ఒత్తిడి విషయానికి వస్తే, స్క్వీజీ యొక్క కాఠిన్యాన్ని పరిగణించవలసిన మొదటి విషయం. స్క్వీజీ యొక్క కాఠిన్యం చిన్నది, ఇది సంప్రదింపు రేటుకు మంచిది, కానీ బెండింగ్ నిరోధకతకు ఇది మంచిది కాదు. కాఠిన్యం చాలా ఎక్కువగా ఉంటే, ప్రింటింగ్ సమయంలో స్క్రీన్పై రాపిడి కూడా పెద్దదిగా ఉంటుంది, తద్వారా ప్రింటింగ్ ఖచ్చితత్వాన్ని ప్రభావితం చేస్తుంది. రెండవది స్క్వీజీ యొక్క కోణం మరియు స్క్వీజీ వేగం. ఇంక్ కత్తి యొక్క కోణం సిరా బదిలీ మొత్తంపై గణనీయమైన ప్రభావాన్ని చూపుతుంది. ఇంక్ కత్తి యొక్క చిన్న కోణం, సిరా బదిలీ మొత్తం ఎక్కువ. ఇంక్ నైఫ్ వేగం చాలా వేగంగా ఉంటే, అది తగినంత ఇంక్ ఫిల్లింగ్ మరియు అసంపూర్ణ ముద్రణకు కారణమవుతుంది, తద్వారా ప్రింట్ నాణ్యతను ప్రభావితం చేస్తుంది.
మీరు ప్రింట్ జాబ్ కోసం సరైన ప్రెజర్ సెట్టింగ్లను పొంది, వాటిని ఖచ్చితంగా రికార్డ్ చేసిన తర్వాత, ప్రింటింగ్ ప్రక్రియలో మీరు ఈ సెట్టింగ్లను సరిగ్గా అనుసరించినంత కాలం, మీరు స్థిరమైన రంగులతో సంతృప్తికరమైన ప్రింట్ ఉత్పత్తిని పొందుతారు.
05 పొడి
కొన్నిసార్లు, రంగు ముద్రించిన తర్వాత స్థిరంగా కనిపిస్తుంది, కానీ తుది ఉత్పత్తి కనుగొనబడిన తర్వాత రంగు మారుతుంది. ఇది తరచుగా ఎండబెట్టడం పరికరాలు యొక్క తప్పు సెట్టింగుల వలన సంభవిస్తుంది. అత్యంత సాధారణ కారణం ఏమిటంటే, డ్రైయర్ ఉష్ణోగ్రత చాలా ఎక్కువగా సెట్ చేయబడి, కాగితం లేదా కార్డ్బోర్డ్పై సిరా రంగు మారడానికి కారణమవుతుంది.
06 ఉపరితల లక్షణాలు
స్క్రీన్ ప్రింటింగ్ మాస్టర్లు తరచుగా పట్టించుకోని ఒక సమస్య సబ్స్ట్రేట్ యొక్క ఉపరితల లక్షణాలు. కాగితం, కార్డ్బోర్డ్, ప్లాస్టిక్ మొదలైనవన్నీ బ్యాచ్లలో ఉత్పత్తి చేయబడతాయి మరియు అధిక-నాణ్యత ఉపరితలాలు స్థిరమైన మరియు స్థిరమైన ఉపరితల లక్షణాలను నిర్ధారించగలవు. అయితే ఇది అలా కాదు. ఉపరితలం యొక్క ఉపరితల లక్షణాలలో చిన్న మార్పులు ప్రింటింగ్లో రంగు వ్యత్యాసాలను కలిగిస్తాయి. ప్రింటింగ్ ఒత్తిడి ఏకరీతిగా ఉన్నప్పటికీ మరియు ప్రతి ప్రక్రియ సరిగ్గా నిర్వహించబడినప్పటికీ, ఉపరితలం యొక్క ఉపరితల లక్షణాలలో అసమానతలు కూడా ప్రింటింగ్లో పెద్ద రంగు మార్పులకు కారణమవుతాయి. రంగు తారాగణం.
ఒకే ఉత్పత్తిని ఒకే ప్రింటింగ్ పరికరాలతో వేర్వేరు ఉపరితలాలపై ముద్రించినప్పుడు, రంగుపై ఉపరితలం యొక్క ఉపరితల లక్షణాల ప్రభావం ప్రత్యేకంగా ఉంటుంది. కస్టమర్లు విండో ప్రకటనలను ప్లాస్టిక్ లేదా ఇతర కార్డ్బోర్డ్పై ముద్రించవలసి ఉంటుంది. మరియు ఖాతాదారులకు ఒకే భాగానికి స్థిరమైన రంగులు అవసరం కావచ్చు.
ఇలాంటి పరిస్థితుల్లో, ఖచ్చితమైన రంగు కొలతలు చేయడం మాత్రమే పరిష్కారం. రంగు సాంద్రతను కొలవడానికి స్పెక్ట్రోఫోటోమీటర్ లేదా స్పెక్ట్రల్ డెన్సిటోమీటర్ ఉపయోగించండి. రంగు మార్పు ఉంటే, డెన్సిటోమీటర్ దానిని స్పష్టంగా ప్రతిబింబిస్తుంది మరియు మీరు ఇతర ప్రక్రియలను నియంత్రించడం ద్వారా ఈ రంగు మార్పును అధిగమించవచ్చు.
07 పరిశీలన పరిస్థితులు
మానవ కళ్ళు రంగులో సూక్ష్మమైన మార్పులకు చాలా సున్నితంగా ఉంటాయి మరియు కాంతి పరిస్థితులలో మాత్రమే రంగులను వేరు చేయగలవు. దీని కారణంగా, అదే లైటింగ్ పరిస్థితుల్లో రంగులను సరిపోల్చండి. లేకపోతే, ఇంక్ వాల్యూమ్ లేదా ప్రెజర్ సర్దుబాటు చేయడం వల్ల ఎక్కువ ఇంక్ ఉత్పత్తి అవుతుంది. పెద్ద రంగు తారాగణం.
మొత్తం మీద, సిరా యొక్క స్థిరమైన పనితీరును నిర్ధారించడానికి ప్రతి ప్రక్రియ యొక్క స్థిరమైన నియంత్రణలో స్థిరమైన రంగును నిర్వహించడానికి కీ ఉంటుంది. మెష్ పరిమాణం ఎంపిక, టెన్షన్ మరియు స్ట్రెచ్ స్క్రీన్ యొక్క పీడనం, ఉపరితలం యొక్క ఉపరితల లక్షణాలు మరియు పరిశీలన పరిస్థితులు రంగు విచలనంపై నిర్దిష్ట ప్రభావాన్ని చూపుతాయి. అయినప్పటికీ, ఖచ్చితమైన సెట్టింగ్ రికార్డులు మరియు ప్రతి ప్రక్రియ యొక్క స్థిరమైన నియంత్రణ స్థిరమైన స్క్రీన్ ప్రింటింగ్ రంగులను నిర్ధారించడానికి కీలకమైనవి.
పోస్ట్ సమయం: జనవరి-08-2024