اسکرین پرنٹنگ رنگین کاسٹ کیوں پیدا کرتی ہے؟ اگر ہم کئی رنگوں کے مرکب کو ایک طرف رکھ کر صرف ایک رنگ پر غور کریں تو رنگ کاسٹ کی وجوہات پر بات کرنا آسان ہو سکتا ہے۔ یہ مضمون کئی عوامل کا اشتراک کرتا ہے جو اسکرین پرنٹنگ میں رنگ کے انحراف کو متاثر کرتے ہیں۔ مواد ان دوستوں کے حوالے کے لیے ہے جو یوپین پیکیجنگ میٹریل سسٹم خریدتے اور سپلائی کرتے ہیں:
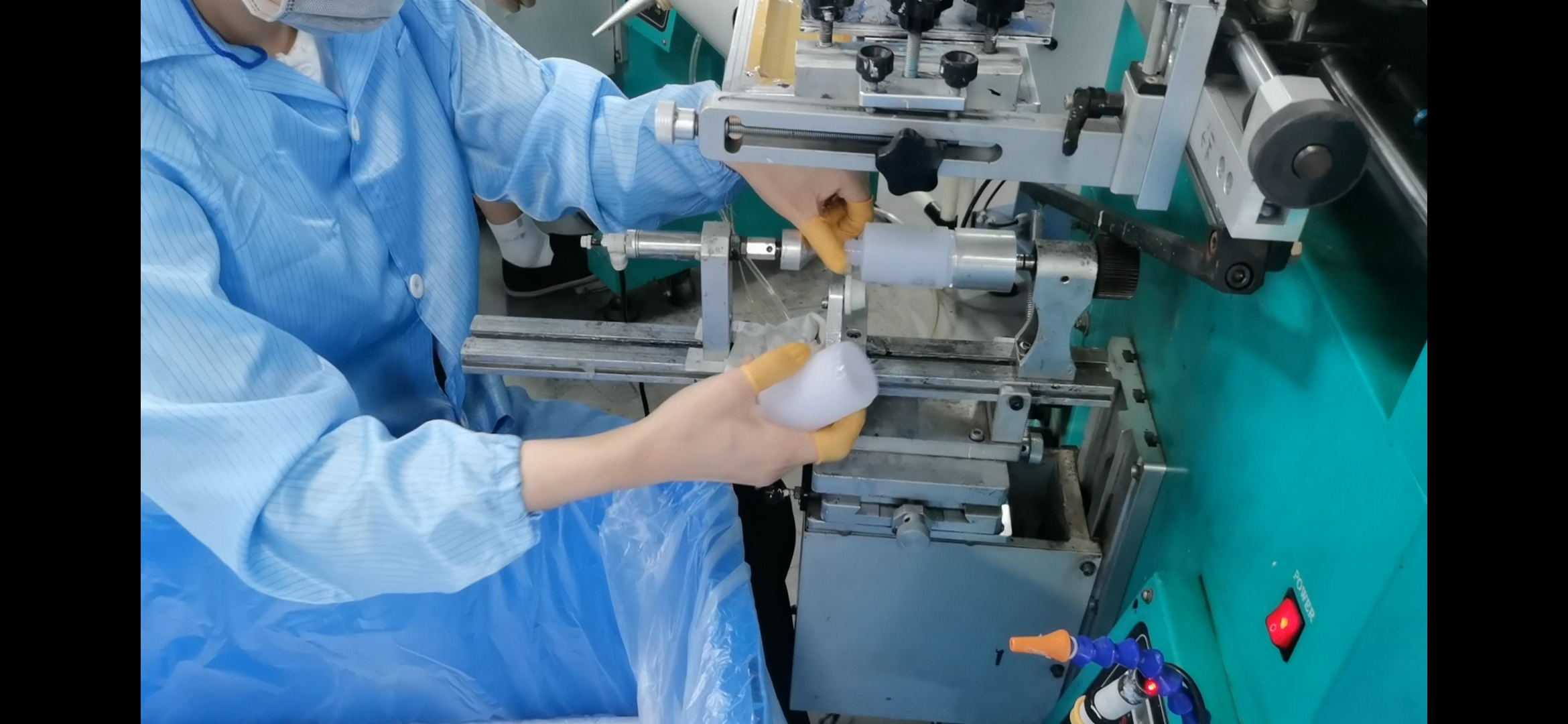
اسکرین پرنٹنگ رنگین کاسٹ کیوں پیدا کرتی ہے؟ اگر ہم کئی رنگوں کے مرکب کو ایک طرف رکھ کر صرف ایک رنگ پر غور کریں تو رنگ کاسٹ کی وجوہات پر بات کرنا آسان ہو سکتا ہے۔ یہ مضمون کئی عوامل کا اشتراک کرتا ہے جو اسکرین پرنٹنگ میں رنگ کے انحراف کو متاثر کرتے ہیں۔ مواد ان دوستوں کے حوالے کے لیے ہے جو یوپین پیکیجنگ میٹریل سسٹم خریدتے اور سپلائی کرتے ہیں:
اسکرین پرنٹنگ میں رنگ کے انحراف کا سبب بننے والے چند عام عوامل ذیل میں درج ہیں: سیاہی کی تیاری، میش کا انتخاب، میش ٹینشن، پریشر، خشک ہونا، سبسٹریٹ کی خصوصیات، مشاہدے کے حالات وغیرہ۔
01 سیاہی کی تیاری
سیاہی کی ملاوٹ یہ فرض کرتے ہوئے کہ استعمال کی جانے والی سیاہی کا روغن ایک معیاری روغن ہے، رنگ کے انحراف کی سب سے بڑی وجہ سیاہی میں انک مکسنگ آئل جیسے سالوینٹس کا اضافہ ہے۔ اچھے رنگ کنٹرول آلات کے ساتھ ایک ورکشاپ میں، سیاہی کو کنٹرول آلات کے مطابق ملایا جا سکتا ہے. تاہم، زیادہ تر پرنٹنگ کمپنیوں کے لیے یہ سہولیات حاصل کرنا ناممکن ہے۔ سیاہی ملاتے وقت وہ صرف ماسٹر ورکرز کے تجربے پر بھروسہ کرتے ہیں۔
عام طور پر، سیاہی کو ایڈجسٹ کرنے والا تیل سیاہی کو پرنٹنگ کے لیے زیادہ موزوں بنانے کے لیے شامل کیا جاتا ہے۔ تاہم، سیاہی میں تیل کو ایڈجسٹ کرنے کے بعد، سیاہی میں روغن کا ارتکاز بدل جائے گا، جو پرنٹنگ کے دوران سیاہی کے رنگ کی خصوصیات میں تبدیلی کا باعث بنے گا۔ اس کے علاوہ، سیاہی میں زیادہ سالوینٹ خشک ہونے کے بعد سیاہی کی ایک پتلی فلم بنائے گا، جس سے رنگ کی چمک کم ہو جائے گی۔
سیاہی لگانے سے پہلے سیاہی پتلی ہونے کا مسئلہ بھی ہے۔ مثال کے طور پر، سیاہی کی دکان کے کارکن سیاہی کو ملاتے یا پتلا کرتے وقت اپنے فارمولے کی بنیاد پر فیصلے کرتے ہیں۔ یہ ناگزیر رنگ انحراف کی طرف جاتا ہے. اگر سیاہی کو کچھ دن پہلے ملایا جاتا ہے، اگر آپ اچھی سیاہی سے پرنٹ کرتے ہیں، تو اس صورت حال کی وجہ سے رنگ کاسٹ زیادہ واضح ہوگا۔ لہذا، رنگ کاسٹ سے مکمل طور پر بچنا تقریباً ناممکن ہے۔
02 میش سلیکشن
اگر آپ سوچتے ہیں کہ اسکرین کا میش سائز واحد عنصر ہے جو سیاہی کی منتقلی کو متاثر کرتا ہے، تو آپ کو کافی پریشانی کا سامنا کرنا پڑے گا۔ میش قطر اور جھریاں بھی سیاہی کی منتقلی کو متاثر کرتی ہیں۔ عام طور پر، اسکرین کے سیاہی کے سوراخوں سے جتنی زیادہ سیاہی جڑی ہوگی، پرنٹنگ کے عمل کے دوران اتنی ہی زیادہ سیاہی سبسٹریٹ میں منتقل کی جائے گی۔
پہلے سے اندازہ لگانے کے لیے کہ ہر میش کے ذریعے کتنی سیاہی منتقل کی جا سکتی ہے، بہت سے سکرین فراہم کنندگان ہر میش کی نظریاتی سیاہی کی منتقلی والیوم (TIV) فراہم کرتے ہیں۔ TIV ایک پیرامیٹر ہے جو اسکرین کی سیاہی کی منتقلی کی مقدار کو ظاہر کرتا ہے۔ اس سے مراد ایک مخصوص میں منتقل کی جانے والی سیاہی کی مقدار ہے جس میں پرنٹنگ کے مخصوص حالات کے تحت ہر میش کے ذریعے کتنی سیاہی منتقل کی جائے گی۔ اس کی اکائی سیاہی کا حجم فی یونٹ رقبہ ہے۔
پرنٹنگ میں یکساں ٹونز کو یقینی بنانے کے لیے، اسکرین کے میش نمبر کو غیر تبدیل شدہ رکھنا کافی نہیں ہے، بلکہ یہ بھی یقینی بنانا ہے کہ اسکرین کا قطر اور اس کی لہریں مستقل رہیں۔ اسکرین کے کسی بھی پیرامیٹر میں تبدیلی کے نتیجے میں پرنٹنگ کے دوران سیاہی کی فلم کی موٹائی میں تبدیلیاں آئیں گی، جس کے نتیجے میں رنگ بدل جائے گا۔
03 نیٹ تناؤ
اگر نیٹ کا تناؤ بہت چھوٹا ہے، تو یہ فلم کو چھیلنے کا سبب بنے گا۔ اگر جالی میں بہت زیادہ سیاہی رہ جائے تو چھپی ہوئی چیز گندی ہو جائے گی۔
اس مسئلے کو سکرین اور سبسٹریٹ کے درمیان فاصلہ بڑھا کر حل کیا جا سکتا ہے۔ تاہم، اسکرین اور سبسٹریٹ کے درمیان فاصلہ بڑھانے کے لیے دباؤ بڑھانے کی ضرورت ہوتی ہے، جس کی وجہ سے سبسٹریٹ میں زیادہ سیاہی منتقل ہوتی ہے۔ رنگ کی کثافت کو تبدیل کرنے کے لیے۔ بہترین طریقہ یہ ہے کہ اسٹریچ نیٹ کے تناؤ کو یکساں رکھا جائے، تاکہ رنگ کی مستقل مزاجی کو یقینی بنایا جا سکے۔
04 پریشر کی سطح
مستقل رنگ کو برقرار رکھنے کے لیے دباؤ کی مناسب ترتیبات بہت اہم ہیں، اور پرنٹنگ کے عمل کے دوران دباؤ کی یکساں سطح کو یقینی بنانا بہت ضروری ہے۔ خاص طور پر اعلی حجم، بار بار پرنٹنگ کی نوکریوں میں۔
جب دباؤ کی بات آتی ہے تو، غور کرنے کی پہلی چیز squeegee کی سختی ہے۔ squeegee کی سختی چھوٹی ہے، جو رابطہ کی شرح کے لیے اچھا ہے، لیکن یہ موڑنے والی مزاحمت کے لیے اچھا نہیں ہے۔ اگر سختی بہت زیادہ ہے تو، پرنٹنگ کے دوران اسکرین پر رگڑ بھی بڑی ہوگی، اس طرح پرنٹنگ کی درستگی کو متاثر کرے گا. دوسرا squeegee اور squeegee کی رفتار کا زاویہ ہے۔ سیاہی چاقو کا زاویہ سیاہی کی منتقلی کی مقدار پر نمایاں اثر رکھتا ہے۔ سیاہی چاقو کا زاویہ جتنا چھوٹا ہوگا، سیاہی کی منتقلی کی مقدار اتنی ہی زیادہ ہوگی۔ اگر سیاہی چاقو کی رفتار بہت تیز ہے، تو یہ ناکافی سیاہی بھرنے اور نامکمل نقوش کا سبب بنے گی، اس طرح پرنٹ کے معیار کو متاثر کرے گا۔
ایک بار جب آپ پرنٹ جاب کے لیے دباؤ کی درست ترتیبات حاصل کر لیتے ہیں اور انہیں درست طریقے سے ریکارڈ کر لیتے ہیں، جب تک کہ آپ پرنٹنگ کے عمل کے دوران ان ترتیبات کو درست طریقے سے فالو کرتے ہیں، آپ کو ایک تسلی بخش پرنٹ پروڈکٹ مل جائے گا جس میں ہم آہنگ رنگ ہیں۔
05 خشک
بعض اوقات، رنگ صرف پرنٹنگ کے بعد ہی نظر آتا ہے، لیکن تیار شدہ مصنوعات کے ملنے کے بعد رنگ بدل جاتا ہے۔ یہ اکثر خشک کرنے والے آلات کی غلط ترتیبات کی وجہ سے ہوتا ہے۔ سب سے عام وجہ یہ ہے کہ ڈرائر کا درجہ حرارت بہت زیادہ ہے، جس کی وجہ سے کاغذ یا گتے پر سیاہی کا رنگ بدل جاتا ہے۔
06 سبسٹریٹ کی خصوصیات
ایک مسئلہ جسے اسکرین پرنٹنگ ماسٹر اکثر نظر انداز کرتے ہیں وہ ہے سبسٹریٹ کی سطحی خصوصیات۔ کاغذ، گتے، پلاسٹک وغیرہ سبھی بیچوں میں تیار کیے جاتے ہیں، اور اعلیٰ معیار کے ذیلی ذخائر مستحکم اور مستقل سطح کی خصوصیات کو یقینی بنا سکتے ہیں۔ لیکن ایسا نہیں ہے۔ سبسٹریٹ کی سطح کی خصوصیات میں چھوٹی تبدیلیاں پرنٹنگ میں رنگین انحراف کا سبب بنیں گی۔ یہاں تک کہ اگر پرنٹنگ کا دباؤ یکساں ہے اور یہاں تک کہ ہر عمل کو درست طریقے سے چلایا جاتا ہے، تب بھی سبسٹریٹ کی سطح کی خصوصیات میں تضادات بھی پرنٹنگ میں رنگوں کی بڑی تبدیلیوں کا سبب بنیں گے۔ رنگین کاسٹ۔
جب ایک ہی پروڈکٹ کو ایک ہی پرنٹنگ آلات کے ساتھ مختلف سبسٹریٹس پر پرنٹ کیا جاتا ہے، تو رنگ پر سبسٹریٹ کی سطحی خصوصیات کا اثر خاص طور پر واضح ہوتا ہے۔ صارفین کو کھڑکی کے اشتہارات پلاسٹک یا دوسرے گتے پر پرنٹ کرنے کی ضرورت پڑ سکتی ہے۔ اور گاہکوں کو ایک ہی ٹکڑے کے لئے مستقل رنگوں کی ضرورت ہوسکتی ہے۔
اس طرح کے حالات میں، واحد حل رنگ کی درست پیمائش کرنا ہے۔ رنگ کی کثافت کی پیمائش کرنے کے لیے سپیکٹرو فوٹومیٹر یا سپیکٹرل ڈینسیٹو میٹر کا استعمال کریں۔ اگر رنگ کی تبدیلی ہوتی ہے، تو کثافت میٹر اسے واضح طور پر ظاہر کر سکتا ہے، اور آپ دوسرے عمل کو کنٹرول کر کے اس رنگ کی تبدیلی پر قابو پا سکتے ہیں۔
07 مشاہدے کے حالات
انسانی آنکھیں رنگ میں باریک تبدیلیوں کے لیے بہت حساس ہوتی ہیں، اور صرف روشنی کے حالات میں ہی رنگوں میں فرق کر سکتی ہیں۔ اس کی وجہ سے، ایک ہی روشنی کے حالات میں رنگوں کا موازنہ کرنا یقینی بنائیں۔ دوسری صورت میں، سیاہی کے حجم یا دباؤ کو ایڈجسٹ کرنے سے زیادہ سیاہی پیدا ہوگی۔ بڑی رنگین کاسٹ۔
مجموعی طور پر، مستقل رنگ کو برقرار رکھنے کی کلید سیاہی کی مستحکم کارکردگی کو یقینی بنانے کے لیے ہر عمل کے مستحکم کنٹرول میں ہے۔ میش سائز کا انتخاب، اسٹریچ اسکرین کا تناؤ اور دباؤ، سبسٹریٹ کی سطح کی خصوصیات اور مشاہدے کے حالات ان سب کا رنگ انحراف پر ایک خاص اثر پڑتا ہے۔ تاہم، درست ترتیب کے ریکارڈ اور ہر عمل کا مستحکم کنٹرول اسکرین پرنٹنگ کے رنگوں کو یقینی بنانے کی کلیدیں ہیں۔
پوسٹ ٹائم: جنوری-08-2024